Are you looking for a clear and effective way to communicate necessary changes in material costs to your clients? Crafting a letter for material cost adjustments doesnât have to be daunting; it simply requires a blend of clarity and professionalism. Whether you aim to explain reasons for the increase or provide reassurance about your commitment to quality, the right words can make all the difference. Read on to discover an adaptable template that will guide you in making your communication seamless and straightforward!
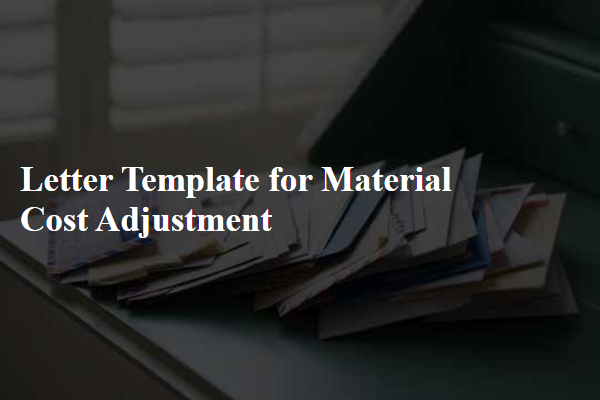
Clear Subject Line
In construction projects, material cost adjustments can significantly impact budgeting and financial planning. Accurate tracking of material prices, such as concrete (averaging $120 per cubic yard) and steel (approximately $850 per ton), is essential for maintaining budget integrity. Changes in supplier pricing due to market fluctuations or unexpected supply chain disruptions can necessitate adjustments. For instance, a spike in demand for lumber (recently reaching $700 per thousand board feet) can lead to sudden price increases, affecting overall project costs. Effective communication of these adjustments ensures all stakeholders, especially project managers in urban areas like New York City or Los Angeles, understand financial implications and can make informed decisions regarding resource allocation.
Current Cost Analysis
Material cost adjustments play a crucial role in supply chain management, significantly impacting financial outcomes. Recent studies indicate that the cost of raw materials, such as steel and aluminum, has surged by approximately 30% over the past year due to global supply chain disruptions. Analyzing current material costs involves evaluating supplier pricing, market demand, and fluctuations in currency rates. For instance, the U.S. dollar's performance against the euro has affected import costs for European suppliers. In manufacturing hubs like Shenzhen, China, labor shortages and increased operational costs have also contributed to rising prices. Tracking these metrics helps businesses make informed decisions about material procurement, ultimately affecting production budgets and pricing strategies.
Justification for Adjustment
Material cost adjustments arise due to factors impacting production expenses, such as increased raw material prices, supply chain disruptions, and fluctuations in currency exchange rates. For instance, in Q2 2023, global steel prices surged by 30% amid rising demand and limited supply from major producers like China and India. Additionally, January 2023 brought significant logistical challenges in transportation, leading to heightened delivery fees, further straining budgets. Persistent inflation trends, with the Consumer Price Index (CPI) reaching 8.5% year-over-year in some regions, exacerbate these cost pressures. Adjusting material costs is essential to maintain financial stability, ensure competitive pricing, and sustain quality standards in production.
Proposed New Rates
Proposed new rates for material costs impact project budgets significantly. For construction projects in urban areas, such as New York City, typical materials like concrete and steel experienced price increases of 10% to 15% from January 2022 to October 2023 due to inflation and supply chain disruptions. Local suppliers often adjust rates quarterly based on market trends, impacting financial planning. Effective evaluation of new rates involves analyzing historical price fluctuations, regional demand, and competition among suppliers. Accurate cost adjustments enhance project feasibility and ensure profitability. Client communication regarding changes is essential for maintaining transparency and trust.
Implementation Timeline
Material cost adjustments significantly impact project budgeting, particularly in construction and manufacturing sectors, where pricing fluctuates due to market volatility. Notable events influencing costs include trade tariffs imposed in recent years, affecting materials like steel and aluminum, which may see an increase of 10-25% depending on supplier contracts. Implementing adjustments requires a structured timeline, typically spanning 30 to 90 days, allowing stakeholders--project managers, procurement teams, and finance departments--to assess impacts, negotiate supplier contracts, and communicate changes to clients. Specific milestones during this period should include budget reviews, stakeholder consultations, and updated project forecasts, ensuring all parties are aligned with new material pricing and timelines for procurement.
Comments