When it comes to establishing strong partnerships in the manufacturing sector, a well-crafted supply agreement is essential. This document not only outlines the terms and conditions of the relationship but also ensures clarity and mutual understanding between both parties. From pricing and delivery schedules to quality control measures, every aspect plays a crucial role in fostering a successful collaboration. If you're ready to explore how to create an effective manufacturing supply agreement, keep reading!
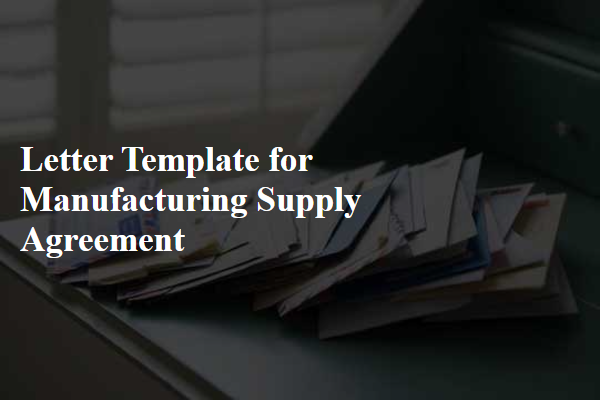
Parties Involved
A manufacturing supply agreement necessitates clearly identifying the parties involved. The supplier, typically a company specializing in the production of goods, may have significant experience in sectors such as electronics, textiles, or automotive components. The purchaser, often an entity like a retailer or wholesaler, relies on the supplier for consistent delivery of quality products. Key details include the full legal names of both parties, registration numbers for businesses, and primary locations, such as headquarters or manufacturing facilities. This foundational information lays the groundwork for the contract, ensuring both parties understand their roles in the manufacturing process, from raw material sourcing to finished product delivery. Implementing this clarity safeguards against misunderstandings and potential disputes, facilitating smoother business operations.
Product Specifications
Product specifications play a crucial role in manufacturing supply agreements, defining the exact requirements for materials and components. These specifications should include detailed information such as dimensions, weight, and tolerances of products, commonly measured in millimeters or grams. For instance, an electronic component might require specifications like a voltage rating of 5 volts and a current rating of 2 amperes. Additionally, materials must be specified, such as plastic types (like ABS or PVC) with relevant standards (ISO 9001 for quality) and certifications (such as RoHS for environmental compliance). Surface finishes may also require description, including options like matte or glossy, which impact aesthetics and functionality. Packaging specifications should state dimensions of outer cartons and packing density to ensure safe transportation. Clear labeling guidelines must be included for compliance with regulations in regions like the EU or North America. Overall, precise product specifications enhance quality control and ensure mutual understanding between manufacturers and suppliers.
Payment Terms
In the context of a manufacturing supply agreement, payment terms serve as critical components that govern the financial transactions between parties involved. Predefined payment schedules, such as net 30 or net 60, detail the timeframes (30 or 60 days post-invoice) within which payments are due after the delivery of goods (raw materials or finished products). Payment methods include electronic funds transfer (EFT), credit card transactions, or checks, ensuring a streamlined process. Late payment penalties may apply, typically a percentage of the outstanding amount (e.g., 1.5% per month), incentivizing timely payments and maintaining cash flow. Additionally, provisions for advance payments or deposits may be stipulated, requiring upfront investment before production begins, mitigating financial risk for suppliers. Revisions to payment terms must be clearly documented and agreed upon, reflecting any negotiations or adjustments in the supply relationship.
Delivery Schedules
Delivery schedules in a manufacturing supply agreement specify the timelines for the shipment of goods from suppliers to manufacturers. These schedules ensure timely delivery of materials like steel, plastics, or microchips, crucial for production processes. Typically, suppliers agree to deliver goods on predetermined dates or within defined timeframes, such as weekly shipments or monthly batches. Factors like lead time, production capacity, and transportation logistics are essential in establishing these schedules. Clear delivery terms help minimize production delays, maintain inventory levels, and manage supplier relationships efficiently. Detailed documentation ensures accountability and addresses potential issues related to missed deadlines or quality control.
Termination Clauses
Termination clauses in manufacturing supply agreements outline the conditions under which either party may terminate the agreement before its completion. Commonly included conditions involve breaches of contract, such as failure to deliver goods on time or substandard quality, typically defined by industry standards. Notice periods, often ranging from 30 to 90 days, must be adhered to ensure proper communication of termination intentions. Furthermore, provisions for immediate termination may apply in cases of insolvency or bankruptcy, protecting parties from undue risk. The clauses may also delineate consequences of termination, including the return of unsold inventory or completion of pending transactions, ensuring a clear process for both parties in the event of an early conclusion to their business relationship.
