When it comes to ensuring the highest quality standards in your supply chain, a thorough quality assurance checklist is essential. This comprehensive tool not only helps you evaluate your suppliers but also fosters a stronger partnership built on trust and accountability. By using this checklist, you'll be well-equipped to identify potential issues early on and keep your business running smoothly. Ready to dive deeper into creating an effective supplier quality assurance checklist? Keep reading!
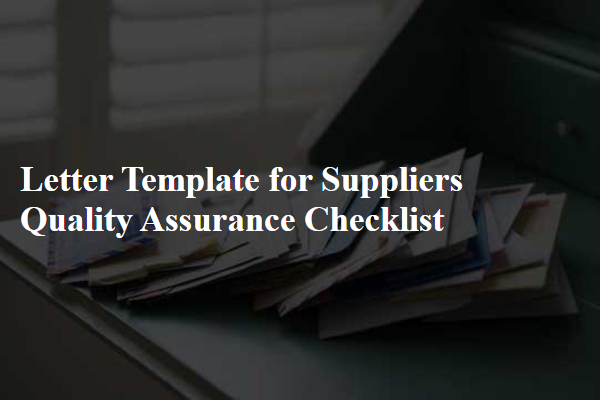
Clear quality standards and specifications
Quality assurance checklists play an essential role in maintaining high standards for suppliers in various industries. Clear quality standards and specifications outline the benchmarks that products must meet to ensure safety and performance. These benchmarks encompass criteria such as material composition, dimensional tolerances, and performance metrics, with specific numerical values that align with industry regulations such as ISO 9001. Consistent compliance with these standards helps prevent defects and ensures that suppliers deliver products, like automotive components or electronic devices, that adhere to quality expectations. The checklist must include sections for inspection methods, frequency of checks, and documentation practices to guarantee traceability and accountability throughout the supply chain. For effective monitoring, annotated guidelines on corrective actions and continuous improvement processes should be integrated to enhance supplier performance and product reliability.
Comprehensive inspection and testing protocols
A comprehensive supplier quality assurance checklist ensures high standards in the inspection and testing processes for supplied goods. Key elements in the checklist include incoming material verification, where suppliers must provide certificates of conformity to relevant standards such as ISO 9001, ensuring consistent quality. Detailed visual inspections of products, including dimensions and surface finishes, should adhere to specified tolerances (for instance, +-0.5mm for metal parts). Additionally, functionality tests must be documented, stipulating performance metrics (e.g., 98% operational efficiency for electronic components) and environmental requirements, such as resistance to temperatures exceeding 60 degrees Celsius. Furthermore, procedures for handling non-conforming products must be outlined, necessitating immediate identification and isolation of defective items with corrective actions reported to stakeholders. Regular audits of supplier facilities should also be included, assessing compliance with safety regulations and quality management systems to maintain the integrity of the supply chain.
Supplier performance evaluation criteria
A comprehensive supplier performance evaluation criteria can significantly enhance the quality assurance process in procurement. Key metrics typically assessed include delivery timeliness, measured by the percentage of on-time shipments, and quality defect rates, often expressed as the number of defective units per thousand produced. Cost competitiveness is evaluated by comparing quoted prices against market averages. Additionally, communication effectiveness is assessed through response times to inquiries and issue resolution rates. Compliance with industry standards, such as ISO 9001 certification, is a critical factor, reflecting the supplier's commitment to maintaining high quality. Evaluations also include sustainability practices, where suppliers are expected to adhere to environmental regulations and guidelines, such as those set forth by the Environmental Protection Agency (EPA), contributing to wider corporate social responsibility initiatives. For records, suppliers should provide documentation like the usage of quality management systems, detailed vendor profiles, and historical performance data to substantiate evaluations. Regular audits or assessments, preferably quarterly, can further ensure ongoing compliance and identify areas for improvement in the supplier's performance.
