Are you looking to streamline your business processes and boost overall efficiency? In todayâs fast-paced world, evaluating and enhancing operational workflows is crucial for staying competitive. By pinpointing bottlenecks and identifying areas for improvement, you can unlock significant cost savings and productivity gains. Curious about how to get started? Read on for practical insights and a step-by-step guide!
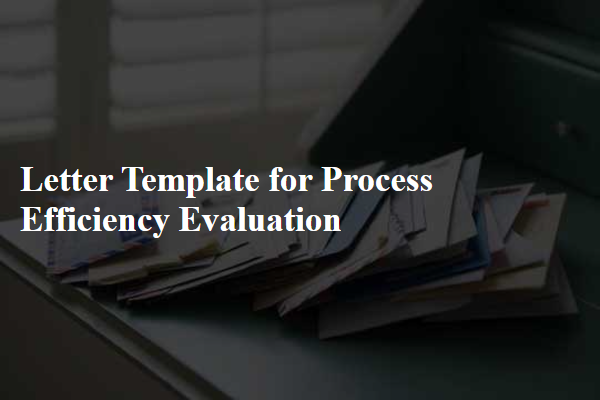
Subject Line and Title Clarity
Subject lines and titles must clearly convey the purpose of communication to enable efficient evaluation. For instance, a subject line like "Q3 Process Efficiency Evaluation Results" provides immediate context regarding timeframe and focus, essential for stakeholders, such as management teams in manufacturing firms, analyzing operational efficiency. Titles should be specific yet concise, employing keywords like "Efficiency Metrics," "Process Improvement," or "Performance Analysis" to enhance searchability in databases or email archives. Additionally, including relevant dates (e.g., "August 2023 Review") and the responsible department (e.g., "Logistics Optimization Team") fosters clarity and aids in quicker comprehension of the report's intent and key insights.
Introduction and Purpose Statement
In process efficiency evaluations, organizations aim to analyze operational workflows to identify areas for improvement. The primary purpose of this evaluation is to enhance productivity, reduce waste, and streamline procedures across various departments. By utilizing methodologies such as Lean Six Sigma, organizations can determine key performance indicators (KPIs) to measure effectiveness. Ongoing assessments will enable teams to implement best practices based on data-driven insights, fostering a culture of continuous improvement. Ultimately, this process leads to increased customer satisfaction and reduced operational costs, driving overall business success.
Criteria and Metrics for Evaluation
A process efficiency evaluation involves assessing various criteria and metrics to determine the effectiveness and productivity of operational workflows. Key criteria include cycle time (the total time to complete a process), throughput (the amount of output produced during a specific period), and resource utilization (the degree to which resources, such as manpower and materials, are used effectively). Metrics such as defect rates (the frequency of errors in a production output), cost per unit (the total cost incurred to produce each unit of product or service), and customer satisfaction scores (measured through surveys and feedback) further provide insights into performance levels. Regular monitoring of these indicators allows organizations to identify areas for improvement, streamline processes, and enhance overall efficiency and profitability.
Data Sources and Collection Methods
In evaluating process efficiency within organizational frameworks, identifying data sources and collection methods becomes crucial. Primary data sources, such as employee surveys (gathering qualitative insights) and operational metrics (quantitative data reflecting productivity), provide foundational information. Secondary data sources include industry reports and benchmarking studies (offering context and comparative analysis). Data collection methods such as interviews (in-depth perspectives from staff), observational studies (real-time assessment of workflows), and digital analytics (tracking performance through software metrics) contribute to a comprehensive understanding. The integration of diverse data sets enables a thorough analysis of efficiency, highlighting areas for improvement and fostering informed decision-making processes within the organization.
Recommendations and Action Steps
Process efficiency evaluations are essential for enhancing productivity in organizations. Key performance indicators (KPIs) like cycle time (the total time taken to complete a task), throughput (the rate of production or processing), and waste reduction metrics can provide insights into existing workflows. Implementing recommendations such as Lean methodologies (like value stream mapping to identify non-value-added activities) can significantly streamline processes. Action steps may include conducting team workshops at locations such as corporate offices or training centers, establishing regular review meetings to assess progress, and utilizing project management tools (like Asana or Trello) to track implementation stages. Continuous monitoring of these adaptations is crucial for evaluating their effectiveness and making necessary adjustments.
Comments