Are you looking to improve your attic ventilation compliance? Proper attic ventilation is crucial for maintaining a healthy home environment, and understanding the requirements can feel overwhelming. In this article, we'll break down the key components of attic ventilation and how they contribute to energy efficiency and mold prevention. So, stick around to learn more about how to ensure your attic is in compliance!
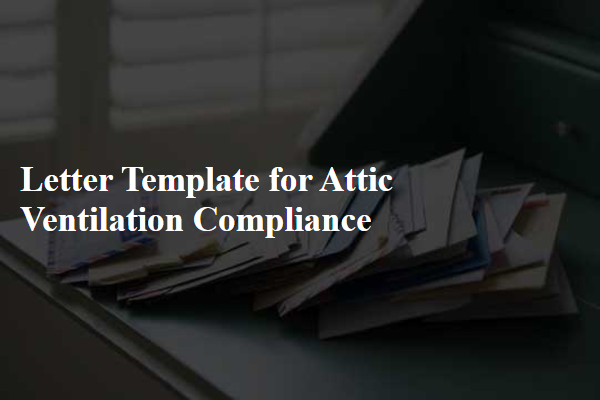
Building Code Requirements
Compliance with attic ventilation, according to the International Building Code (IBC), mandates adequate airflow to prevent moisture buildup and promote energy efficiency. Attics should have a minimum vent area calculated based on the size of the space, generally requiring at least 1 square foot of vent area for every 300 square feet of attic floor area. Effective ventilation systems must include both intake vents, often positioned near the eaves or soffits, and exhaust vents, typically located at or near the roof ridge. Local building authorities in areas like California under Title 24 standards emphasize the significance of appropriate ventilation in reducing energy consumption and prolonging roof life. Compliance inspections may call for a detailed analysis of existing ventilation to ensure alignment with building code requirements, ensuring safety and structural integrity.
Ventilation Calculation
Proper attic ventilation is crucial in ensuring optimal energy efficiency and extending the lifespan of roofing materials. A ventilation calculation must consider various factors such as the total attic area, typically measured in square feet, and the appropriate vent sizes, which must adhere to local building codes. The recommended ratio for ventilation is 1 square foot of net free ventilating area (NFVA) for every 300 square feet of attic space, although some jurisdictions may require a ratio of 1:150. This includes both intake ventilation located at the eaves or soffits and exhaust ventilation placed at the ridge or high points of the roof. The use of static vents, turbine vents, or powered attic ventilators should be examined, depending on specific climate conditions and design requirements. Regular assessments are necessary to determine if the current ventilation system meets these standards and efficiently mitigates moisture build-up and heat accumulation.
Material Specifications
Proper attic ventilation compliance requires specific material specifications to ensure optimal airflow and moisture control. The primary materials include high-density polyethylene vent pipes, typically with a diameter of 4 inches, designed to facilitate exhaust and intake. Ridge vents, often made from durable aluminum or plastic, should cover a minimum of 50% of the ridge length, promoting efficient airflow. Soffit vents, constructed from weather-resistant vinyl or aluminum, need to maintain a minimum net free area (NFA) of 1 square foot for every 300 square feet of attic space. Continuous soffit vents should span the full length of the eaves, allowing air to enter easily. Additionally, baffles made from rigid foam or polyethylene should be installed along the roof eaves to prevent insulation blockage, ensuring a clear path for air movement. Regular inspection of these materials for corrosion or damage can help maintain compliance with local building codes, ensuring a healthy attic environment.
Installation Guidelines
Proper attic ventilation is essential for maintaining a healthy and energy-efficient home environment. Effective ventilation systems, such as ridge vents, soffit vents, or gable vents, allow for adequate airflow (a minimum of 1 square foot of vent area per 150 square feet of attic space), helping to regulate temperature and moisture levels. Installation should adhere to local building codes, often referencing guidelines from organizations like the American Society of Home Inspectors (ASHI) or the National Roofing Contractors Association (NRCA). Ventilation covers should be installed to prevent debris entry while allowing free airflow, ensuring the elimination of excess heat (which can exceed 140 degrees Fahrenheit in poorly ventilated attics) and moisture (which can lead to mold and wood decay). Inspect regularly for blockages, ensuring that vent areas are unobstructed by insulation, to maintain optimal airflow and prolong roof life.