Communication and feedback mechanisms
Effective communication and feedback mechanisms are essential in supplier quality assurance processes to ensure that products meet specified standards. Regular updates from suppliers can include status reports on production timelines and quality control measures, with periodic meetings scheduled, ideally quarterly, to discuss performance metrics. Clear feedback loops should be established, allowing for immediate reporting of defects or non-conformities, facilitating swift resolution of issues. Documented communication channels, such as email or dedicated platforms like Vendor Management Systems, ensure consistent tracking of quality updates. Additional tools like satisfaction surveys can gauge supplier performance and identify areas for improvement, ensuring continuous enhancement of product quality and adherence to contractual obligations.
Corrective action and continuous improvement plans
A comprehensive supplier quality assurance checklist focuses on corrective actions and continuous improvement initiatives, key elements in maintaining high standards. The checklist includes identifying defects in production processes, necessitating root cause analysis (RCA) to understand underlying issues. Corrective action plans must be documented per ISO 9001 standards, detailing immediate fixes and long-term strategies. Continuous improvement plans, such as the Kaizen methodology, aim for incremental enhancements through employee training and process optimization. Regular audits (quarterly or biannually) are essential to ensure adherence to quality requirements and track progress. Engaging suppliers through performance reviews encourages collaboration towards mutual improvement goals, fostering a culture of quality assurance.
