Are you tired of rising packaging costs eating into your profits? You're not aloneâmany businesses are seeking effective strategies to tackle this pressing issue. In this article, we'll explore some innovative solutions to help you reduce packaging expenses while maintaining product quality and customer satisfaction. Stick around to discover actionable tips that can transform your supplier relationships and drive cost efficiency!
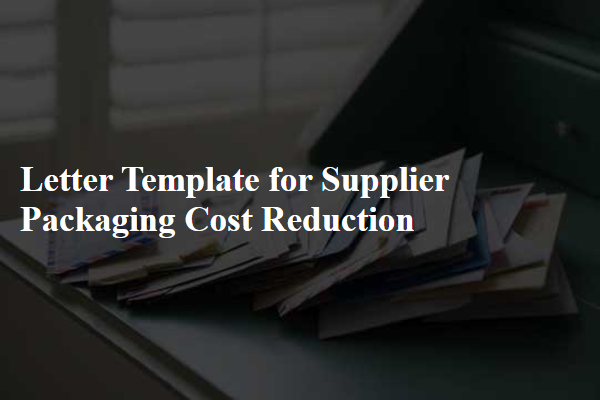
Clear Communication of Objectives
Effective communication of objectives is essential in negotiating packaging cost reductions with suppliers. Companies can streamline expenses while maintaining quality through strategic discussions. Transparency about target cost percentages, expected savings ranges (typically aiming for reductions of 10-20%), and specific packaging requirements such as environmentally friendly materials can foster collaborative relationships. Establishing key performance indicators (KPIs) related to packaging efficiency helps suppliers understand expectations. Discussing case studies from similar industries or successful previous collaborations illustrates potential for mutual benefits. Additionally, scheduling regular follow-ups ensures consistent alignment on objectives, creating an ongoing dialogue that allows for adjustments based on market conditions or material availability.
Detailed Cost Analysis
A detailed cost analysis of packaging expenses reveals significant opportunities for reduction. The current expenditure on materials, such as cardboard boxes and plastic wrapping, averages approximately $2.50 per unit for shipment in the Midwest region, with specific manufacturers like XYZ Corp contributing to higher costs due to their sourcing practices. Labor costs associated with packaging, currently estimated at $1.00 per unit, suggest inefficiencies during the packing processes at facilities in Ohio and Illinois. Additionally, shipping costs, averaging $0.75 per unit for transportation over distances exceeding 300 miles, can be optimized by exploring local suppliers or consolidating shipments more effectively. Implementing sustainable materials might offer long-term savings and elevate brand reputation, while also complying with regulatory guidelines from organizations like the Environmental Protection Agency (EPA).
Collaborative Approach
Suppliers in the packaging industry often face rising costs due to fluctuating raw material prices, freight charges, and labor expenses. Strategic discussions focused on collaborative approaches can lead to innovative solutions aimed at reducing overall packaging costs. Techniques such as bulk purchasing agreements or shared logistics arrangements can significantly decrease unit costs. Implementing alternative materials such as biodegradable options or recycled materials may also yield cost savings while promoting sustainability. Engaging in regular feedback sessions on design efficiency and exploring automation in packaging processes could enhance productivity and reduce waste, resulting in further financial benefits.
Sustainable Alternatives
Sustainable packaging alternatives can significantly reduce costs for suppliers seeking environmentally friendly solutions. For instance, using biodegradable materials, such as corn starch-based bioplastics or recycled paper, presents a viable option that can decrease expenses associated with disposal in landfills. Suppliers can also explore lightweight packaging designs that lower shipping costs; for example, using compressible materials that require less transportation space. The implementation of reusable packaging systems can further enhance cost savings by reducing the frequency of purchasing new materials, allowing companies like IKEA to minimize waste and improve their sustainability score. Adopting these sustainable alternatives not only lowers costs but enhances brand reputation, appealing to environmentally-conscious consumers.
Timeline for Implementation
Implementing a packaging cost reduction strategy involves several critical phases and timelines. Initial assessment (1-2 weeks) focuses on analyzing current packaging materials and processes for inefficiencies. Next, a supplier meeting (3 weeks) will allow for discussions about alternative materials or methods that maintain product integrity but reduce costs. Design prototypes (1 month) will be created, allowing for testing and feedback on new packaging solutions. Pilot testing (2-4 weeks) will assess durability and cost-effectiveness before full-scale implementation. Once successful, a phased rollout (immediate after testing) across all products will begin, followed by monitoring and adjustments (ongoing) as needed to ensure long-term savings and sustainability in packaging operations.