Inspection and Maintenance Procedures
Effective attic ventilation is crucial for maintaining a healthy and energy-efficient home environment. The recommended ventilation ratio is 1 square foot of ventilation for every 300 square feet of attic space, as per building codes in various regions. Proper inspection involves checking for obstructions in vents, with common barriers including insulation, debris, and animal nests. Maintenance procedures should include clearing any blockages, ensuring all vents (especially ridge and soffit) are functioning properly, and inspecting for signs of moisture or mold growth, which can indicate poor air circulation. Regular inspections, ideally twice a year and after significant weather events, can prevent costly repairs and enhance energy efficiency by regulating attic temperature, thus prolonging the lifespan of roofing materials and optimizing HVAC performance.
Letter Template For Attic Ventilation Compliance Samples
Letter template of attic ventilation compliance notification to homeowners.
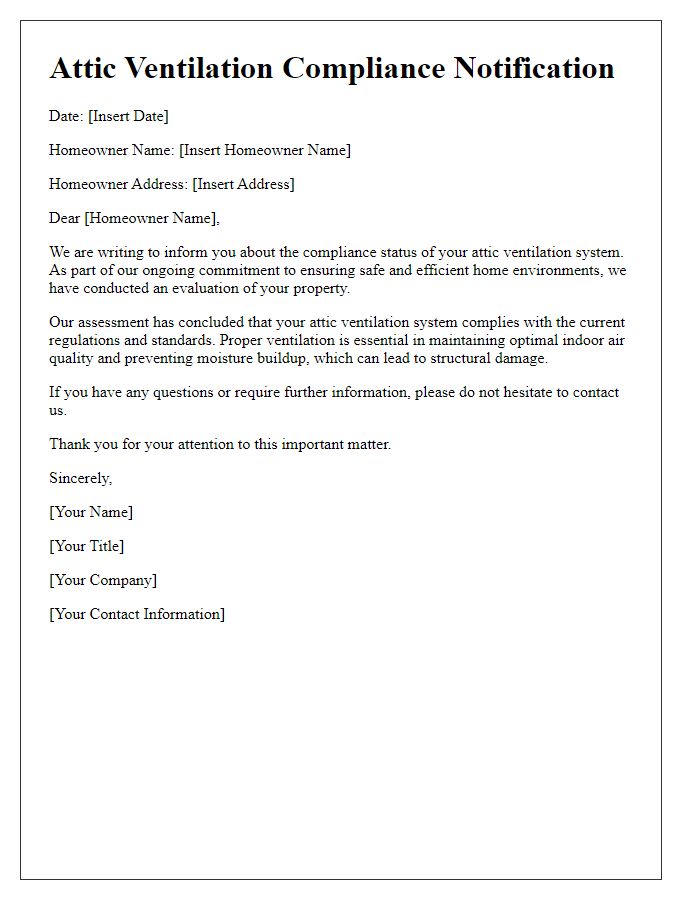
Letter template of attic ventilation compliance follow-up for contractors.
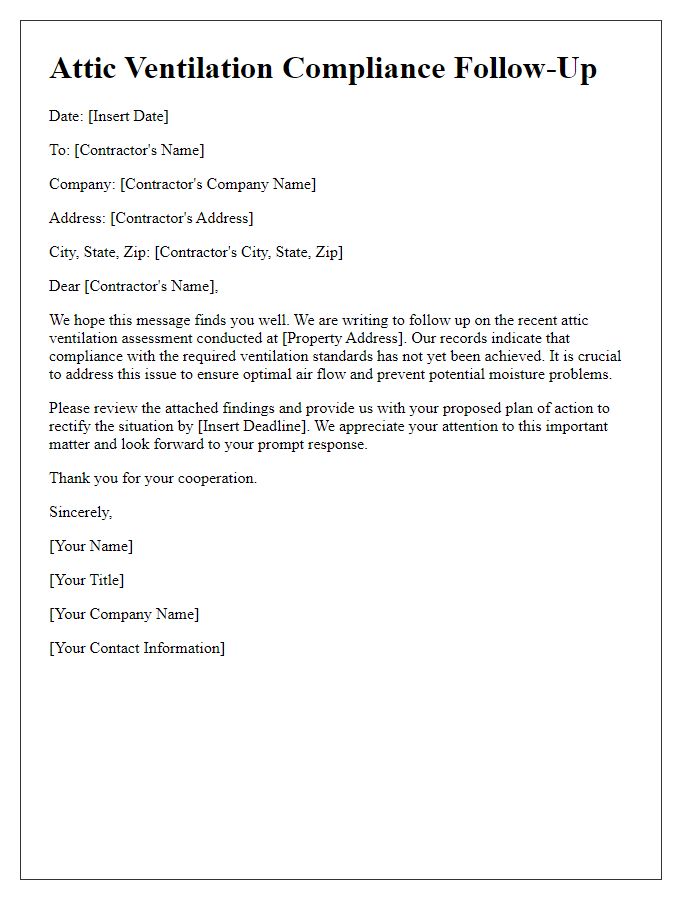
Letter template of attic ventilation compliance reminder for property managers.