Letter Template For Suppliers Quality Assurance Checklist Samples
Letter template of Supplier Quality Assurance Checklist for Initial Assessment
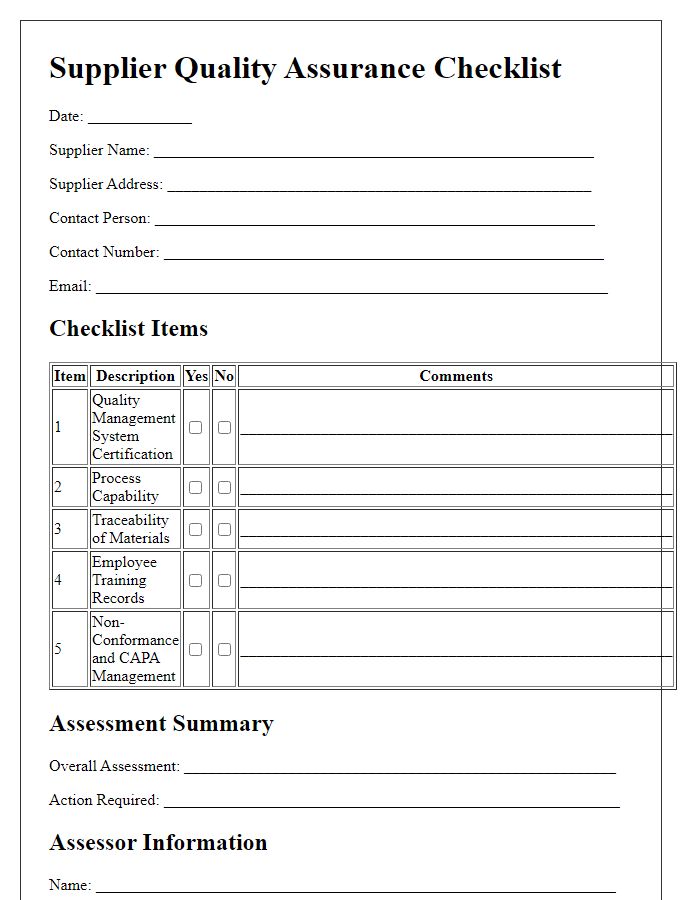
Letter template of Supplier Quality Assurance Checklist for Ongoing Compliance
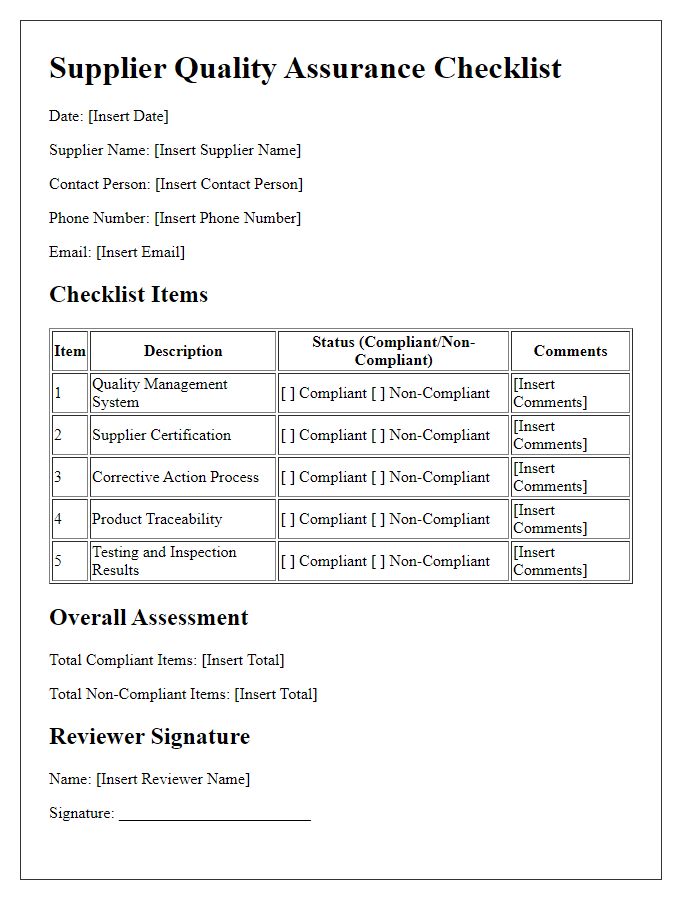
Letter template of Supplier Quality Assurance Checklist for Audit Preparation
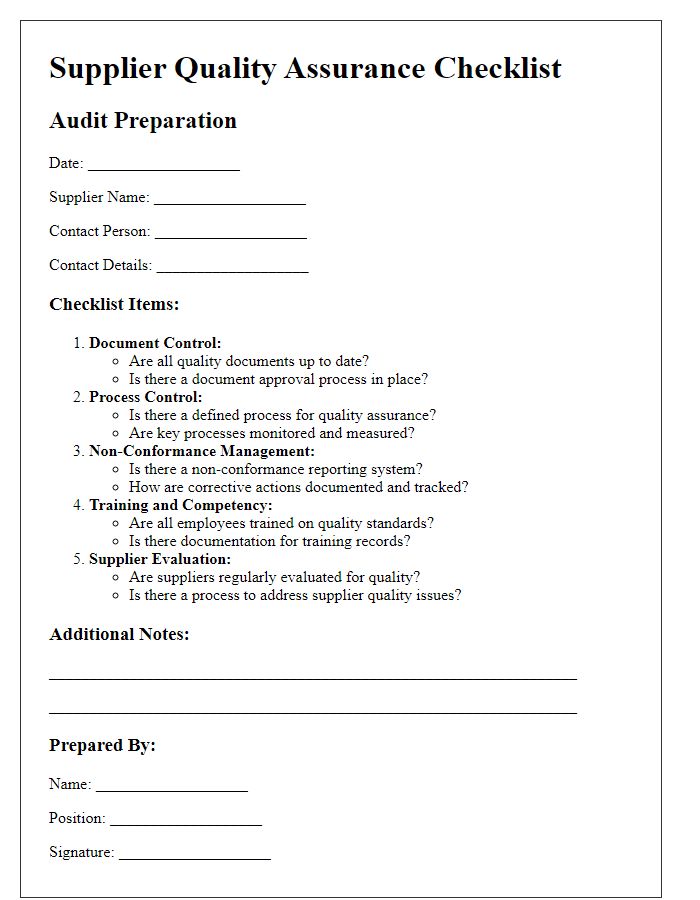
Letter template of Supplier Quality Assurance Checklist for Product Launch
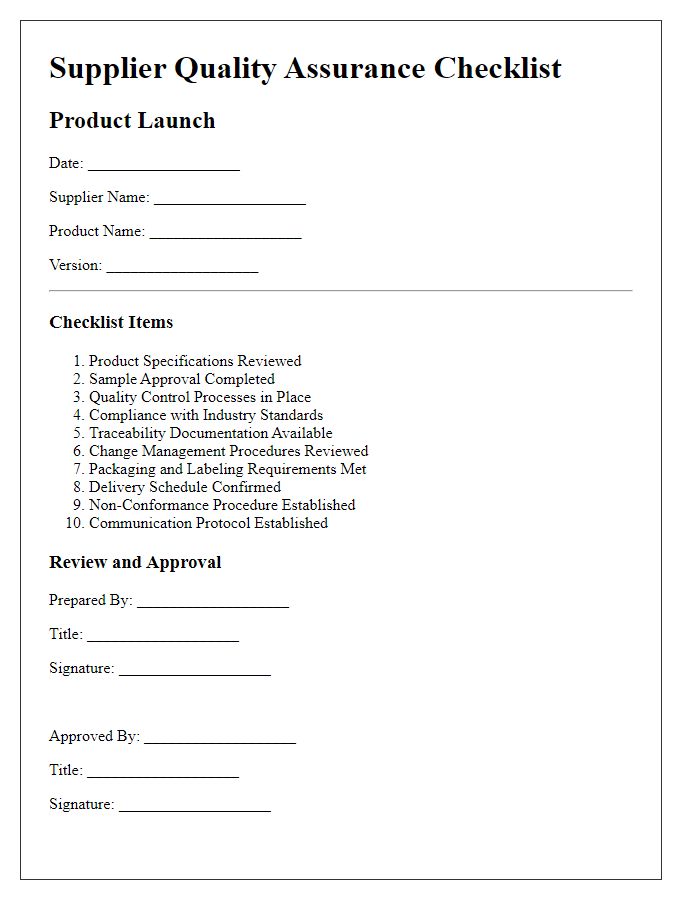
