In today's fast-paced industrial world, it is crucial for businesses to communicate effectively, especially during significant events like a factory shutdown. Crafting a notice that is clear and concise ensures that all employees and stakeholders are informed about the necessary changes and implications. This article will guide you through the essential elements of a factory shutdown notice, emphasizing transparency and understanding throughout the process. So, if you're looking for a practical template and tips to navigate this sensitive situation, keep reading!
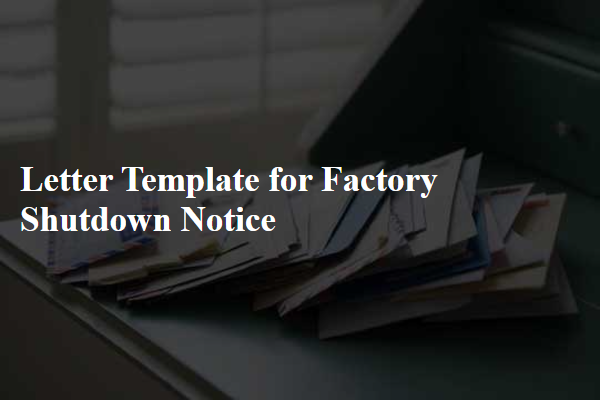
Reason for Shutdown
A factory shutdown notice communicates necessary information to employees and stakeholders regarding the temporary suspension of operations. Essential reasons for such a shutdown can include maintenance of machinery (scheduled repairs on equipment, crucial for workplace safety), safety inspections (mandatory checks to comply with regulatory standards), and inventory assessments (evaluation of stock levels to optimize production efficiency). Political events, such as labor strikes or government regulations (potential impact on operations), may also trigger shutdowns. Environmental factors, including severe weather conditions (hurricanes, floods, impacting operational capacity), could necessitate a halt in production. Each reason requires clear articulation to ensure transparency and maintain trust among all parties involved.
Schedule and Timeline
A factory shutdown notice often includes critical details regarding the schedule and timeline for the temporary cessation of operations. The planned shutdown for the manufacturing facility located in Springfield, USA, will commence on March 1, 2024, anticipated to last for four weeks. The operational pause aims to facilitate essential maintenance work, equipment upgrades, and safety inspections. Notification to employees will be communicated two weeks prior to the shutdown date, ensuring adequate preparation time. Employees are expected to complete any pending projects by the end of February 2024. Upon resumption of operations on April 1, 2024, training sessions will be held to familiarize staff with any new machinery and updated processes, enhancing productivity and safety standards in the workplace.
Employee Compensation and Benefits
The planned factory shutdown at the XYZ Manufacturing Plant will commence on November 15, 2023. This temporary closure, lasting for four weeks, is implemented for necessary repairs and maintenance of equipment. During this period, all full-time employees, approximately 250 individuals, will receive compensation based on their average weekly hours worked prior to the shutdown. Benefits such as health insurance coverage will remain active, ensuring employees access necessary medical services throughout the closure. Human Resources will provide detailed information regarding unemployment benefits and additional support programs available to assist employees during this transitional phase. Regular updates will be communicated via email to ensure all staff members stay informed.
Safety and Compliance Measures
Factory shutdown notifications emphasize the importance of safety and compliance measures necessary for maintaining worker health and asset integrity. Scheduled shutdowns ensure thorough inspections and maintenance of essential machinery, such as conveyor systems and robotic arms, guaranteeing adherence to Occupational Safety and Health Administration (OSHA) regulations. Compliance with Environmental Protection Agency (EPA) standards also necessitates regular assessments of waste management processes and emissions levels, promoting sustainable practices. In situations like these, detailed timelines are provided, specifying dates and expected durations of shutdowns, often encompassing critical activities like equipment upgrades or emergency repairs. Notifications often include reminders regarding personal protective equipment (PPE) requirements and emergency protocols to ensure employee safety during these periods.
Contact Information for Queries
Factory shutdown notices can significantly impact production schedules and employee livelihoods. In these situations, workers may seek clarification and have questions regarding next steps. Clear communication channels are essential. Providing contact information such as phone numbers, email addresses, and names of key personnel can facilitate a smoother transition during the shutdown period. A dedicated hotline may be established, operational from 9 AM to 5 PM, enabling employees to directly reach human resources or management teams for immediate assistance. Additionally, including a specific email address for inquiries can ensure timely responses. Location details, such as office address for in-person visits, can further support effective communication.
Comments