Returning construction materials can sometimes feel like a hassle, but with the right approach, it doesnât have to be! Whether you overestimated your needs or simply faced a change in your project plans, knowing how to craft a concise return letter can streamline the process. In this article, weâll guide you through creating a professional letter that communicates your request clearly, ensuring you get your materials returned without any roadblocks. Ready to learn how to write an effective return letter? Letâs dive in!
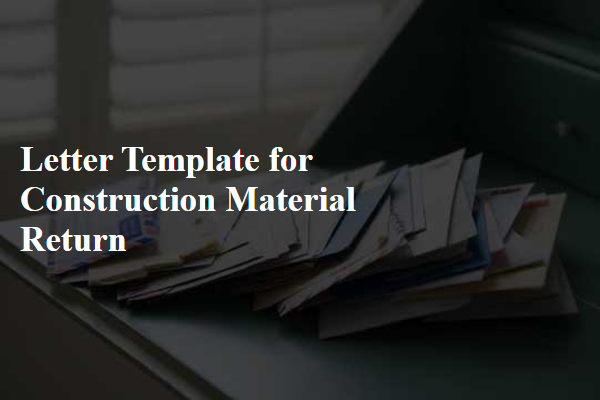
Header and Company Information
Construction material returns often require specific documentation to ensure proper accounting and inventory management. Key details typically include the name of the construction company, which may be XYZ Construction, and contact information such as the main office located at 123 Builder Street, Construction City, State, ZIP Code. The date of the return request, for example, January 10, 2023, is crucial for record-keeping. Additionally, a reference or invoice number related to the original purchase, such as INV-78910, aids in tracking the materials being returned. It is also important to specify the materials being returned, for instance, 50 bags of cement, along with the reasons for the return, which could include excess inventory or defective materials.
Detailed Description of Returned Items
Construction material returns often include various items such as concrete bags, lumber, steel beams, insulation rolls, and tiles. These materials can vary in size, weight, brand, and condition. A typical scenario could involve returning unused cement bags (30 kg each) from a local supplier, like XYZ Construction Supplies, due to overestimation of project requirements. Additionally, it might include four 2x4 wooden planks (length 8 feet), which were not utilized because of a change in design specifications on-site. Furthermore, high-grade insulation rolls (value per roll $50) intended for installation in attics may be returned due to incorrect shipment of thickness. Accurate documentation of such returns is essential for inventory management and financial reconciliation, including current market rates and supplier policies.
Reason for Return
Construction material returns often arise due to reasons such as over-ordering, incorrect specifications, and damage during transportation. For instance, a contractor might order 100 sheets of drywall (approximately 4 x 8 feet each) for a residential remodeling project. If the project scope changes, leading to the need for only 70 sheets, the excess materials need to be returned. Additionally, materials like cement bags (usually weighing 94 pounds each) may arrive damaged, with visible tears or moisture exposure, rendering them unsuitable for use. Properly documenting these reasons helps suppliers understand the return's context and facilitates efficient processing.
Return Authorization and Documentation
Construction material returns require specific documentation for authorization. A Return Authorization Number (RAN) must be clearly indicated on all documents. Essential items include original purchase receipts, which display item details, quantities, prices, and dates of purchase. Condition reports should describe the state of returned materials, including packaging and any damages. Photographic evidence may support the condition reports, illustrating the materials' status upon return. Each item must be labeled with SKU numbers or product codes for efficient processing. The return must be sent to the designated facility, often located at specific addresses provided by suppliers, adhering to timelines, usually within 30 days of delivery.
Closing with Contact Information
Construction material returns require careful attention to detail to ensure proper processing. Include essential details such as the invoice number (associated with the purchase), the specific materials being returned (like concrete mix or steel beams), and their quantity. It's vital to provide a reason for the return, whether it's due to excess inventory or damaged goods upon delivery. Additionally, a return authorization number from the supplier may be necessary for tracking purposes. Conclude the communication efficiently with contact information, ensuring to include phone numbers and email addresses for quick responses, allowing for smooth coordination during the return process.
Letter Template For Construction Material Return Samples
Letter template of inquiry regarding the return policy for construction materials.
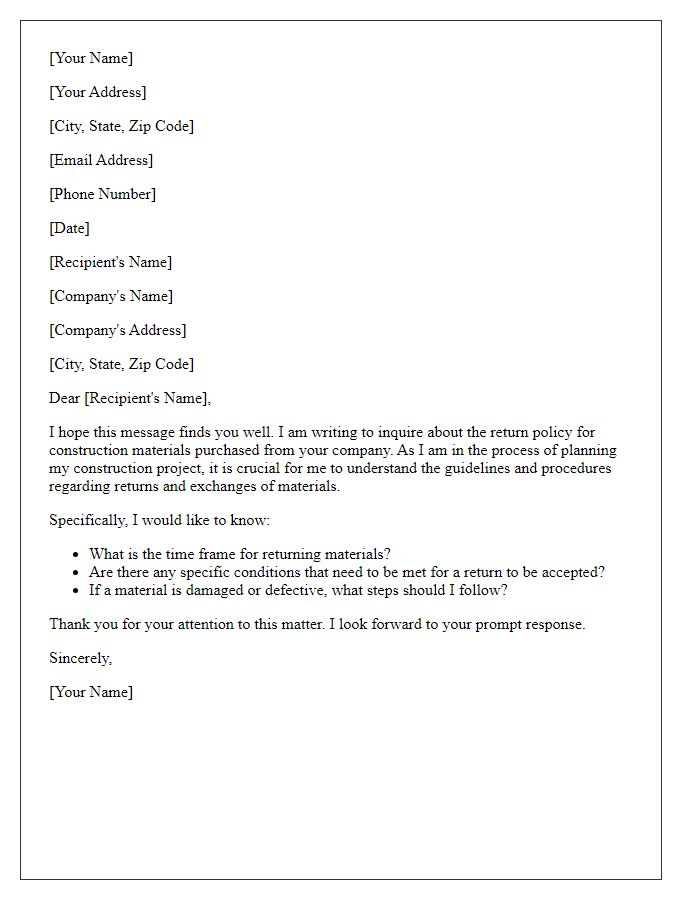
Letter template of notification for the return of defective building materials.