Letter template of Supplier Quality Assurance Checklist for Corrective Action Requests
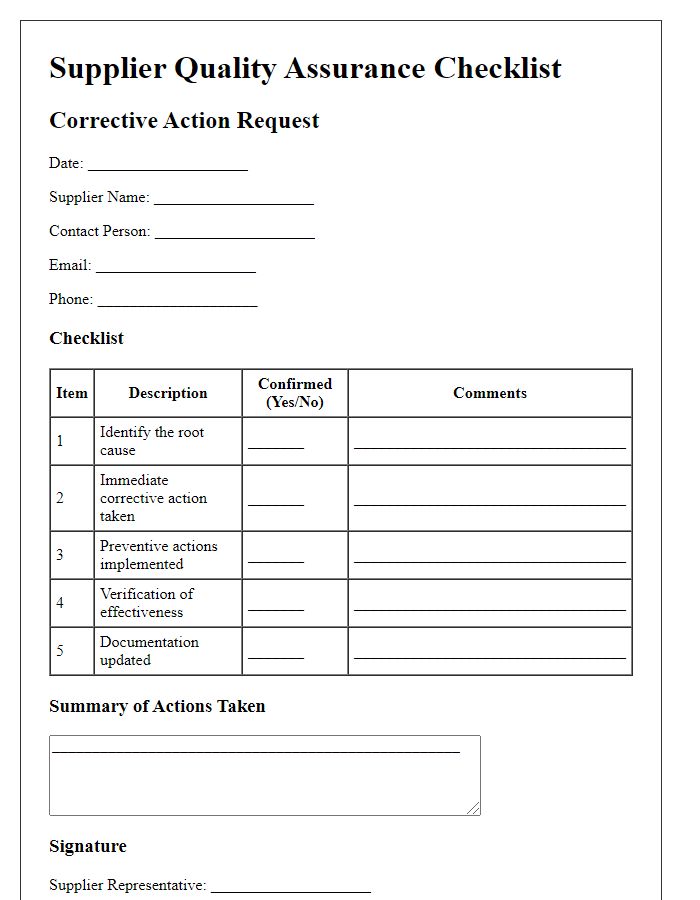
Letter template of Supplier Quality Assurance Checklist for Training and Support
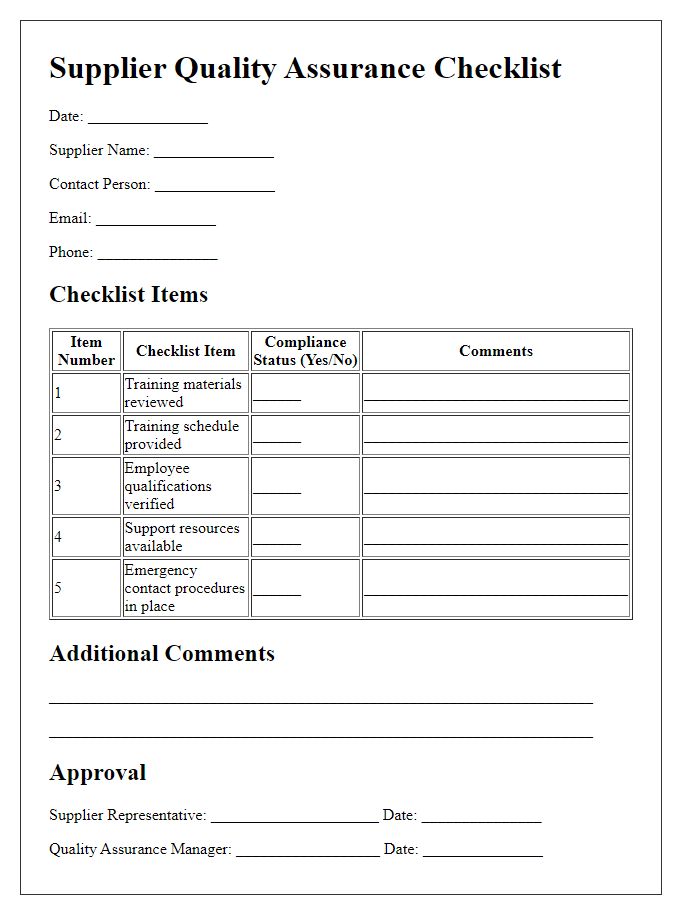
Letter template of Supplier Quality Assurance Checklist for Risk Management
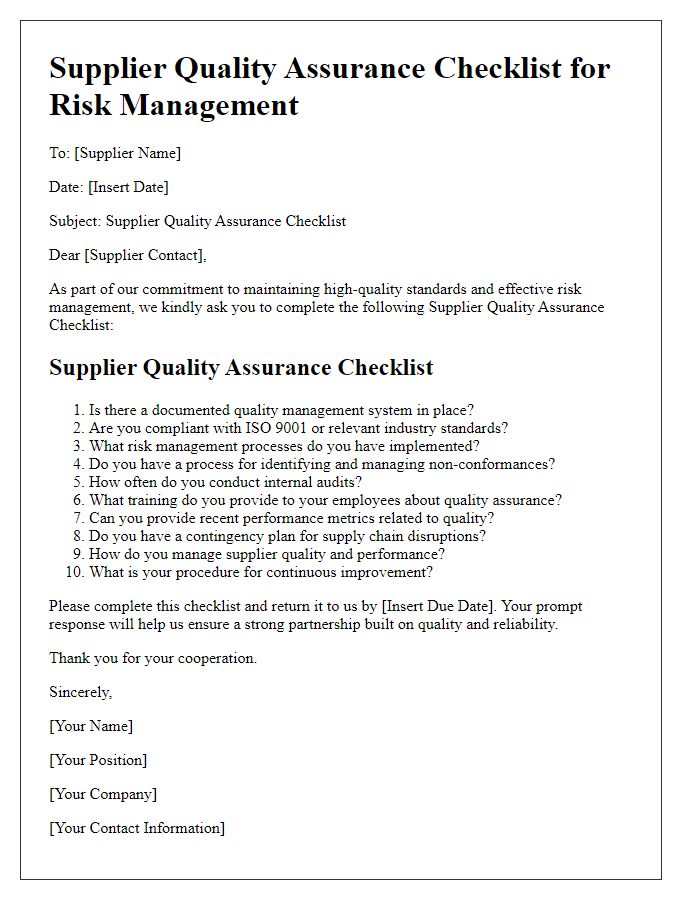
Letter template of Supplier Quality Assurance Checklist for Supplier Performance Review
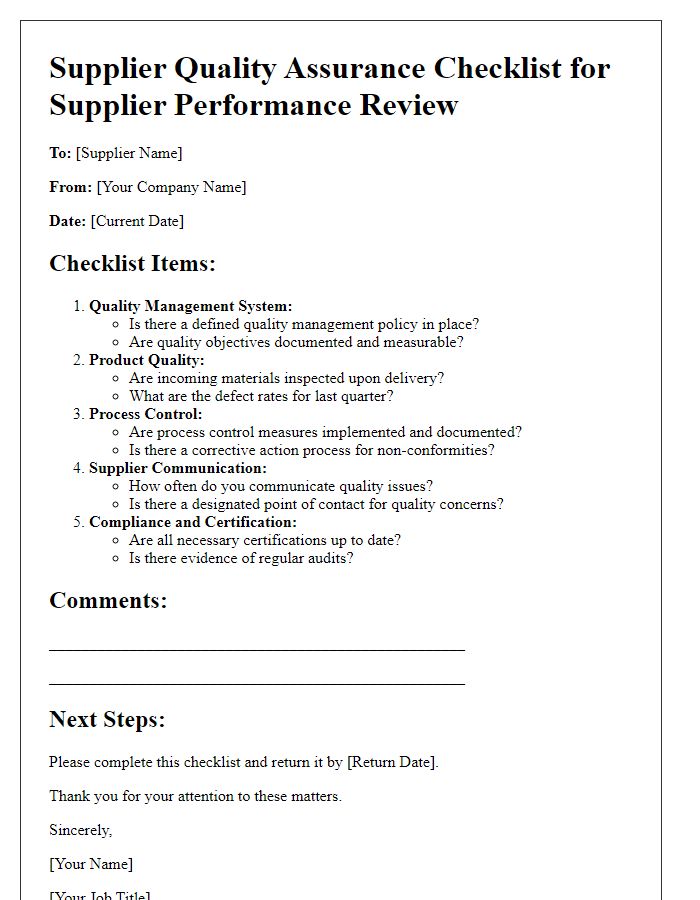
Letter template of Supplier Quality Assurance Checklist for Contract Evaluation
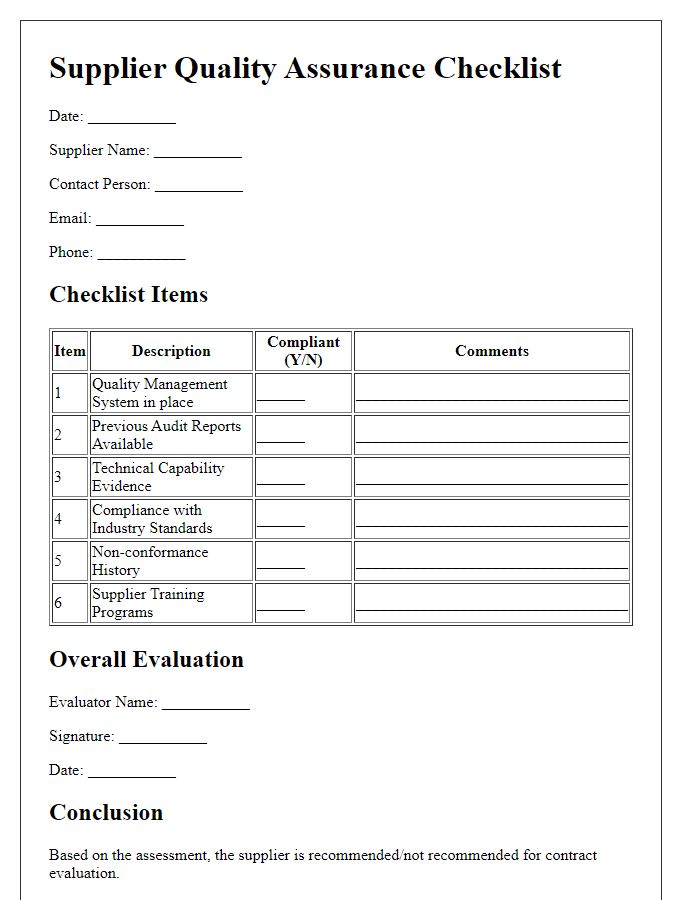
Comments