Letter Template For Supplier Packaging Cost Reduction Samples
Letter template of negotiation for lower packaging expenses from supplier.
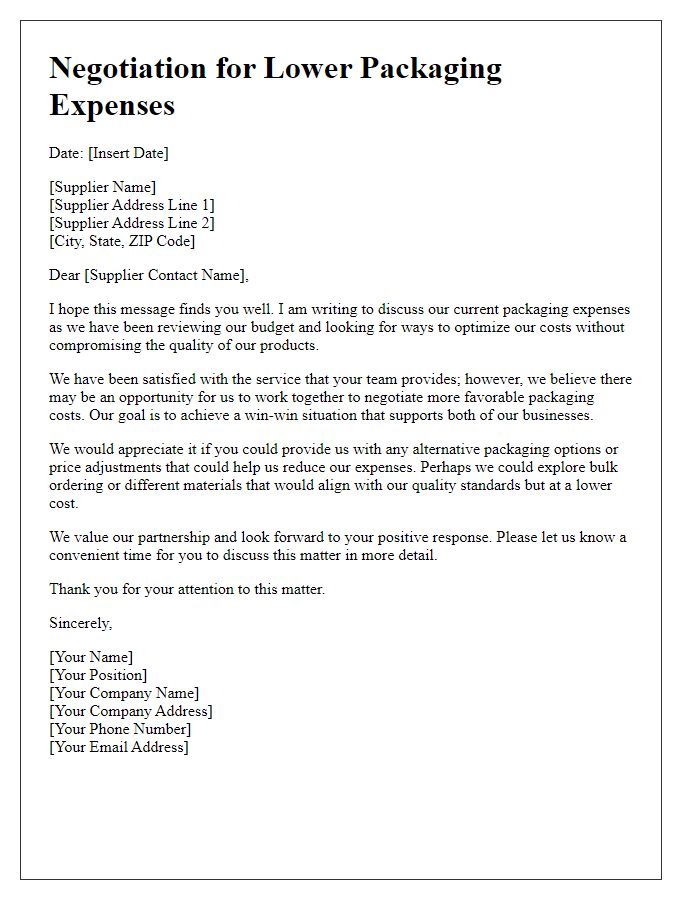
Letter template of inquiry about supplier packaging cost reduction options.
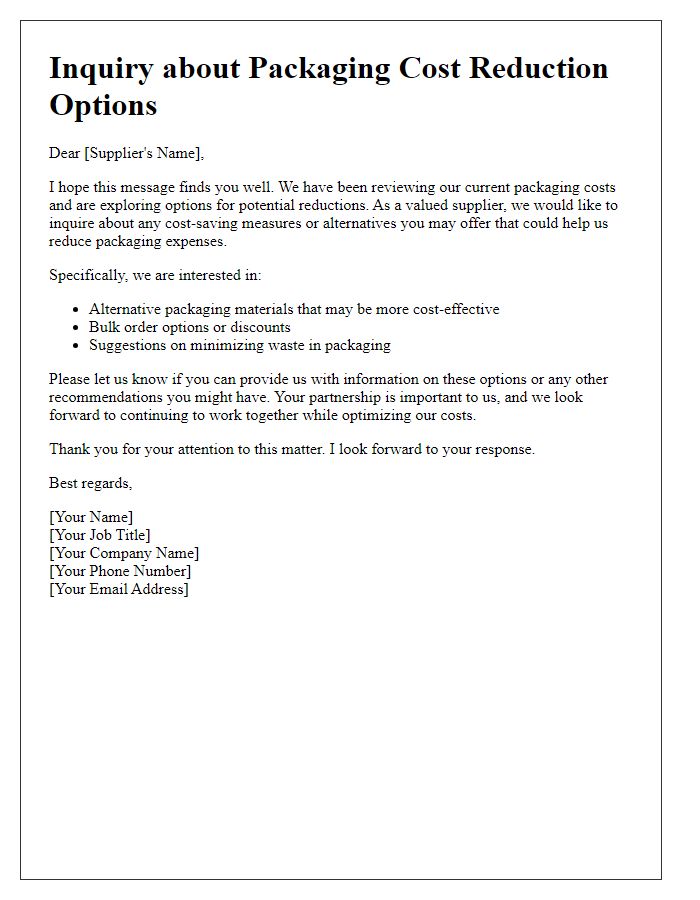
Letter template of agreement for revised packaging pricing with supplier.
