In today's fast-paced market, supply chain disruptions can happen to anyone, even the most reliable vendors. Whether due to unforeseen circumstances or demand surges, these hiccups can impact our operations significantly. It's essential to communicate transparently with all parties involved to navigate these challenges together. Letâs dive into how to effectively address vendor supply disruptions and keep your business running smoothly.
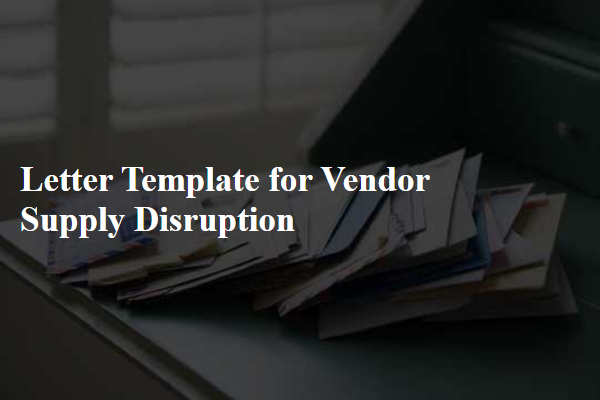
Clear Subject Line
Supply chain disruptions can significantly impact business operations, especially for companies relying on vendors for essential materials. For example, a shortage of semiconductor chips, critical for electronics manufacturing, can halt production lines. This situation was notably observed during the COVID-19 pandemic, causing numerous automotive companies to temporarily close facilities due to a lack of essential components. Additionally, natural disasters, such as hurricanes or floods, can disrupt logistics and transportation networks, delaying shipments and leading to inventory shortages. Businesses must proactively communicate with vendors about potential disruptions, reassess supplier relationships, and explore alternative sourcing options to ensure operational continuity.
Acknowledgment of Issue
Supply disruptions can severely impact manufacturing operations, especially in companies reliant on timely delivery of essential components, such as automotive parts, electronics, or consumer goods. Vendors, like those located in industrial hubs such as Shenzhen or Detroit, may face challenges that manifest as delays in shipment or incomplete orders. These disruptions can stem from various factors, including raw material shortages, transportation issues, or unforeseen events like natural disasters. Acknowledgment of such disruptions is crucial for maintaining communication and trust between suppliers and manufacturers. For instance, a vendor should promptly inform its client about potential delays, providing an estimated timeline and possible solutions to mitigate the impact. Clear documentation of affected orders, including order numbers and expected delivery changes, ensures transparency in the supply chain process.
Reason for Disruption
Supply chain disruptions can significantly impact the availability of goods and services across various industries, particularly in manufacturing and retail sectors. Events such as natural disasters, including hurricanes or earthquakes, can halt the production at key supplier facilities, affecting lead times. Additionally, geopolitical tensions, like trade wars or sanctions, may lead to delays in shipping routes or increased tariffs on imported goods. The ongoing global health crisis, exemplified by the COVID-19 pandemic, has revealed vulnerabilities in supply networks, resulting in shortages of raw materials and labor. Transportation issues, such as port congestion, can exacerbate delays, especially in regions like Southern California where shipping traffic has dramatically increased. Understanding these factors is essential for businesses to develop strategies that mitigate the impact of supply disruptions on operations and customer satisfaction.
Estimated Resolution Timeline
Supply chain disruptions can significantly impact product delivery schedules, particularly for vendors managing critical inventories. Events such as natural disasters, geopolitical tensions, or pandemics can lead to shortages in raw materials or components. For instance, the ongoing semiconductor shortage originating from various manufacturing plants in East Asia has caused delays for industries reliant on electronics, with expected resolution timelines extending upwards of six months. During such disruptions, vendors must maintain clear communication with stakeholders regarding anticipated delays and revised timelines, ensuring transparency and the ability to strategize alternative solutions. Proactive measures, like diversifying suppliers or enhancing inventory management practices, can help mitigate these risks in future procurement processes.
Contact Information for Further Queries
Supply chain disruptions often impact vendor relationships, especially when dealing with critical materials. Vendors must clearly communicate any significant delays due to unforeseen circumstances, such as natural disasters or global transportation issues. Effective communication includes comprehensive contact information, enabling clients to address inquiries promptly. A dedicated customer service representative should be identified, along with their direct phone number and email address. Additionally, establishing a timeline for resolution gives customers clear expectations regarding the expected delivery schedule. Providing updates on alternative supply options or backup plans can also enhance client confidence during the disruption.
