Are you curious about how digital twin technology is reshaping industries? This innovative approach creates a virtual replica of physical assets, allowing companies to analyze performance, predict outcomes, and enhance decision-making processes. By leveraging real-time data, organizations can optimize operations and drive efficiency like never before. If you want to delve deeper into this fascinating topic and explore its implications for various sectors, keep reading!
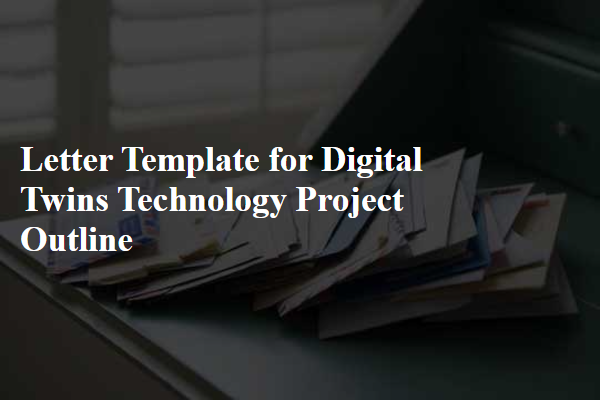
Project Objectives and Goals
Digital twins technology creates virtual replicas of physical entities, allowing real-time data integration and analysis. Key objectives include enhancing operational efficiency, minimizing downtime, and improving predictive maintenance strategies, utilizing sensors and IoT data streams. Specific goals involve developing a comprehensive data model that includes parameters from the machinery (such as motors and turbines), environmental conditions (temperature, humidity), and operational metrics (throughput, cycle time). Implementation aims to reduce operational costs by at least 15% over the first year, leveraging analytics platforms and machine learning algorithms that predict system failures. Geographic scope encompasses industrial sectors, emphasizing facilities in advanced manufacturing hubs, such as Germany and Japan, known for their innovative technologies.
Key Stakeholders and Roles
The implementation of digital twins technology, defined as virtual replicas of physical systems, necessitates the collaboration of various key stakeholders. Engineers (responsible for the technical design and integration of digital twin systems), data analysts (tasked with interpreting vast datasets generated from physical assets), and IT specialists (focused on maintaining the software infrastructure required for real-time data processing) play critical roles. Project managers oversee timelines and resource allocation, ensuring alignment with strategic objectives. Additionally, end-users (such as operators and maintenance teams) provide essential feedback on usability, greatly influencing system enhancements. Lastly, executive sponsors (typically high-ranking officials within organizations like Siemens or GE) secure funding and resources, facilitating the project's success. Each stakeholder's contribution is vital for the development and optimization of digital twin solutions, impacting industries such as manufacturing, aerospace, and healthcare.
Scope and Deliverables
Digital twins technology encompasses the creation of virtual replicas of physical assets, processes, or systems that enable real-time monitoring and analysis. This project aims to implement digital twin models in industrial settings, particularly focusing on manufacturing equipment, such as CNC machines and assembly robots, to enhance operational efficiency. Key deliverables include the development of a scalable digital twin framework, integration of IoT sensors for data collection, and the establishment of predictive maintenance protocols utilizing machine learning algorithms. Additionally, training workshops for end-users, covering tools like Microsoft Azure Digital Twins, will be conducted to ensure effective application and utilization of created models in real-world scenarios. By utilizing this cutting-edge technology, organizations can achieve significant cost savings and reduced downtime, leading to improved productivity levels across various sectors.
Milestones and Timeline
Digital twins technology offers innovative solutions for various industries, including manufacturing, healthcare, and urban planning. This project aims to develop a comprehensive digital twin model utilizing real-time data integration and simulation capabilities. Key milestones include the initial phase of data collection, which involves gathering operational metrics from physical assets within six months. Following this, a prototype model will be developed within the next four months, focusing on user interaction and data visualization. The next milestone entails extensive testing and validation over two months to ensure accuracy and reliability of the digital twin. Finally, the project aims to launch the full-scale digital twin deployment by the end of the year, enabling stakeholders to analyze and optimize performance through actionable insights derived from the digital model.
Budget and Resource Allocation
Digital twins technology enables virtual replicas of physical assets, enhancing monitoring and predictive maintenance capabilities in industries like manufacturing and healthcare. A comprehensive budget allocation is critical for the successful implementation of this technology, encompassing costs related to software licenses for platforms like Ansys and Siemens, hardware investments for IoT sensors in smart factories, and skilled workforce expenses for data scientists and engineers proficient in machine learning algorithms. Resource allocation must also account for cloud storage services, such as Amazon Web Services, for data hosting and processing. Furthermore, training sessions for staff to adapt to new systems and continuous maintenance of digital twins will require dedicated financial resources, ensuring optimum operational efficiency and longevity of the digital twin systems.