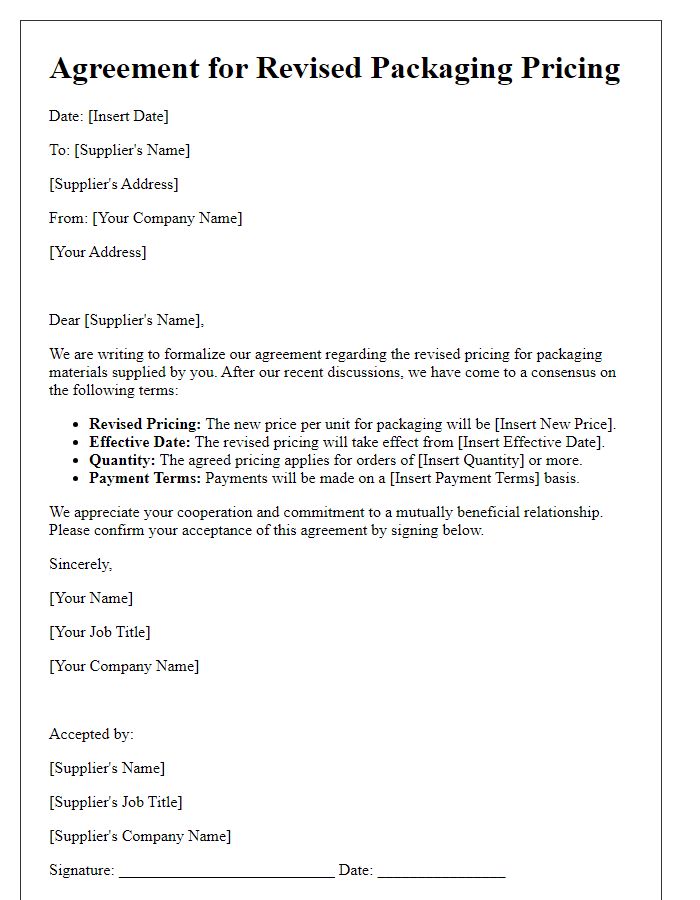
Letter template of follow-up on packaging cost savings discussions with supplier.
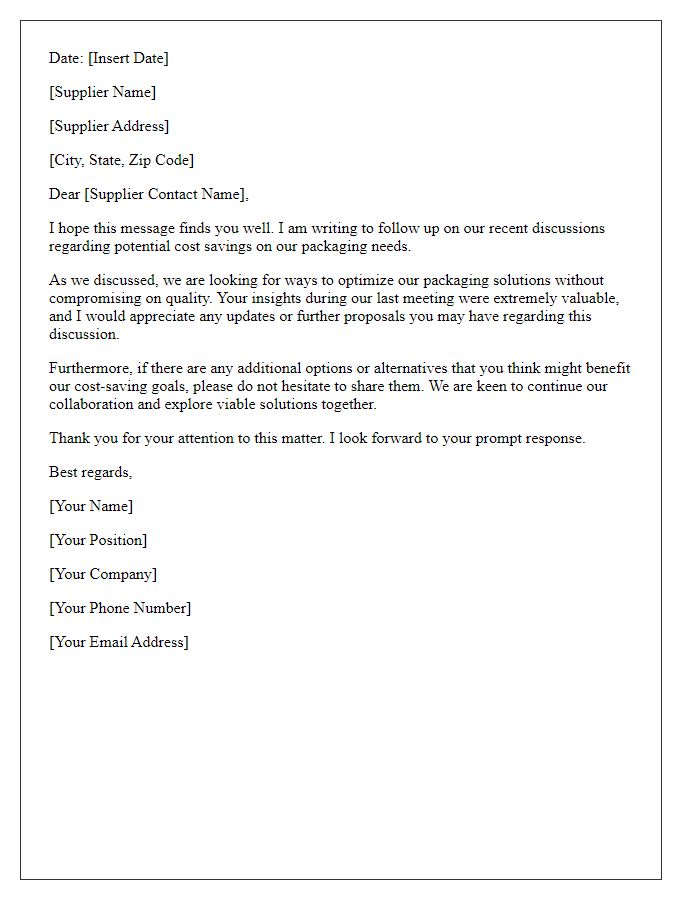
Letter template of strategy for collaborative packaging cost reduction with supplier.