Letter Template For Vendor Supply Disruption Samples
Letter template of escalation regarding persistent vendor supply disruption.
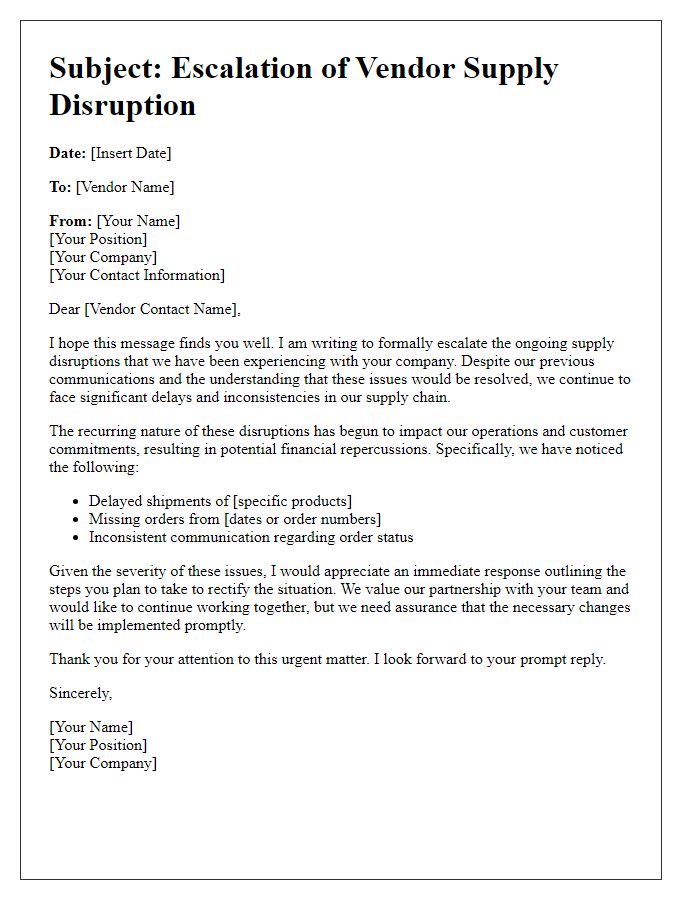
Letter template of negotiation for alternative solutions during vendor supply disruption.
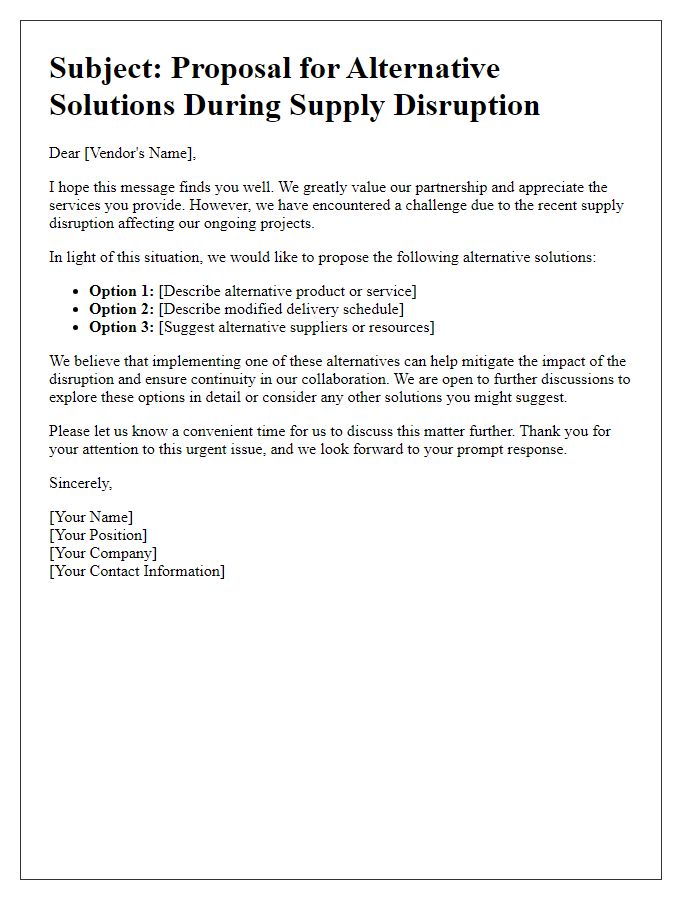
Letter template of confirmation of understanding vendor supply disruption.
