Have you ever wondered how we can make products safer for everyone? As consumers, we all want the peace of mind that comes with knowing the items we use daily are thoroughly tested and meet high safety standards. In this article, weâll explore the latest advancements in product safety improvements and the crucial steps companies are taking to protect their customers. So, letâs dive in and uncover the innovative solutions making a difference today!
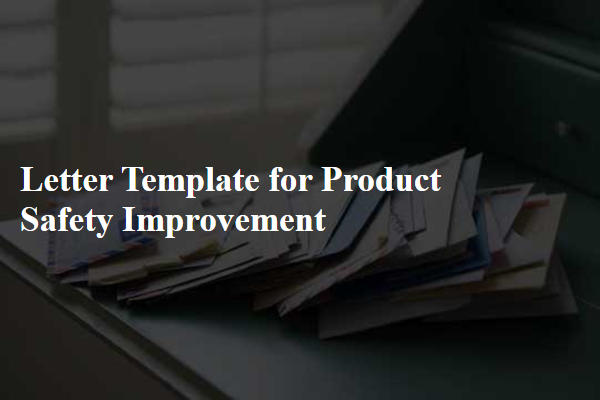
Clear and concise communication.
Product safety improvements require systematic evaluations and proactive measures to ensure consumer protection. Regular assessments conducted according to ISO 9001 standards can identify potential hazards associated with manufacturing processes, material selection, and product design. Effective communication strategies, including product labeling with safety warnings and user manuals that highlight best practices, can enhance public awareness. Implementing rigorous testing protocols, such as durability and performance evaluations in compliance with ASTM standards, can significantly mitigate risks. Continuous feedback loops from consumer reports and product return data can inform necessary adjustments, promoting a culture of safety within the organization.
Legal and regulatory compliance.
Product safety improvement necessitates adherence to legal and regulatory compliance standards set forth by organizations such as the Consumer Product Safety Commission (CPSC) in the United States. Compliance involves rigorous testing protocols to ascertain that products meet safety requirements, mitigating risks associated with hazards like choking, burns, or electrical shocks. Manufacturers must conduct risk assessments based on detailed guidelines established in the ASTM International standards, ensuring that materials used, such as toxic-free plastics or flame-retardant fabrics, comply with regulations. In addition, regular audits and certifications from recognized bodies like Underwriters Laboratories (UL) play a critical role in maintaining safety standards, safeguarding public health, and ensuring that products can withstand real-world use scenarios without causing harm. Effective communication with both consumers and regulatory agencies is essential in fostering trust and transparency regarding product safety.
Tone of assurance and responsibility.
Safety protocols in product manufacturing play a critical role in consumer protection. Manufacturers must adhere to rigorous standards, such as ISO 9001, which emphasizes continual improvement in quality management systems. Events, like product recalls, underscore the importance of proactive safety measures. For instance, the 2020 recall of 1.5 million children's toys due to lead paint highlighted the need for stringent safety testing before market release. Collaborations with safety organizations, including the Consumer Product Safety Commission (CPSC), can enhance compliance and consumer trust. Regular audits and consumer feedback mechanisms are essential for identifying potential hazards and implementing timely improvements, ensuring that products remain safe for use in homes across the United States and beyond.
Guidelines on safety practices.
Product safety improvement encompasses critical guidelines on safety practices essential for manufacturing and consumer use. Regular inspections should be conducted during the production process, ensuring compliance with safety standards established by organizations such as the American National Standards Institute (ANSI). Furthermore, implementing rigorous testing protocols before product launch can identify potential hazards that may arise from design flaws or material defects. Proper labeling of products, including safety warnings and usage instructions, is vital for consumer awareness. Additionally, training programs for employees about safety practices can enhance workplace safety, reduce accidents, and foster a culture of safety. Collaboration with safety regulators and industry associations can also provide valuable insights into best practices and emerging safety technologies, ultimately leading to improved product safety and consumer trust.
Contact information for support.
Product safety improvements require effective communication with consumers. Clear contact information for support can enhance customer trust and ensure swift assistance. Including details such as a dedicated customer service phone line, available weekdays from 9 AM to 5 PM Eastern Time (ET), and a responsive email address monitored within 24 hours can streamline inquiries. Highlighting an online chat feature on the company website can provide immediate assistance. Ensuring multilingual support further accommodates diverse customer bases, improving accessibility. Providing a physical mailing address for formal complaints or inquiries adds transparency and fosters confidence in the brand's commitment to safety.
Comments