Letter Template For Manufacturing Supply Agreement Samples
Letter template of Manufacturing Supply Agreement for Electronic Components
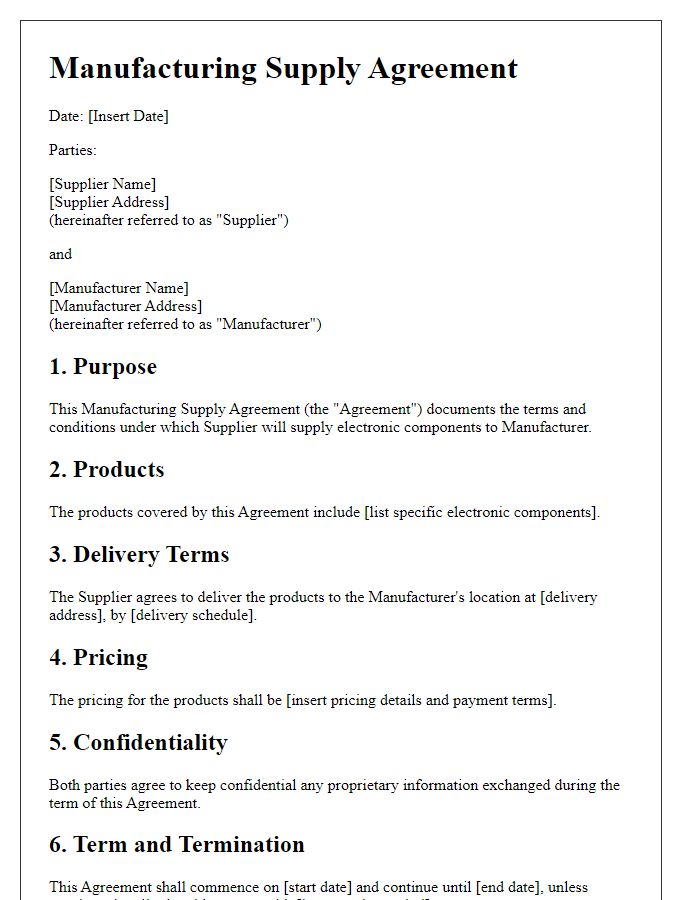
Letter template of Manufacturing Supply Agreement for Industrial Equipment
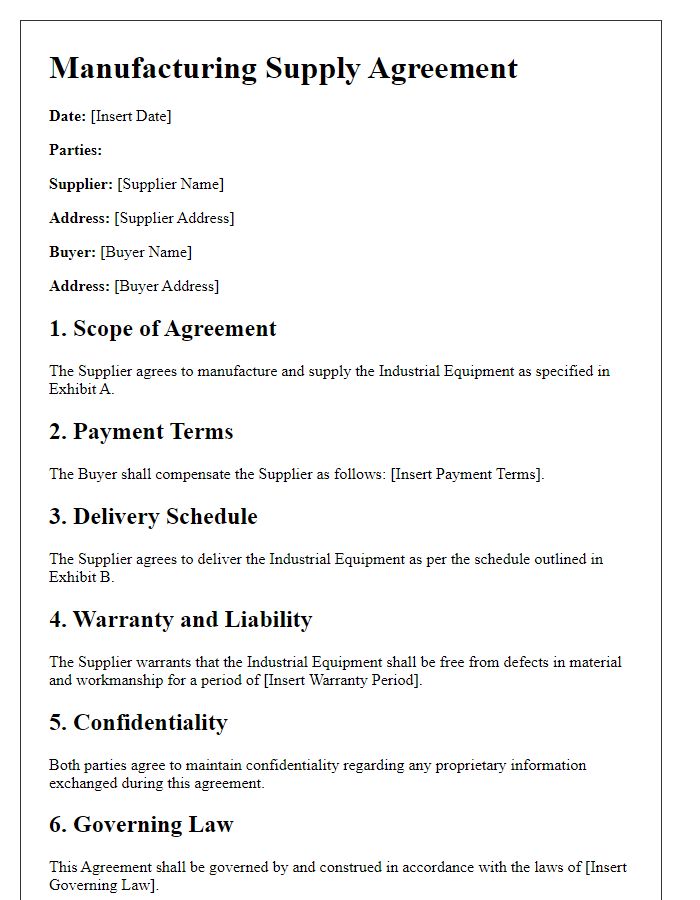
Comments