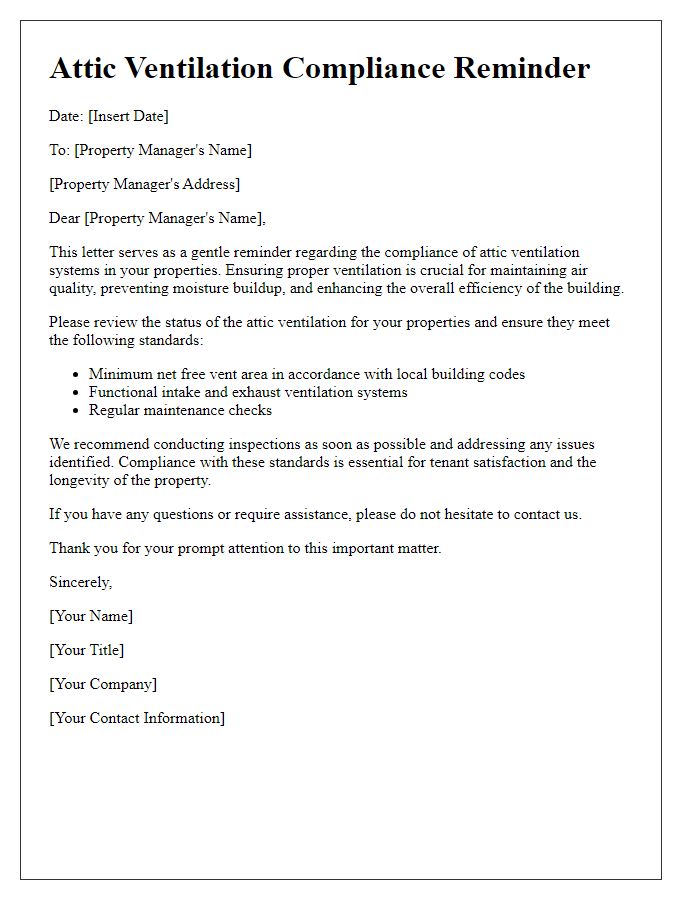
Letter template of attic ventilation compliance inquiry for local authorities.
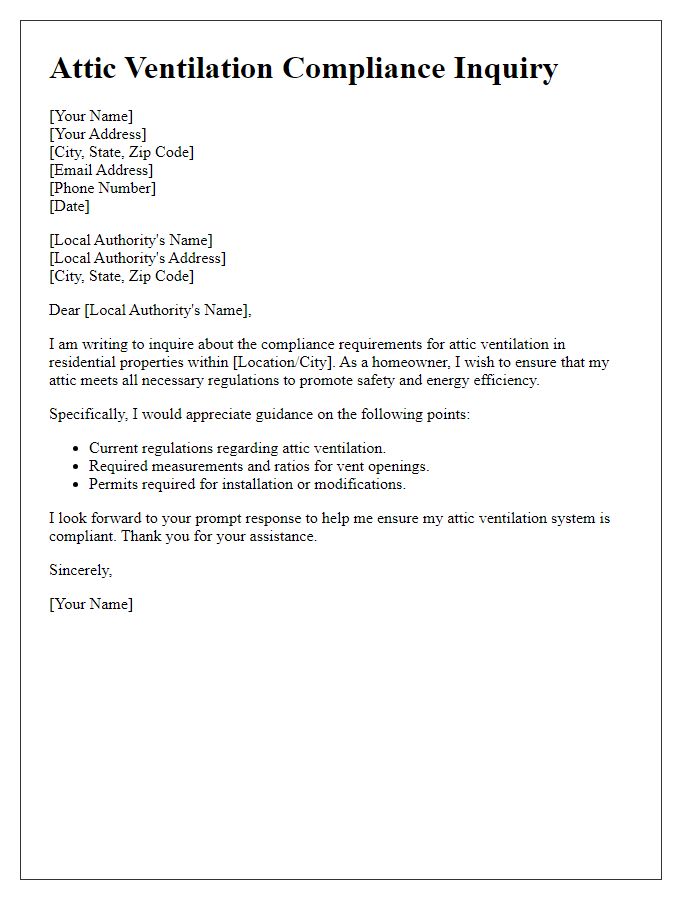
Letter template of attic ventilation compliance explanation for tenants.