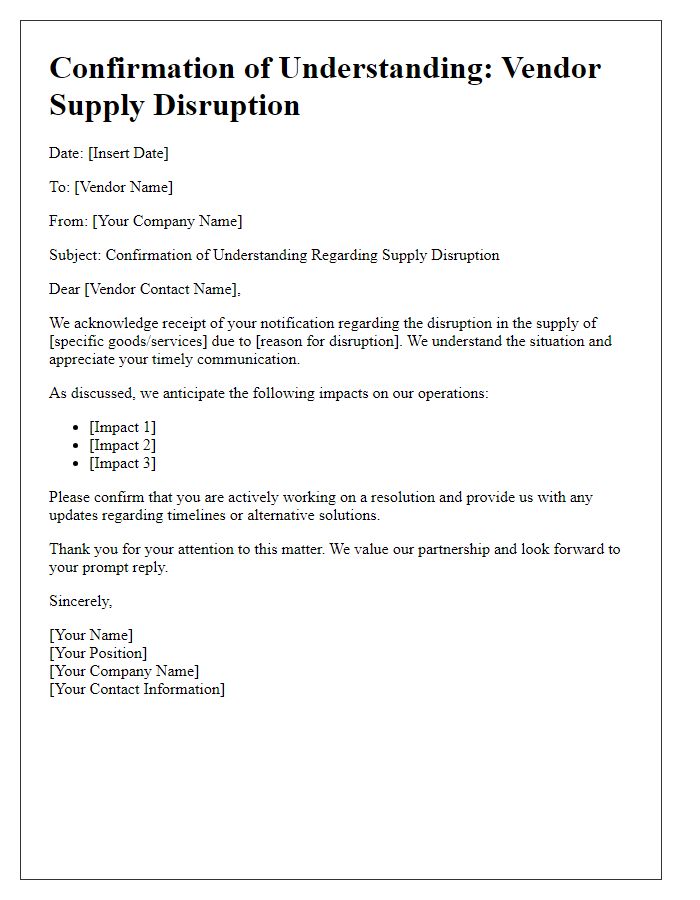
Letter template of follow-up on previous communication about vendor supply disruption.
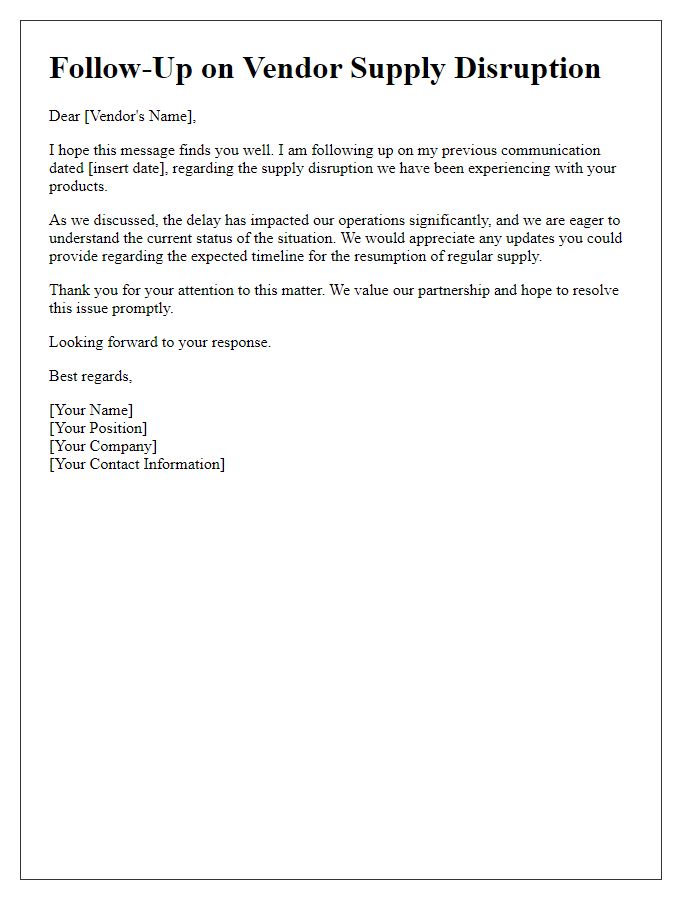
Comments