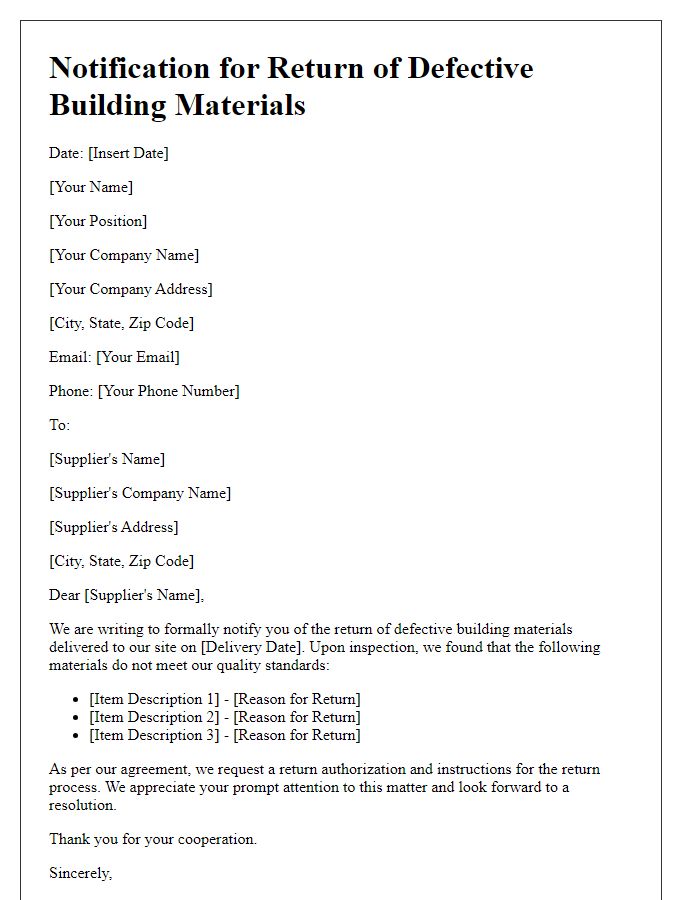
Letter template of documentation for the return of excess construction materials.
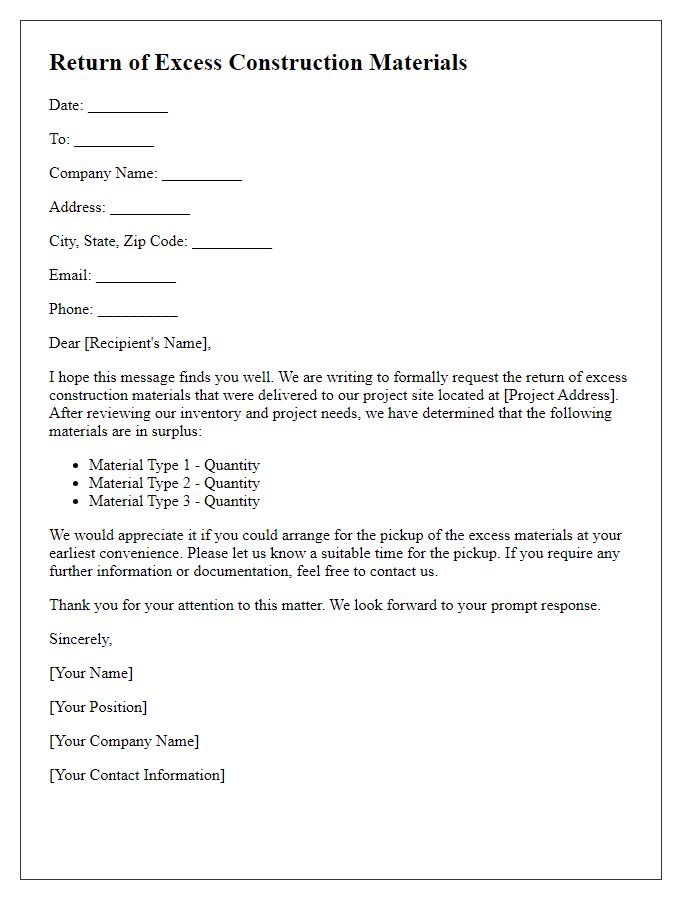
Comments