Navigating the complexities of vendor product lifecycle assessment can feel daunting, but it doesnât have to be. Understanding each phase of your product's journeyâfrom conception to retirementâcan significantly enhance your strategic decision-making. This letter template serves as a valuable resource to streamline communication and foster collaboration with your vendors. Ready to dive deeper into optimizing your product lifecycle? Read on to explore how you can elevate your approach!
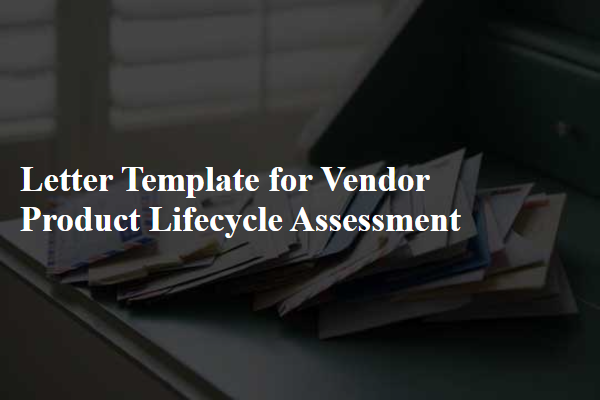
Product Description and Specifications
The product lifecycle assessment (LCA) of biodegradable packaging, including materials like PLA (Polylactic Acid) derived from renewable resources, focuses on key specifications such as thickness, tensile strength, and decomposition rate. Standard thickness options of 30 microns to 100 microns provide various strength levels for different applications, catering to both lightweight and heavy-duty packaging needs. Tensile strength typically ranges from 40 to 80 MPa, ensuring durability during transport and storage. The decomposition rate under industrial composting conditions, approximately 45 to 90 days, significantly reduces landfill waste compared to conventional plastics, which take centuries to decompose. Specifically, this product aligns with sustainability goals, meeting regulatory requirements outlined by organizations such as the Environmental Protection Agency (EPA) in the United States. Additionally, certifications from bodies like ASTM International validate its compostability, enhancing its market appeal.
Environmental Impact and Sustainability Practices
Environmental impact assessments are crucial in evaluating the sustainability practices of various products throughout their lifecycle, from design to disposal. Key stages include raw material extraction, which often utilizes non-renewable resources like petroleum or metals, affecting ecosystems (deforestation rates, mining impacts in regions like the Amazon). Production processes, particularly for electronics, can result in significant greenhouse gas emissions, with estimates suggesting around 15-20% of global emissions stem from manufacturing industries. Distribution involves transportation methods, where road and air freight can lead to carbon footprints significantly higher than rail or sea options, with air freight producing approximately 500 grams of CO2 per ton-mile. Usage phases, especially with energy-intensive products, can vary in efficiency, impacting users and contributing to energy consumption statistics (average household electricity usage of 877 kWh/month in the US). Finally, end-of-life management practices, such as recycling or landfill disposal, directly influence waste generation and pollution, with only about 12% of plastics recycled globally. Evaluating these factors is essential for understanding the overall sustainability of vendor products.
Regulatory Compliance and Safety Standards
The vendor product lifecycle assessment focuses on Regulatory Compliance and Safety Standards, crucial for ensuring product integrity and consumer protection. Companies must adhere to guidelines set by governing bodies, such as the Food and Drug Administration (FDA) in the United States or the European Union's REACH regulation, impacting various sectors. Compliance involves evaluating materials, production processes, and end-of-life disposal methods to mitigate environmental risks. Safety Standards, including international norms like ISO 9001 for quality management systems and ISO 14001 for environmental management, establish benchmarks for product safety and performance. Regular audits and documentation are essential to maintain transparency and accountability throughout the product lifecycle, ensuring that all products meet legal and ethical standards before reaching the market.
End-of-Life Management and Recycling Options
Product lifecycle assessment is critical for effective end-of-life management and recycling options for electronic devices like smartphones and laptops. Electronic waste (e-waste) generated in 2021 exceeded 57 million metric tons globally, posing significant environmental challenges. Recycling initiatives can recover valuable materials such as gold, silver, and rare earth elements, reducing the need for mining and its ecological impact. Organizations like the Basel Convention aim to mitigate hazardous waste exports, promoting responsible e-waste handling. Local recycling facilities, incorporated in community programs, can ensure compliance with environmental regulations while offering consumers secure disposal methods. Implementing comprehensive recycling strategies can enhance brand reputation and contribute to sustainability goals.
Cost-Benefit Analysis and Total Cost of Ownership
Conducting a vendor product lifecycle assessment is essential for understanding the financial implications and overall value of a product. The cost-benefit analysis (CBA) involves quantifying benefits such as increased efficiency or enhanced performance (e.g., 20% productivity improvement) against costs including initial purchase price (e.g., $50,000 for enterprise software) and ongoing expenses (annual maintenance fees reaching $10,000). The total cost of ownership (TCO) encapsulates all direct and indirect costs (e.g., training, downtime, disposal) associated with the product throughout its lifecycle, often spanning five to seven years. An in-depth understanding of these financial metrics facilitates informed decision-making and ensures alignment with organizational goals. Specific metrics, benchmarks, and historical data can provide additional insights into potential return on investment, risk factors, and long-term sustainability of the product within the organization's operational framework.
Comments