Are you looking to streamline your shipping quality assurance process? In todayâs fast-paced world, ensuring that your products arrive in perfect condition is more critical than ever. A well-structured letter template can be a game-changer, helping you communicate effectively with your team and partners about quality standards and expectations. Letâs dive into the essential components of a shipping quality assurance letter that can enhance your operationsâkeep reading to discover more!
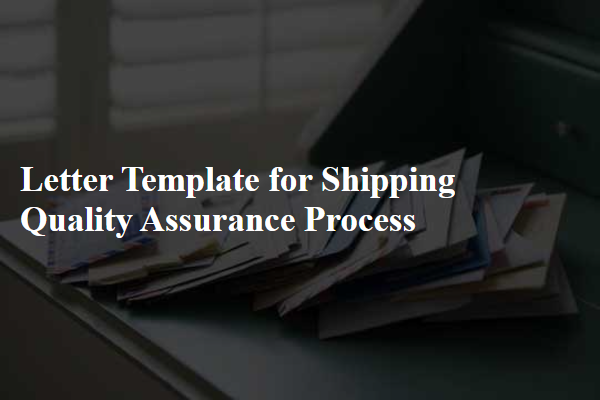
Clear Shipping Protocols
Clear shipping protocols are essential for ensuring product quality throughout the logistics process, impacting various aspects of supply chain management. Specific guidelines detailing packaging requirements, such as moisture-resistant materials and shock-absorbent cushioning (common in the shipping of electronics), contribute to reducing damage rates significantly, often by over 30%. Strict temperature controls (often maintained between -15 to 20 degrees Celsius for perishable goods) ensure the integrity of sensitive items during transportation. Moreover, standardized inspection checkpoints for shipments at different stages, such as pre-dispatch checks and receiving inspections at distribution centers, help identify potential quality issues early, fostering proactive resolution strategies. Adherence to industry compliance standards, like ISO 9001 for quality management systems, enhances operational efficiency while building customer trust in the reliability of the shipping process.
Quality Control Checkpoints
Quality control checkpoints in the shipping quality assurance process involve several critical measures to ensure product integrity and compliance with standards. Initial inspections occur at the manufacturing facility, where each item (quantities often totaling thousands) undergoes rigorous quality assessments and adherence to specifications outlined by regulations such as ISO 9001. Packaging checks follow, ensuring that materials (cardboard, bubble wrap) are suitable for transport, preventing damage during transit routes that may exceed thousands of miles. Final inspections at the distribution center (such as those located in major logistics hubs like Los Angeles or Memphis) assess the completeness of orders and proper labeling, while also confirming that items meet safety regulations mandated by agencies like the FDA or EPA. Throughout this process, tracking systems document each stage, providing visibility and accountability that facilitate timely resolution of any discrepancies before product delivery.
Documentation and Records Management
Shipping quality assurance processes involve systematic tracking of documentation and records management, ensuring regulatory compliance and operational efficiency. Essential documents consist of shipping manifests, packing lists, and inspection records, which detail the contents, quantities, and condition of goods shipped. Compliance with ISO 9001 standards mandates meticulous record-keeping to facilitate audits and traceability. The process incorporates digital solutions, such as cloud storage, enabling real-time access to documentation, enhancing collaboration among teams. Regular audits of records, conducted quarterly, ensure alignment with internal policies and external regulatory requirements, minimizing errors and boosting confidence in the shipping process. The centralized database system streamlines information retrieval and protects against data loss, creating a robust framework for assessing quality assurance in shipping operations.
Communication Channels
Effective communication channels play a crucial role in the shipping quality assurance process. Regular updates through email correspondence enhance coordination between the logistics team and quality assurance inspectors, ensuring timely resolution of shipping discrepancies. Utilizing project management platforms, such as Trello or Asana, allows for real-time tracking of shipments, facilitating transparency on delivery timelines and quality checks. Additionally, implementing instant messaging applications like Slack improves quick communication, enabling teams to address urgent quality issues immediately. Regular virtual meetings can further support collaborative discussions about shipping standards and quality benchmarks, fostering a culture of continuous improvement across the shipping department.
Continuous Improvement Feedback Loop
In shipping quality assurance processes, implementing a Continuous Improvement Feedback Loop is essential for enhancing operational efficiency and customer satisfaction. The feedback loop captures key performance indicators (KPIs), such as delivery times (averaging 48 hours for domestic shipments) and package integrity (aiming for a 99.5% intact delivery rate). Regular surveys from customers (collected quarterly) provide insights into their experiences and expectations, enabling teams to identify areas for improvement. Utilizing data analytics, trends are recognized, such as recurring delays at specific distribution centers like Memphis, Tennessee, enabling targeted interventions. Additionally, staff training sessions focus on best practices, ensuring all team members understand their role in maintaining quality standards. Documenting every phase of the process promotes accountability and empowers teams to innovate continuously, striving for excellence in shipping performance.
Comments