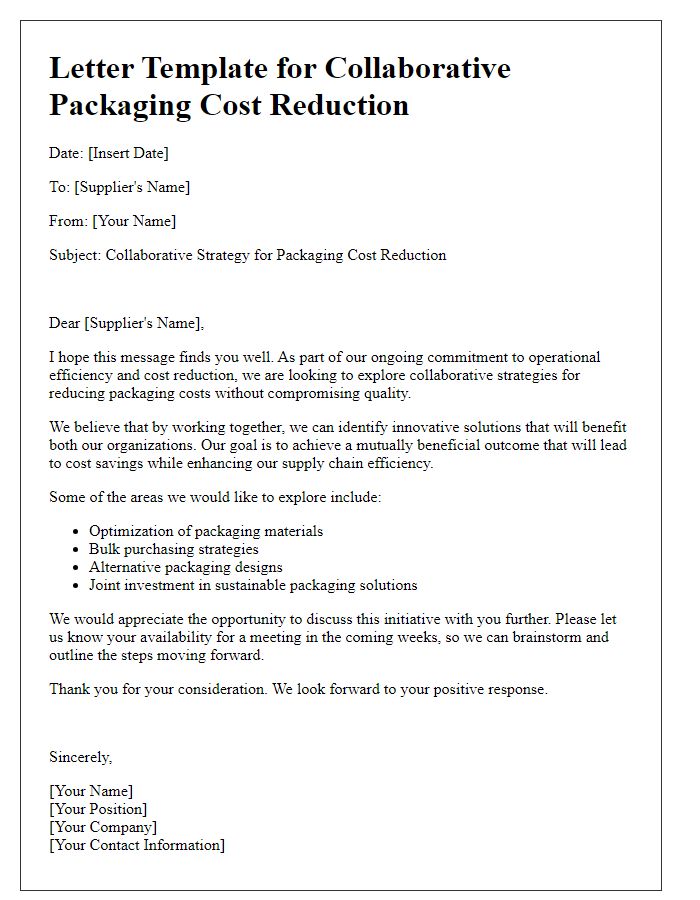
Letter template of notification for seeking packaging cost adjustments from supplier.
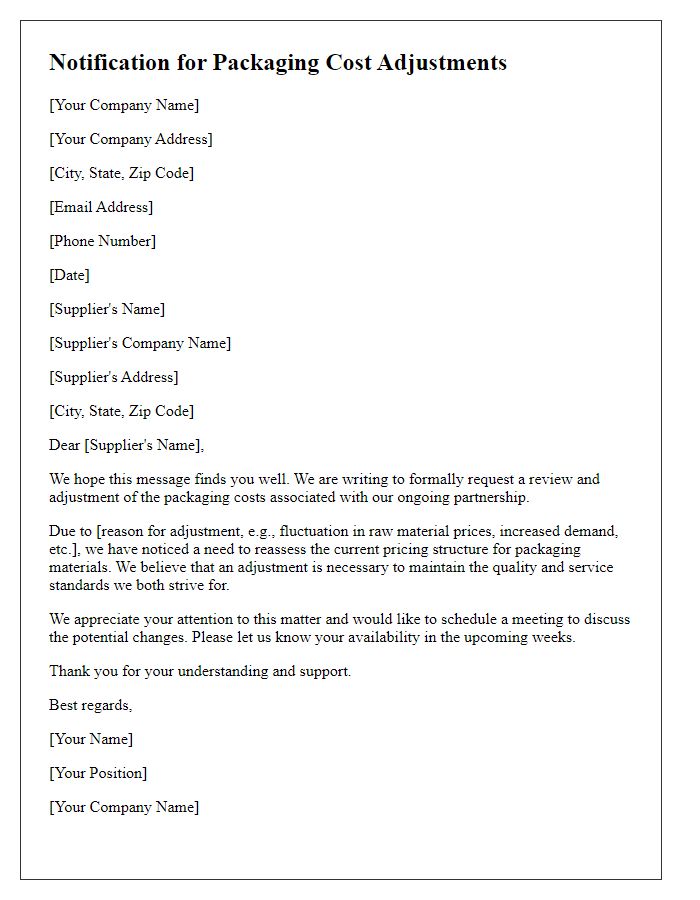
Comments