Navigating the ins and outs of a supply chain agreement can feel overwhelming, but it doesn't have to be! Whether youâre a seasoned professional or new to the logistics scene, understanding the nuances of these agreements is crucial for ensuring smooth operations. A well-crafted letter can pave the way for clear communication, setting the stage for mutually beneficial partnerships. Join me as we explore essential elements of a supply chain agreement letter that can help streamline your operations and foster collaborationâread on to uncover more!
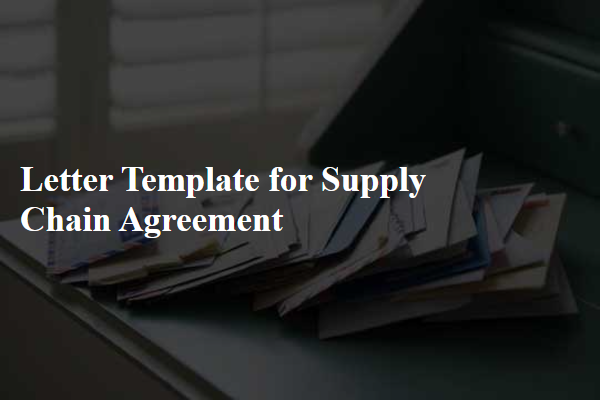
Parties Involved
In a supply chain agreement, the parties involved typically include suppliers, manufacturers, distributors, and retailers. Suppliers, such as Company A located in Chicago, Illinois, provide the raw materials necessary for production, while manufacturers like Company B, based in San Francisco, California, transform these materials into finished goods. Distributors, including Company C, situated in Dallas, Texas, are responsible for transporting these products to various retail locations. Retailers, such as Company D, with stores across New York City, sell the final products to consumers. Each party plays a critical role in ensuring a seamless flow of goods, optimizing inventory management, and enhancing customer satisfaction.
Scope of Agreement
The Supply Chain Agreement delineates the operational framework between the parties involved, ensuring a seamless flow of goods, services, and information. Critical components include procurement processes, inventory management protocols, and logistics strategies aimed at optimizing efficiency and minimizing costs across all transactions. The agreement covers essential metrics such as lead times, defined in business days from order placement to delivery completion, and quality assurance standards, specifying acceptable defects per million opportunities (DPMO). Furthermore, it incorporates compliance with relevant regulatory guidelines, including OSHA regulations related to workplace safety and environmental standards as mandated by the EPA. Stakeholders, identified as suppliers, manufacturers, and distributors, are bound to adhere to these terms to foster collaboration and enhance supply chain resilience. Thorough documentation, including invoices, shipping manifests, and quality certificates, will support accountability and traceability throughout the supply chain process.
Payment Terms
Payment terms in a supply chain agreement play a crucial role in defining the financial responsibilities and expectations between parties involved in the transaction. Commonly, the terms stipulate specific timelines for payments, often ranging from Net 30 to Net 60 days after the invoice date. Early payment discounts, such as 2% off if paid within 10 days, can incentivize timely payments. It's vital to note relevant currency specifications, often denoting US Dollars (USD) or Euro (EUR), to avoid conversion discrepancies. Additionally, penalties for late payments, typically a percentage of the outstanding amount per month, are outlined to encourage adherence to agreed-upon schedules. Clear delineation of payment methods, including electronic transfers or checks, underlines how transactions should be processed. Lastly, conditions for dispute resolution related to payment issues ensure both parties have a mutually agreeable mechanism for addressing conflicts.
Delivery Schedule
A well-defined delivery schedule is essential for effective supply chain management, ensuring timely arrival of goods at designated locations. Specific dates, such as quarterly deliveries or bi-weekly shipments, facilitate smooth operations and inventory control. For instance, adhering to a delivery window of 2-5 days post-order can enhance supplier efficiency and customer satisfaction. Critical aspects like lead times (time from order placement to delivery) should be clearly stated, along with potential penalties for delays, fostering accountability among all parties. Additionally, involving logistics partners, such as freight carriers or third-party logistics providers, can optimize transportation routes and reduce costs. Regular reviews of delivery performance metrics can identify trends, enabling continuous improvement in the supply chain process.
Dispute Resolution Mechanism
A supply chain agreement's Dispute Resolution Mechanism outlines the processes and procedures for addressing conflicts that arise between parties involved in the logistics and distribution of goods. This mechanism typically encompasses arbitration and mediation, providing a structured approach to conflict resolution outside of traditional court litigation. For instance, parties may agree to engage a neutral third-party arbitrator, such as the American Arbitration Association (AAA), to facilitate discussions and reach an equitable solution. Timelines for dispute notification procedures, often set within 30 days of the incident, ensure prompt attention to issues, while documenting meetings and resolutions aids in maintaining transparency and accountability. Additionally, incorporating clauses related to governing laws, such as the Uniform Commercial Code (UCC), clarifies jurisdictional matters, guiding the resolution process through predefined legal frameworks.
Comments