In today's fast-paced construction industry, managing risks effectively is more crucial than ever. Whether you're overseeing a large-scale project or a small renovation, understanding potential obstacles can mean the difference between success and costly delays. This proposal outlines key strategies for risk mitigation tailored specifically to our upcoming project, ensuring that we proactively address challenges before they arise. Ready to discover how these solutions can safeguard our work and enhance efficiency? Let's dive in!
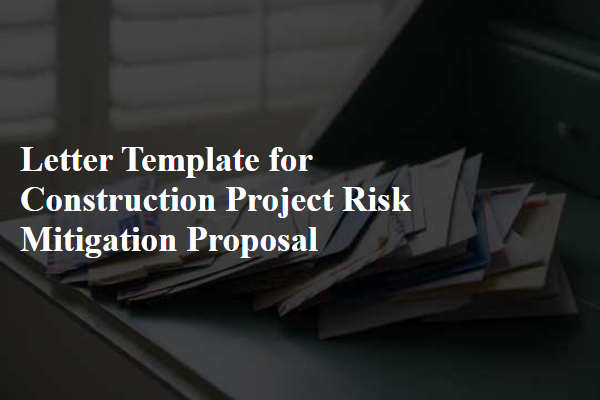
Project Overview and Objectives
The construction project, located at the downtown development site of Springfield, aims to create a state-of-the-art convention center with a targeted completion date of December 2024. The primary objective includes minimizing delays and budget overruns, ensuring an efficient workflow throughout the phases of design, procurement, and construction. Key components of risk mitigation involve comprehensive safety protocols due to the high foot traffic in the urban area, adherence to local building codes, and effective management of supply chain disruptions, particularly focusing on critical materials such as steel and concrete. Additionally, the project will utilize advanced risk assessment tools, involving real-time data analytics to identify potential hazards and devise proactive strategies, ensuring the safety of workers and the integrity of the surrounding infrastructure.
Identified Risks and Potential Impacts
Identified risks in construction projects, such as scheduling delays and safety hazards, can significantly impact project timelines and budgets. Potential impacts of scheduling delays may include increased labor costs, estimated at 10% higher for each week of delay, and potential penalties from clients due to missed deadlines. Safety hazards, including falls (the leading cause of construction-related injuries), can result in costly medical expenses and legal liabilities, which can range from thousands to millions of dollars depending on the severity. Furthermore, adverse weather conditions during peak seasons, such as summer storms or winter snow, can halt work and delay progress, affecting overall project delivery timelines. Implementing comprehensive risk management strategies, such as thorough safety training and robust weather monitoring systems, can help mitigate these identified risks effectively, ultimately safeguarding project success.
Proposed Mitigation Strategies
The proposed mitigation strategies for construction project risks, including financial loss and schedule delays, focus on comprehensive planning and proactive management. Enhanced project scheduling techniques, such as Critical Path Method (CPM), can identify potential delays early, allowing for timely intervention. Regular risk assessment meetings, ideally held bi-weekly, can facilitate continuous monitoring of risk factors like labor shortages, material costs, or regulatory changes. Implementation of robust supply chain management practices can minimize disruptions, particularly with fluctuating raw material prices, such as steel increasing by 20% in the last year. Training programs for workers on safety protocols can significantly reduce workplace accidents, promoting a secure environment and adhering to OSHA regulations. Utilizing advanced project management software can further streamline communication and documentation processes, ensuring all stakeholders are informed and aligned with project objectives.
Implementation Timeline and Responsibilities
The implementation timeline for the construction project risk mitigation strategy outlines a series of key milestones, ranging from initial risk assessment to final project completion. The risk assessment phase, lasting two weeks, will involve the identification of potential risks such as material shortages, labor disputes, and adverse weather conditions. Following this, a detailed risk management plan will be developed and presented to stakeholders within one month, specifying measures to address each identified risk. Responsibilities will be assigned to project managers, safety officers, and field supervisors, ensuring accountability. During the construction phase, which spans six months, regular risk review meetings will be conducted bi-weekly to monitor the effectiveness of mitigation measures. The final phase involves a comprehensive project evaluation, scheduled for one month after completion, to assess the success of the implemented strategies and prepare lessons learned for future projects.
Monitoring and Evaluation Plan
A comprehensive Monitoring and Evaluation Plan (M&E Plan) is essential for the effective management of construction project risks, particularly in large-scale developments like urban infrastructure projects. This plan outlines specific parameters for systematic tracking of project milestones, such as completion percentage, and adherence to budgetary constraints (typically within a 10% variance). Key stakeholders include project managers, quality assurance teams, and local regulatory bodies, all of whom regularly assess risk factors such as safety compliance (aligned with OSHA standards), environmental impact (focusing on flora and fauna preservation), and schedule delays (aiming for a maximum of 5% increase in timelines). Data collection methods incorporate real-time monitoring technologies (e.g., drones for site surveys) and regular site inspections, enabling quick identification of potential issues. The evaluation aspect measures project outcomes against established benchmarks, ensuring risks are managed proactively through adaptive management strategies and continuous stakeholder engagement throughout the construction process. The M&E plan serves not only as a risk mitigation tool but also enhances overall project transparency and accountability.
