In todayâs fast-paced world, production downtime can feel like a setback that tests a companyâs resilience and adaptability. Itâs essential to communicate transparently with stakeholders about the reasons behind any interruptions in our workflow. By understanding the factors that contribute to downtimeâfrom machinery maintenance to supply chain disruptionsâwe can foster a supportive environment for everyone involved. If you'd like to delve deeper into the specifics of our recent downtime and how weâre addressing it, keep reading!
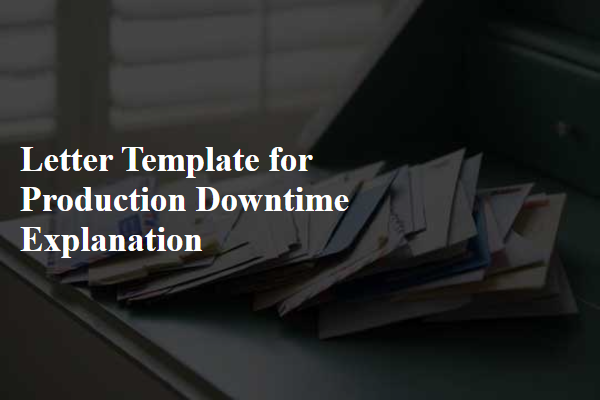
Detailed Incident Description
Unplanned production downtime can significantly impact manufacturing operations, such as those at the Tesla Gigafactory in Nevada. On September 15, 2023, a critical machinery failure occurred in line 4, halting the assembly of electric vehicle (EV) batteries. Maintenance technicians identified a malfunction in the robotic arms that assemble battery cells, specifically a failure in the servo motor, which led to a complete shutdown of that segment. Production was suspended for approximately 6 hours while engineers sourced replacement parts from local suppliers and performed necessary repairs. This downtime not only resulted in a backlog of orders but also affected the supply chain as battery production is vital for the subsequent assembly of Tesla Model Y vehicles. Proper response and resolution mechanisms are crucial to mitigate such incidents in the future.
Root Cause Analysis
Production downtime in manufacturing sectors often stems from equipment malfunctions, such as conveyor belt failures or CNC machine breakdowns. A recent incident at the Smith Manufacturing Plant (established 1995) lasted approximately six hours, resulting in significant delays. Root cause analysis revealed that a malfunctioning sensor (specifically a proximity sensor) caused misalignment in assembly. Investigation into the equipment revealed that the average lifespan of the sensor is typically three years, but this specific unit had only been operational for one year before failure. Additionally, maintenance logs indicated that routine checks were overlooked, leading to unmonitored wear and tear. This incident emphasizes the importance of regular equipment maintenance and timely replacement of critical components to minimize future production disruptions.
Impact Assessment
Production downtime can significantly disrupt operations across various industries, leading to financial losses and delayed delivery schedules. Common causes of production downtime include equipment failure (also known as machinery breakdown), which can result from wear and tear or lack of maintenance, human error during operation, and supply chain disruptions triggered by insufficient raw materials or logistics issues. Industries such as manufacturing can experience particularly severe impacts, with studies indicating that a single hour of downtime can cost companies between $100,000 to $300,000. The assessment of these impacts encompasses not only direct financial losses but also indirect effects such as decreased customer satisfaction and increased labor costs due to overtime. Addressing production downtime requires detailed analysis and proactive measures, including routine maintenance schedules and contingency plans to mitigate future disruptions in facilities located in regions like the Midwest United States, known for their extensive manufacturing capabilities.
Corrective Actions Implemented
Production downtime, especially in manufacturing environments like automotive or electronics, can significantly impact productivity and profitability. Recent incidents of equipment malfunction resulted in an extended halt of operations for three consecutive days, affecting output and delivery schedules. In response, a thorough root cause analysis was conducted, identifying a critical failure in the conveyor system linked to wear and tear on the drive motor. Immediate corrective actions included the replacement of the faulty motor and the implementation of a rigorous preventive maintenance schedule that ensures bi-weekly inspections and performance evaluations. Additionally, employee training sessions focused on operational best practices were instituted to enhance awareness of equipment handling, aiming to reduce future incidents and improve overall efficiency in production lines.
Preventative Measures
Production downtimes frequently disrupt manufacturing processes, leading to financial losses and delayed deliveries. In response to these challenges, companies implement preventative measures aimed at minimizing future occurrences. Regular maintenance of machinery, including automated assembly lines in factories, can extend equipment lifespan and enhance performance. Staff training sessions, held quarterly, improve operational efficiency and reduce human error. Inventory management systems using real-time data analytics allow for better forecasting and timely ordering of materials, reducing shortages that can halt production. Additionally, adherence to safety protocols can prevent accidents that contribute to unexpected downtimes. Effectively addressing these factors can significantly improve overall productivity and operational stability in the manufacturing sector.
Comments