Letter Template For Digital Twins Technology Project Outline Samples
Letter template of project overview for digital twins technology implementation.
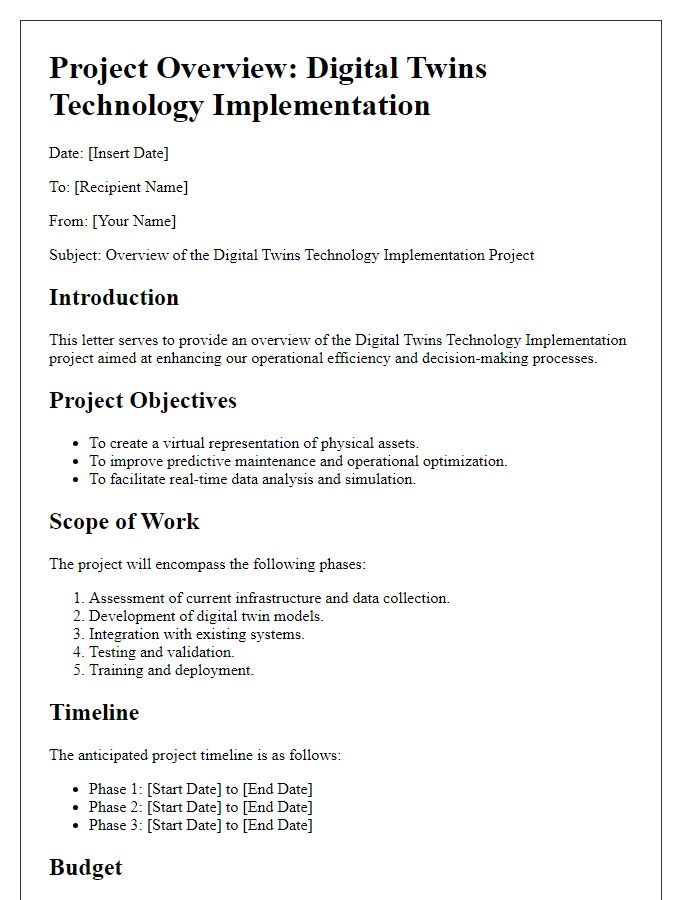
Letter template of funding request for digital twin technology initiative.
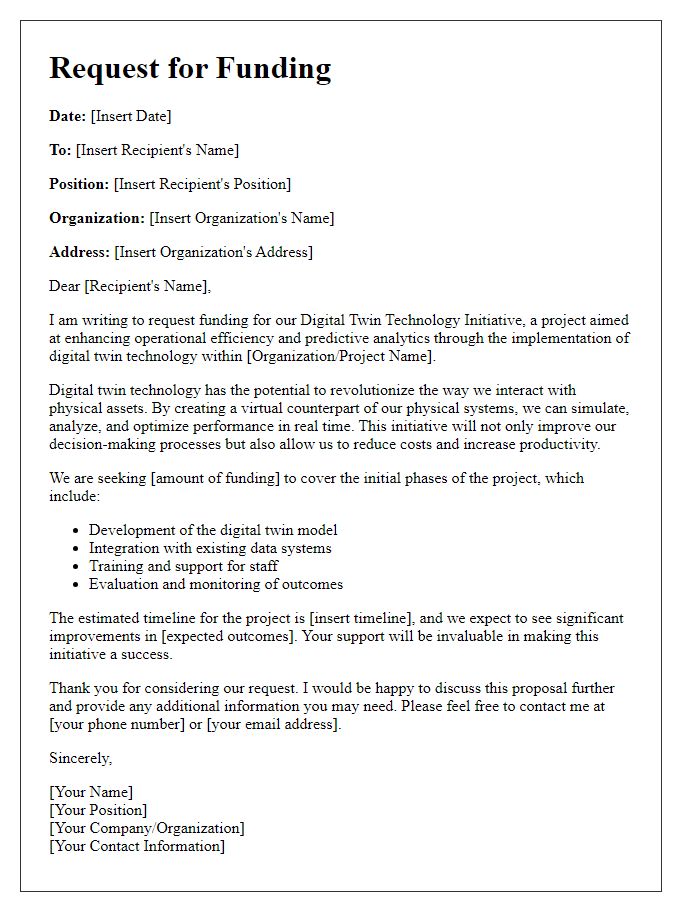
Comments