Letter Template For Construction Project Risk Mitigation Proposal Samples
Letter template of risk management framework for construction activities.
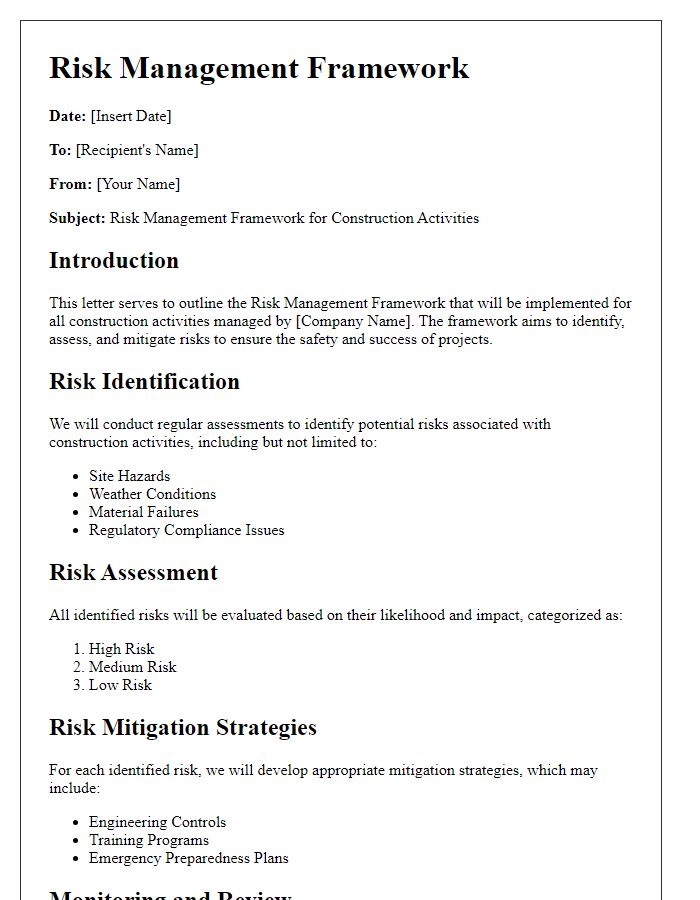
Letter template of construction project vulnerability assessment proposal.
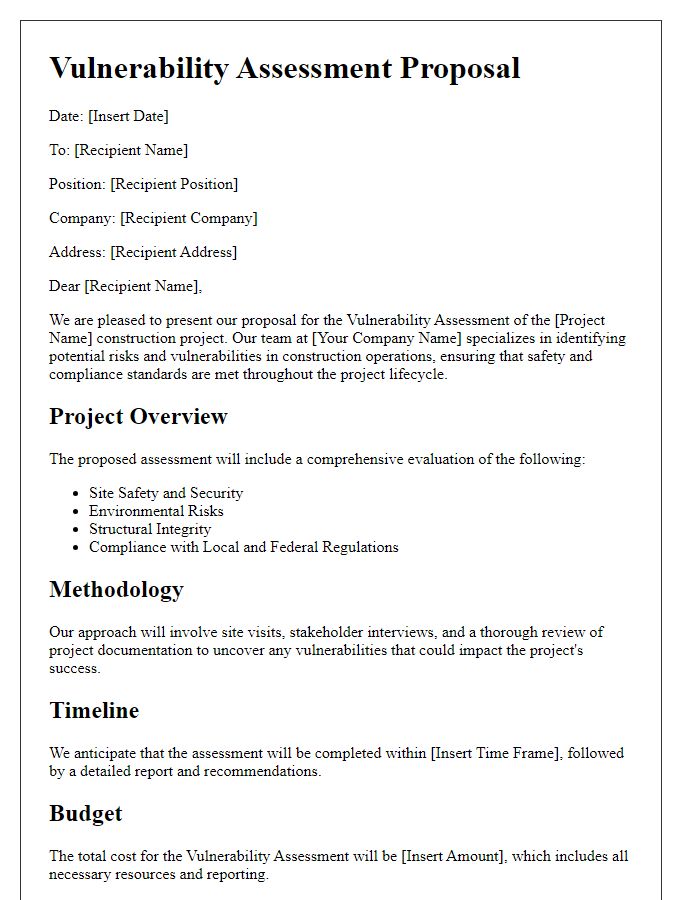
Comments