Have you ever found yourself grappling with a faulty product and unsure of how to address the issue? If so, you're not aloneâmany people face the dilemma of navigating the tricky waters of faulty material reports. Writing a clear and concise letter can make all the difference in resolving your concerns effectively. Join us as we explore a comprehensive template that will guide you through this process with ease!
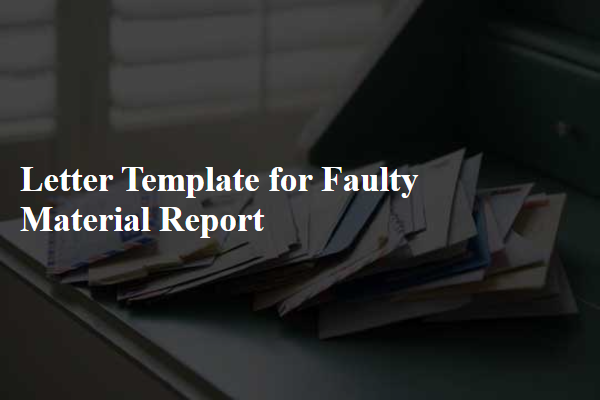
Clear identification of the faulty material
The faulty material, identified as Batch #12345 of High-Density Polyethylene (HDPE) sourced from Polymer Industries Ltd., exhibited significant degradation, resulting in an unexpected reduction in tensile strength, measured at 22 MPa instead of the expected 30 MPa. This batch was utilized in the manufacturing process for components in the automotive sector, specifically for the production of fuel tanks at the Toyota assembly facility located in Georgetown, Kentucky. Tests conducted on the material revealed visible cracking and discoloration, with an accelerated aging assessment showing deterioration within a mere 30 days of exposure to UV light at levels exceeding 300 watts per square meter. This deviation from the quality standards set forth in ISO 9001:2015 is of grave concern and necessitates immediate attention to prevent further complications in production and product safety.
Detailed description of the defect or issue
A faulty material can significantly impact the quality of production in manufacturing processes. For instance, in steel manufacturing, defects such as cracks or inclusions can lead to structural failures in buildings or bridges, raising safety concerns. Specific dimensions, such as improperly sized steel beams (varying more than +-1 millimeter), can disrupt assembly processes. Additionally, visual inspection may reveal surface irregularities or discoloration, indicative of manufacturing mishaps. Material properties, like tensile strength (measured in megapascals), may fall below industry standards, compromising overall durability and leading to costly repairs. Timely reporting of these defects is crucial to coordinate replacements and prevent further disruptions in supply chains, particularly in high-stakes industries like automotive and construction.
Impact on operations or projects
A faulty material, such as substandard steel beams used in the construction of high-rise buildings, can significantly disrupt operations and lead to extensive project delays. Instances of tensile strength below the industry standard of 400 MPa can compromise structural integrity, resulting in the need for additional inspections and potential redesigns. For example, construction projects in urban areas like New York City may face penalties for exceeding deadlines while rectifying issues caused by the faulty materials. Moreover, the reallocation of resources, including labor and equipment, can lead to increased operational costs, estimated at an additional 10-15% of the project budget. Prolonged issues can also damage relationships with stakeholders, including investors and local governments, impacting future project approvals and financing opportunities.
Supporting documentation and evidence
A comprehensive faulty material report details defective items, including specific product identification numbers and descriptions of anomalies observed during inspection. Supporting documentation encompasses photographs illustrating the damaged materials, quality control checklists highlighting missed standards, and communication records with suppliers regarding previous issues encountered, all crucial for assessing responsibility and remedy options. Additionally, compliance reports with industry standards such as ISO (International Organization for Standardization) outlining expected specifications can serve as tangible evidence supporting the claim of material faults, thus reinforcing the argument for corrective action and potential reimbursements.
Specific request for resolution or action steps
Faulty materials can lead to production delays and increased costs for manufacturers. For instance, in the automotive industry, defective parts like brake pads or engine components can result in safety hazards and recalls. Companies often implement quality control measures (ISO 9001 standards) to identify issues early. In such cases, a specific request for resolution may involve replacement orders from suppliers, detailed investigations into manufacturing processes, and corrective action plans to prevent recurrence. Effective communication of these issues also maintains customer trust and satisfaction in global markets.
Comments