Hey there! If you're looking for a smooth and efficient way to keep your inventory updated, you've come to the right place. We understand the challenges of managing stock levels and ensuring that everything runs like clockwork. In this article, weâll share a simple but effective letter template for inventory replenishment updates that you can easily tailor to your business needsâso stick around to learn more!
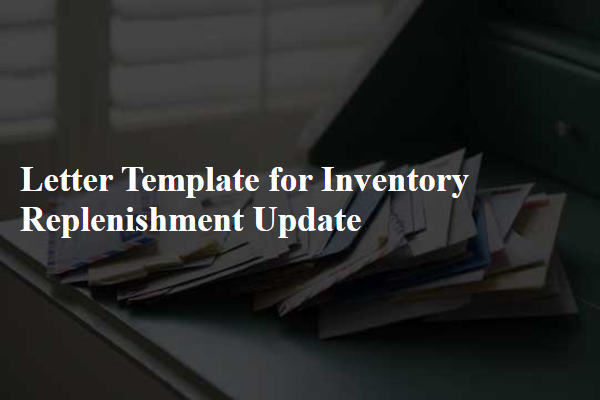
Inventory Levels
Inventory levels play a crucial role in the operational efficiency of businesses, particularly in retail stores and supply chain management. Accurate monitoring of stock quantities, often measured in units or cases, ensures that products like electronics, clothing, and food items remain available to meet customer demand. A significant drop in inventory levels below the safety stock threshold -- typically a predetermined minimum quantity -- can trigger replenishment orders to suppliers and manufacturers. For example, a grocery store may need to reorder perishable items such as dairy or produce if inventory levels fall below a specified number, ensuring fresh stock is available at locations like supermarkets or convenience stores. An effective inventory replenishment strategy can reduce the risk of stockouts and enhance overall customer satisfaction.
Supplier Collaboration
Inventory replenishment updates are crucial for maintaining supply chain efficiency in businesses such as retail operations and manufacturing plants. Collaboration with suppliers, such as prominent companies like Fastenal or Grainger, can enhance the accuracy of stock levels. Regular communication about inventory thresholds, typically 20% of total stock levels, alerts suppliers to potential shortages. This proactive approach ensures that product categories, such as electronics or raw materials, are restocked in a timely manner, minimizing disruption. Utilizing inventory management software, like SAP or Oracle, streamlines the process, allowing for real-time updates and data-driven decisions regarding order quantities and delivery schedules.
Order Processing Time
Timely inventory replenishment is crucial for maintaining operational efficiency in businesses. Order processing time refers to the duration needed to handle an inventory order from initiation to fulfillment. In many industries, such as retail and manufacturing, average order processing times can vary significantly--typically ranging from 24 to 72 hours depending on supplier location and stock availability. Companies rely on effective communication systems to track these timelines, ensuring that products such as electronics or food items reach distribution centers on schedule. Delays in processing can lead to stockouts, affecting sales and customer satisfaction, particularly during peak seasons like holidays or sales events. Regular updates on order processing times help businesses adjust their inventory strategies accordingly.
Demand Forecasting
Effective demand forecasting requires analyzing historical sales data, market trends, and consumer behavior to ensure optimal inventory levels. Accurate predictions can help businesses maintain sufficient stock while minimizing excess inventory and storage costs. Utilizing forecasting tools, such as machine learning algorithms, companies can harness data from various sources, including sales reports from the previous quarter or demographic insights from market research. Timely inventory replenishment processes are crucial for sectors like retail, where fluctuations in demand can significantly impact sales performance at crucial times, such as holidays or special promotions, influencing the bottom line. Monitoring key performance indicators (KPIs) related to inventory turnover rates and order fulfillment can drive improvements in forecasting accuracy and operational efficiency.
Stock Management Systems
Effective inventory replenishment plays a critical role in optimizing supply chain efficiency within modern Stock Management Systems (SMS). Accurate data tracking is essential, allowing businesses to maintain optimal stock levels, preventing overstock or stockouts. For instance, a retail chain utilizing a comprehensive SMS can automate reorder points based on sales velocity data, ensuring timely replenishments. Furthermore, advanced algorithms within these systems facilitate demand forecasting by analyzing historical sales trends (e.g., last year's monthly data, seasonal fluctuations), enhancing accuracy in inventory planning. Implementing a robust inventory management solution can significantly improve cash flow by reducing excess inventory storage costs while ensuring product availability for customer satisfaction.
Comments