In today's competitive market, ensuring product quality is more important than ever, and having the right certifications can make all the difference. Whether you're a supplier or a business looking to source high-quality goods, understanding the nuances of product quality certification is crucial. This guide will walk you through the essential components and best practices for obtaining and maintaining these certifications. So, let's dive in and explore how you can elevate your product standardsâread on to learn more!
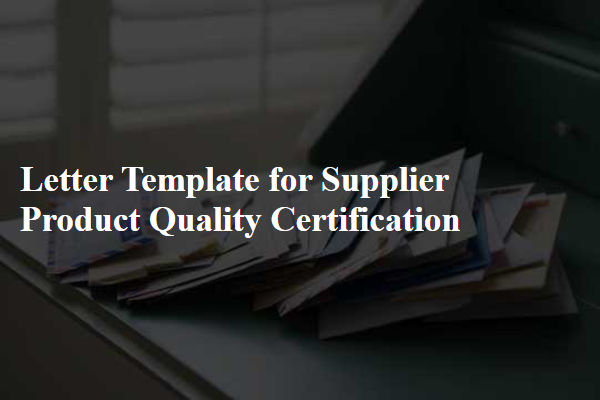
Supplier Information
High-quality supplier information is essential for obtaining product quality certification, particularly for manufacturing processes. Certification bodies, such as ISO (International Organization for Standardization), often require documents that detail supplier capabilities, materials used, and production methods. For instance, suppliers should provide standardized data sheets highlighting material specifications, regulatory compliance, and manufacturing processes employed. Key aspects include the supplier's location (such as factories in China or Germany), certifications held (like ISO 9001 or ISO 14001), and past performance metrics (such as product defect rates below 1% over the last three years). This comprehensive overview aids manufacturers in ensuring product quality and compliance with industry standards.
Product Details
Product quality certification is essential for maintaining standards across various industries. For instance, electronic components such as semiconductors require stringent quality evaluations before certification. In 2023, leading manufacturers like Intel and Samsung implemented rigorous testing protocols that include thermal cycling tests and electrical performance assessments. These processes ensure that each batch of products, including microprocessors and memory chips, meets international quality standards outlined by organizations such as ISO (International Organization for Standardization). Certifications typically verify parameters like dimensional tolerance, material integrity, and performance reliability, providing assurance to customers about product durability and efficacy.
Quality Standards Compliance
The certification process for supplier product quality involves stringent adherence to established quality standards, such as ISO 9001:2015. This international standard focuses on effective quality management systems (QMS) to ensure consistent product quality and service delivery. Key elements include documented procedures, regular audits, and continuous improvement practices. Compliance verification requires detailed assessment of production processes at locations such as manufacturing plants and warehouses, with emphasis on critical control points to minimize defects. Certification bodies, like SGS and TUV, play essential roles in evaluating compliance, offering objective third-party audits, and issuing official certifications to suppliers demonstrating reliable quality assurance practices. Regular surveillance audits help maintain compliance and assess any deviations from quality standards.
Inspection and Testing Procedures
Suppliers must adhere to stringent inspection and testing procedures to ensure product quality across various stages of manufacturing. Quality Assurance (QA) protocols involve a thorough assessment of raw materials, including percentages of impurities allowed and compliance with industry standards such as ISO 9001. During the production phase, processes like in-line inspections, where operators check for defects every hour, are executed. Final product evaluations often consist of mechanical tests, such as tensile strength measurements, which determine durability and safety, following specifications set by organizations like ASTM International. This systematic approach ensures that the products meet customer expectations and regulatory requirements, fostering trust and reliability in supplier relationships.
Certification Validity and Expiry
Supplier product quality certification plays a crucial role in ensuring adherence to industry standards, often regulated by governing bodies like ISO (International Organization for Standardization). Certification validity typically spans three years, with specific companies often requiring renewal processes that include additional audits or compliance checks. After this period, the certification expires, necessitating re-evaluation to maintain supplier eligibility for contracts. Product quality metrics, particularly defect rates and compliance with safety regulations, also significantly affect the renewal process. The implications of expired certification can lead to reduced market confidence and potential disruptions in supply chain operations for businesses reliant on certified products.
Letter Template For Supplier Product Quality Certification Samples
Letter template of supplier certification for quality standards adherence
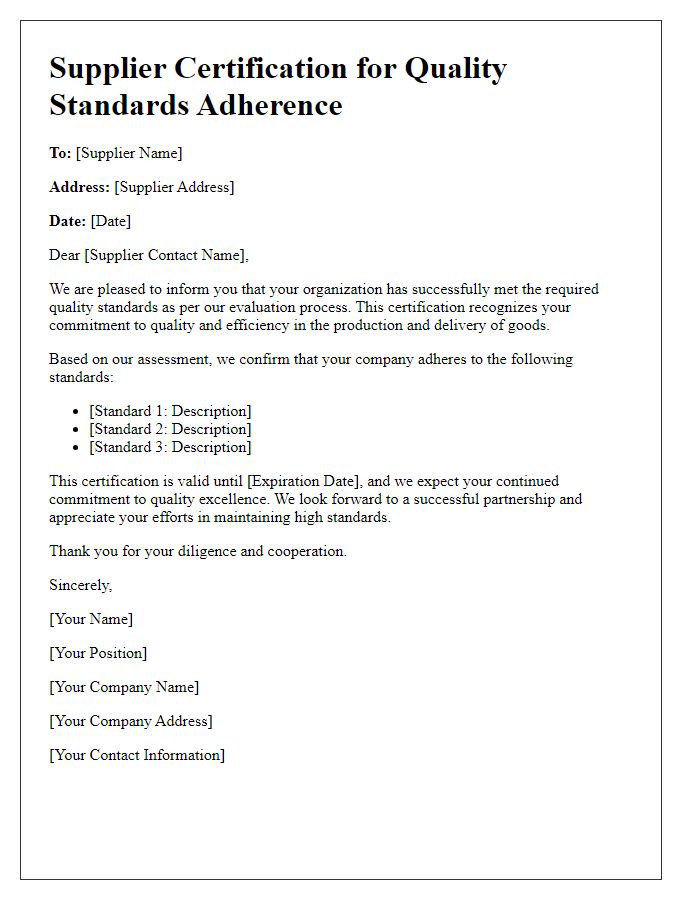
Comments