In todayâs fast-paced business world, maintaining quality standards is crucial for building trust and ensuring customer satisfaction. When it comes to supplier relationships, addressing quality issues promptly can prevent costly disruptions and foster stronger partnerships. Our guide on how to effectively communicate supplier quality concerns will empower you to take proactive steps in resolving any discrepancies. Ready to enhance your supplier quality management? Read on to discover our comprehensive letter template!
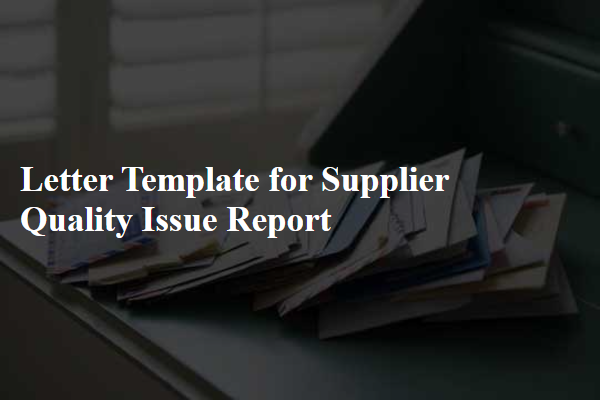
Clear Identification of the Issue
Clear identification of the quality issue is crucial in supplier management to ensure effective resolution and maintain product standards. For instance, defective parts (such as plastic components) received from Supplier XYZ caused production delays at the manufacturing facility in Chicago, resulting in a 20% decrease in output. The specific issue involves dimensional inaccuracies--dimensions exceeding tolerances by 0.5 millimeters on critical fits, which compromises assembly and functionality. Furthermore, the inspection report from October 2023 indicated that 15% of the shipments contained these discrepancies, leading to potential safety risks and customer dissatisfaction. Documentation, including batch numbers and inspection findings, can provide comprehensive insights into the recurring issues observed with Supplier XYZ, aiding in fostering improvements in their quality control processes.
Specifics and Details of the Defect
The supplier quality issue report highlights a critical defect identified in a recent shipment of electrical components, specifically resistors. These resistors, manufactured by XYZ Corp., arrived on November 15, 2023, and were intended for use in consumer electronics production. Inspection revealed that 15% of the units exhibited inconsistent resistance values, ranging from 10% to 30% deviation from the specified tolerance of +-5 ohms. This defect was particularly alarming given that the batch contained approximately 2,000 units, thereby impacting production schedules and product reliability. Furthermore, the defect could potentially lead to overheating issues in final devices, resulting in increased warranty claims and customer dissatisfaction. The affected components were sourced from a production run documented under batch number ABC12345, conducted in XYZ Corp's facility located in Shenzhen, China, which adheres to international quality standards. Immediate corrective actions are necessary to prevent further procurement of defective parts and to ensure compliance with production specifications.
Impact on Business Operations
Supplier quality issues can disrupt business operations significantly, leading to delays in production and increased costs. For instance, a defective batch of components (like microchips from a specific manufacturer) delivered to an automotive company might halt assembly lines, impacting delivery schedules of vehicles to customers. Quality issues can also lead to product recalls, damaging brand reputation and customer trust. Financially, companies may incur expenses related to rework, lost sales, and potential penalties. Furthermore, reliance on specific suppliers for critical materials increases vulnerability; if a significant supplier fails to meet quality standards, it creates a ripple effect, disrupting logistics and inventory management, ultimately affecting overall operational efficiency and profitability.
Previous Incident References (if applicable)
Previous incidents involving supplier quality issues often underscore the importance of maintaining strict quality control processes. For example, the 2022 recall of over 50,000 electronic components due to faulty solder joints highlighted the significance of adhering to IPC-A-610 standards for electronic assembly. Similarly, a 2021 incident reported by an automotive manufacturer revealed significant defects in batch number B1234, resulting in a costly factory shutdown and supply chain delays. In both cases, suppliers located in Shenzhen, China faced scrutiny as industry leaders emphasized the need for continuous improvement measures and regular audits to prevent recurrence. Tracking these past incidents aids in identifying patterns and implementing targeted corrective actions, ultimately enhancing overall product quality.
Proposed Resolution or Remediation Steps
Supplier quality issues often necessitate systematic approaches to address and rectify the problems identified. Key steps include conducting root cause analysis (RCA) to determine the underlying factors contributing to the quality discrepancy. Implementing corrective actions involves developing a detailed plan outlining specific measures, timelines, and responsible parties to ensure efficient remediation. Communication of findings and progress updates to relevant stakeholders is critical for transparency and accountability in the resolution process. Additionally, engaging in quality assurance training sessions for vendor personnel may enhance compliance with established standards, promoting long-term sustainability in product quality. Monitoring the effectiveness of implemented solutions through regular audits can further reinforce a commitment to continuous improvement in supplier partnerships.
Comments