Are you looking to create a solid foundation for a successful partnership with a product manufacturing agreement? Itâs crucial to have a comprehensive and well-structured letter that outlines the terms, responsibilities, and expectations of both parties involved. This document not only protects your interests but also promotes a harmonious working relationship. Join us as we explore a detailed letter template that will guide you through the essential elements of a manufacturing agreement.
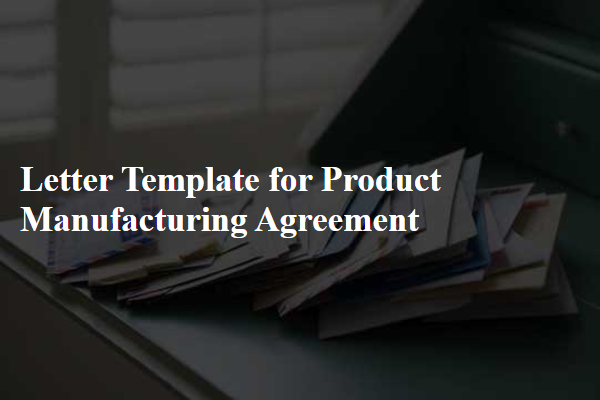
Parties Involved
A product manufacturing agreement typically involves two primary parties: the manufacturer and the client. The manufacturer, often a company specializing in production processes and industrial capabilities, engages in the creation of goods, often utilizing raw materials (such as plastics, metals, or textiles) sourced from various suppliers. The client, usually a brand owner or entrepreneur, requires the products to be designed and built according to specific standards, dimensions, or branding requirements. This agreement outlines critical aspects like pricing structures, order quantities, delivery timelines, intellectual property rights, quality control measures, and confidentiality obligations, ensuring a clear understanding of the roles and responsibilities of each involved party throughout the manufacturing process.
Scope of Work
The manufacturing agreement outlines the detailed scope of work for the production of electronic components at the manufacturer's facility located in Shenzhen, China. This project includes the assembly of printed circuit boards (PCBs) with a target production volume of 10,000 units per month, adhering to the IPC-A-610 standard for assembly quality. Each PCB must incorporate components sourced from approved suppliers, ensuring compliance with RoHS (Restriction of Hazardous Substances) regulations. Additionally, the quality assurance process involves rigorous testing, including functional testing and automated optical inspection (AOI), with a defect rate not exceeding 0.5%. The timeline for the initial production run is set for January 2024, with a comprehensive delivery schedule that aligns with the client's market launch on March 15, 2024. Detailed documentation of the manufacturing process and traceability records will be maintained throughout the production cycle.
Quality Assurance
A quality assurance program in product manufacturing, particularly in factories like those in Shenzhen, China, aims to ensure that products meet specified quality standards before reaching the market. This involves rigorous inspections at multiple stages of production, including initial raw material checks, in-process inspections, and final product assessments. Key performance indicators, such as defect rates (ideally below 2%) and compliance with regulatory standards (such as ISO 9001 certification), are monitored to evaluate quality. Testing methods, including material tensile strength tests and functionality checks, are employed to verify that the products, like electronic devices or clothing, meet customer expectations. Comprehensive documentation, including quality control reports, audit trails, and corrective action plans, provides accountability and traceability throughout the supply chain.
Delivery and Timelines
Delivery timelines in product manufacturing agreements dictate the specific dates and timeframes for the delivery of goods, which is crucial for operational efficiency. For instance, a contract might stipulate that the delivery of electronic components, such as circuit boards from a manufacturing facility in Shenzhen, China, should occur within 30 days after order confirmation. Additionally, penalties may be outlined for delays exceeding a defined grace period, ensuring accountability and encouraging timely distribution. Clear definitions regarding shipping methods--air freight versus sea freight--along with responsibilities for customs clearance and logistics partners, such as DHL or FedEx, are essential for minimizing risks associated with the supply chain. Precise lead times assist businesses in inventory management, allowing for seamless integration into production schedules and maintaining optimal stock levels.
Confidentiality and Intellectual Property
A comprehensive product manufacturing agreement must include elements addressing confidentiality and intellectual property. Confidentiality ensures that sensitive information, such as proprietary manufacturing processes, specifications, or client lists, remains protected from unauthorized disclosure. Both parties typically agree on strict measures to safeguard this information during the term of the agreement and for a defined period afterward, possibly ranging from two to five years. Intellectual property clauses detail ownership rights, stating that any innovations or designs created during the manufacturing process belong to the client, safeguarding their investment in unique product development. Furthermore, both parties may outline procedures for handling any intellectual property disputes that could arise, emphasizing the need for resolution through mediation or arbitration to avoid lengthy litigation.
Comments