Are you looking to enhance your operational efficiency but donât know where to start? Feedback plays a crucial role in identifying areas for improvement, and crafting the right letter can set the tone for productive discussions. By communicating effectively, you not only share your insights but also invite collaboration from your team. Keep reading to discover a template that can help you deliver impactful feedback and drive meaningful change!
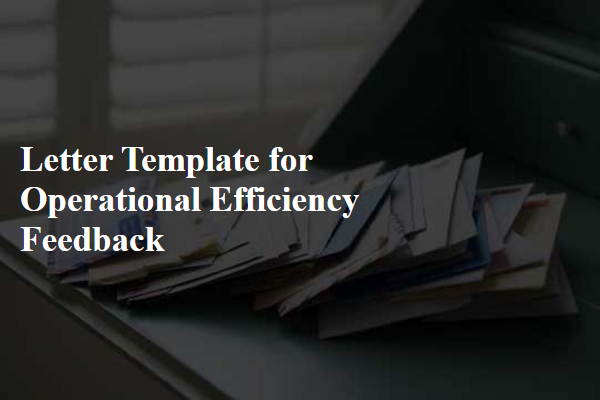
Clear Introduction
Operational efficiency feedback is essential for improving workflow and productivity in organizations such as manufacturing, which often require streamlined processes. Clear communication channels must be established to identify bottlenecks, such as excessive downtime during equipment maintenance or delays in supply chain logistics. Evaluating performance metrics, like production output (measured in units per hour) and employee engagement levels, provides valuable insights into areas needing improvement. Regular feedback loops can facilitate adjustments, ensuring alignment with strategic goals while fostering an adaptive organizational culture. Implementing technology solutions, such as automated tracking systems, can enhance real-time monitoring, contributing to a more agile operational framework.
Specific Feedback
Operational efficiency challenges significantly impact productivity in fast-paced environments like manufacturing and logistics. Inefficient workflows can lead to increased lead times, reduced output rates, and elevated costs. For instance, bottlenecks in assembly lines may result in prolonged downtime, ultimately affecting overall throughput (units produced per hour). Implementing lean methodologies can streamline processes, minimize waste, and enhance resource allocation. Regular training (quarterly sessions) for staff on best practices and new technologies will ensure all team members are aligned and equipped. Monitoring key performance indicators (KPIs), such as cycle time and inventory turnover, will provide insights into performance gaps and help identify opportunities for improvement. Addressing these issues proactively can create a more agile operational backbone, driving enhanced productivity and cost-efficiency.
Positive Reinforcement
Operational efficiency within organizations significantly benefits from positive reinforcement strategies. Regular feedback cycles enhance team morale, fostering an environment of appreciation and motivation. For instance, recognition programs highlighting employee accomplishments can boost productivity significantly, with studies suggesting an increase of up to 20% in work output. Places like Google and Zappos exemplify this approach by implementing practices that celebrate individual and team successes. Encouraging peer-to-peer recognition is also vital, as it cultivates a supportive workplace culture where employees feel valued and engaged. This positive feedback loop not only supports immediate operational goals but also contributes to long-term employee retention and satisfaction.
Areas for Improvement
Identifying areas for improvement in operational efficiency can significantly enhance productivity in organizational processes, particularly within corporate structures like manufacturing plants. Factors such as workflow management, where bottlenecks occur, can slow down production lines and increase lead times, impacting overall output. Employee training programs, tailored to address skill gaps, can empower staff and enhance their effectiveness in tasks like inventory management or quality control. Implementing technology solutions, such as automated tracking systems or project management software, can streamline operations and reduce human error. Regular performance assessments, utilizing metrics like cycle time and downtime, can provide valuable insights, guiding necessary adjustments for sustained operational excellence.
Constructive Suggestions
Operational efficiency is crucial for organizations striving to enhance productivity and reduce costs. Identifying bottlenecks in processes, such as the inventory management system at a distribution center, can lead to significant improvements. Implementing technology solutions like automated tracking systems can streamline order fulfillment, reducing processing time by up to 30%. Furthermore, regular team meetings (held bi-weekly) focused on feedback can foster a culture of continuous improvement. Training programs for staff on best practices can also improve knowledge retention and task execution, ultimately enhancing overall productivity and operational success.
Comments