Are you looking to elevate your organization with robust quality assurance standards? Implementing effective QA practices not only enhances product reliability but also builds trust with your customers. In this article, weâll explore essential components of a quality assurance letter template that can streamline communication and ensure compliance with industry regulations. So grab a cup of coffee and dive into how you can apply these insights to improve your operations!
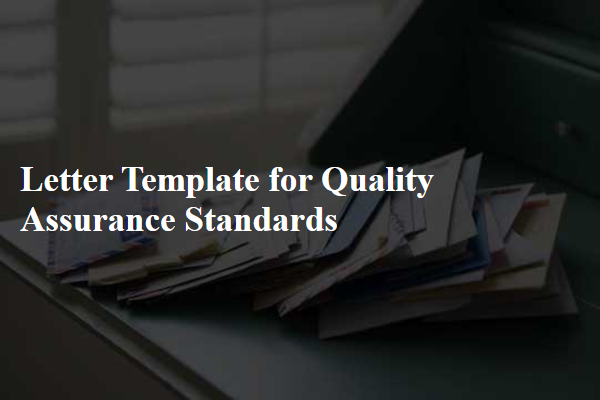
Compliance with industry regulations
Compliance with industry regulations is crucial for maintaining quality assurance standards in various sectors. Regulatory bodies, such as the Occupational Safety and Health Administration (OSHA) in the United States, enforce guidelines that ensure workplace safety and health standards are met, protecting employees and customers alike. Additionally, the International Organization for Standardization (ISO) provides frameworks like ISO 9001, which outlines the criteria for a quality management system. Adherence to these standards helps organizations avoid potential legal issues, improve operational efficiency, and enhance customer satisfaction by delivering products and services that meet or exceed expectations. Regular audits and assessments are essential processes for organizations to ensure compliance, enabling them to identify gaps, mitigate risks, and implement necessary improvements.
Consistent quality control processes
Consistent quality control processes are essential for ensuring products meet established standards in manufacturing environments. This involves regular inspections, typically conducted at various production stages, such as raw material sourcing, in-process manufacturing, and final product evaluation. Statistical process control (SPC) methods often utilize numerical data and control charts to monitor variations in production. Quality assurance teams commonly implement Standard Operating Procedures (SOPs) to provide clear guidelines for testing and measuring product quality. For example, ISO 9001 certification outlines criteria for an effective Quality Management System (QMS), focusing on customer satisfaction and continuous improvement. Furthermore, utilizing advanced technologies such as automated inspection systems or machine learning algorithms can enhance efficiency and accuracy in detecting defects, thus minimizing costly reworks and ensuring a high-quality output in compliance with regulatory standards.
Effective communication channels
Effective communication channels play a crucial role in maintaining quality assurance standards within organizations. Clear pathways for information exchange--such as emails, project management tools like Asana or Trello, and instant messaging platforms like Slack--ensure that team members are aligned on project goals and quality metrics. Regular meetings, such as weekly check-ins, facilitate real-time feedback, while formal documentation processes ensure that vital information regarding standards, such as ISO 9001, is readily accessible. Moreover, utilizing customer feedback channels, like surveys or user testing forums, can provide insights into product quality and areas needing improvement, reinforcing the continuous improvement cycle that is fundamental to quality assurance practices.
Continuous improvement strategies
Quality assurance standards demand continuous improvement strategies to enhance operational efficiency. Regular assessments (quarterly or bi-annually) of internal processes identify bottlenecks, fostering an agile workforce. Implementing frameworks such as Six Sigma or Lean methodologies can streamline production, minimize waste, and reduce defects. Employee training programs focused on quality control principles, like Statistical Process Control (SPC), equip staff with tools to maintain high standards. Utilizing feedback loops from customers, collected through surveys or online reviews, informs product development, ensuring alignment with market expectations. Moreover, benchmarking against industry leaders like Toyota or Motorola highlights best practices that inspire innovation. This cyclical commitment to improvement not only elevates product quality but also enhances customer satisfaction, driving brand loyalty and business growth.
Documentation and record-keeping practices
Quality assurance standards emphasize thorough documentation and meticulous record-keeping practices. These processes are vital in industries such as pharmaceuticals and manufacturing, where compliance with regulations from entities like the Food and Drug Administration (FDA) or the International Organization for Standardization (ISO) is mandatory. Detailed records, including Standard Operating Procedures (SOPs), inspection reports, and corrective action logs, ensure traceability and accountability. For instance, batch records in a pharmaceutical context must include specific data such as batch numbers, ingredients, and testing results to validate product quality. Furthermore, maintaining accurate records assists in audits, facilitates training processes, and supports continuous improvement initiatives, aligning with best practices and regulatory expectations.
Comments