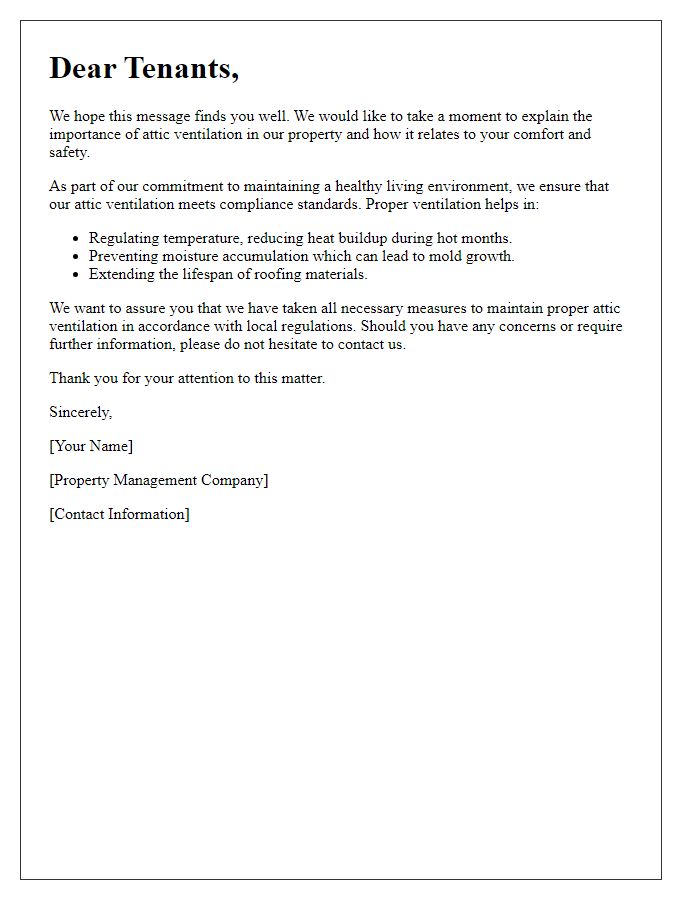
Letter template of attic ventilation compliance approval for renovations.
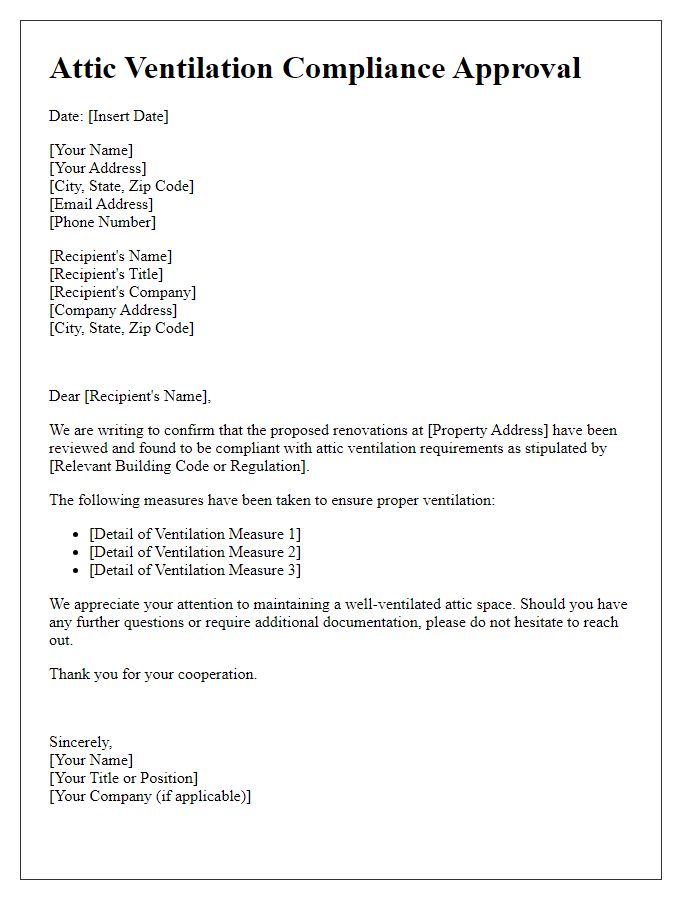
Comments