Are you looking to enhance your vendor relationships and ensure top-notch quality assurance? Crafting the perfect feedback letter can make all the difference in holding vendors accountable and fostering collaboration. In this article, weâll explore a simple yet effective letter template that you can customize to suit your specific needs. So, grab a cup of coffee, sit back, and letâs dive into the art of delivering constructive feedback that gets results!
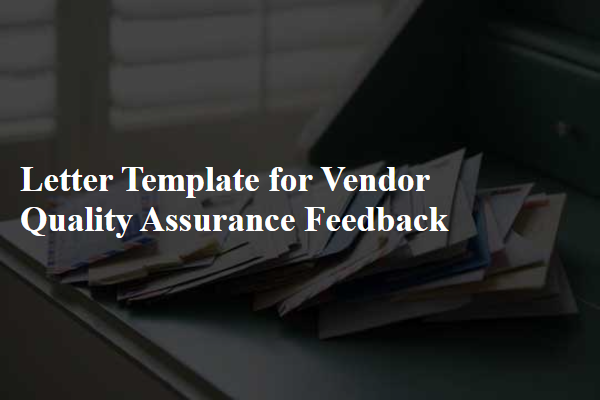
Clear subject line and introduction.
Vendor quality assurance feedback emphasizes the importance of product standards and compliance expectations. Quality assurance (QA) processes are crucial in maintaining high standards across various industries, including manufacturing and technology. Regular audits and assessments ensure that vendors adhere to specific benchmarks and guidelines. Notable QA metrics often include defect rates, compliance statistics, and customer feedback evaluations. Clear communication with vendors regarding quality expectations fosters stronger relationships and improves overall product reliability. Continual improvement practices, such as root cause analysis and corrective action plans, empower vendors to enhance their operational processes effectively.
Specific feedback on product quality.
Vendor quality assurance feedback can provide crucial insights into product quality standards. In a recent assessment of the ABC Widget model 3000, discrepancies in material thickness (measured at 1.8mm instead of the required 2.0mm) were noted, raising concerns about durability. Surface finish exhibited roughness values of over 40 microinches, which is inconsistent with our specification of no more than 20 microinches. The assembly process showed a 5% defect rate in fastening strength tests, surpassing the acceptable threshold of 2%. Moreover, in the heat resistance test conducted at temperatures exceeding 80 degrees Celsius, shifting in structural integrity was observed, suggesting a need for improved thermal stability. Addressing these issues will be pivotal for ensuring customer satisfaction and compliance with our quality standards.
Constructive suggestions for improvement.
Vendor quality assurance processes often benefit from constructive feedback aimed at enhancing product reliability and customer satisfaction. Implementing a systematic approach to quality checks can significantly reduce defect rates, currently observed at 5% during the last quarter's batch inspections. Offering regular training sessions for quality assurance personnel may address knowledge gaps and boost overall performance. Establishing a clear communication channel between production staff and quality controllers can facilitate immediate reporting of issues, reducing the average resolution time, which has fluctuated around 48 hours in previous incidents. Additionally, integrating advanced analytics tools could provide data-driven insights, enabling the identification of recurring quality issues and informing proactive measures to improve product consistency. Regular audits, scheduled quarterly, can ensure adherence to updated quality standards and drive continuous improvement initiatives.
Positive reinforcement and appreciation.
Vendor quality assurance plays a crucial role in maintaining product standards and enhancing the overall customer experience. Recent assessments from suppliers, such as those providing automotive components, have consistently highlighted exceptional performance in meeting quality benchmarks. The percentage of defect-free products stood at an impressive 98%, demonstrating a commitment to excellence in manufacturing and processes. Positive feedback from teams in various locations, including Detroit (known as a hub for automotive innovation), noted timely deliveries and minimal discrepancies in order fulfillment. The collaborative efforts to address potential quality issues proactively foster a reliable partnership. Regular audits have reinforced these findings, proving that adherence to stringent quality control measures not only benefits the vendor but ultimately enhances brand reputation and customer satisfaction. Acknowledgment of these achievements is vital for further motivating continuous improvement and commitment to quality standards.
Contact information for follow-up.
Vendor quality assurance feedback is critical for maintaining high standards in product delivery. A systematic evaluation is essential for ensuring consistent quality across various batches. For effective communication, having detailed contact information is vital, including phone numbers, email addresses, and names of quality assurance representatives. Utilize platforms such as Quality Management Systems (QMS) for documentation and tracking of feedback. Schedule regular follow-up meetings (every quarter recommended) to discuss performance metrics and areas for improvement. Maintaining an open dialogue with vendors can lead to stronger partnerships and increased product reliability, ultimately benefiting the entire supply chain.
Comments