When it comes to construction projects, ensuring quality is not just an optionâit's a necessity. From the initial blueprint to the final inspection, every step must be meticulously monitored to guarantee that the outcome meets both safety standards and client expectations. With our quality assurance letter template, you can effectively communicate your commitment to excellence in every phase of your construction work. Ready to elevate your project standards? Letâs dive in and explore how to make your construction quality assurance process seamless and effective!
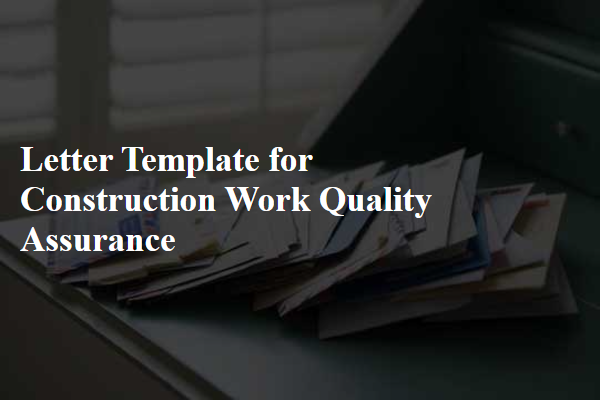
Company Information
Construction quality assurance emphasizes adherence to standards for materials, techniques, and safety procedures during the development of structures. Key entities include national building codes, local regulations, and industry best practices, often stemming from organizations such as the American Society for Testing and Materials (ASTM). Effective quality assurance processes involve regular site inspections, comprehensive documentation, and rigorous testing of materials like concrete and steel to ensure compliance with specified strength parameters. Project management plans must incorporate quality control checkpoints (e.g., before critical phases like concrete pouring) to maintain construction integrity while minimizing delays. This systematic approach ensures durability and safety for future occupants and aligns with the overall project budget and timeline.
Project Details
Quality assurance in construction projects, such as residential buildings or commercial complexes, plays a crucial role in ensuring structural integrity and adherence to safety regulations. During the project's lifecycle, specific quality benchmarks (such as ISO 9001 standards) need to be established. Inspections, which may occur weekly or bi-weekly, are vital to evaluate compliance with the design specifications and materials used, including concrete grades and reinforcement standards. Additionally, documentation detailing any non-conformance issues, along with corrective actions, facilitates transparency and accountability among contractors, subcontractors, and suppliers. This systematic approach ultimately minimizes defects and enhances the life span of the construction work being executed.
Quality Standards Compliance
Quality standards compliance in construction work ensures that materials, processes, and end results meet established guidelines and regulations. For instance, structural integrity inspection (such as compliance with AISC - American Institute of Steel Construction standards) plays a crucial role in assessing the strength of steel elements. Concrete testing (including methods like compressive strength tests as per ASTM C39) guarantees that poured concrete achieves necessary durability. Quality assurance methodologies, such as ISO 9001 implementation, focus on systematic processes to monitor and improve practices continuously. Additionally, adherence to local building codes, such as those defined by the International Building Code (IBC), safeguards public safety while ensuring that projects are completed on time and within budget. Documentation of quality checks, including daily reports and logs, serves as critical evidence for compliance and accountability throughout the construction phase.
Inspection and Testing Procedures
Inspection and testing procedures are critical components of quality assurance in the construction industry, ensuring that all materials, structural elements, and installations comply with project specifications and regulatory standards. In accordance with relevant building codes (such as the International Building Code, IBC) and industry best practices, rigorous testing methods should be employed, including concrete slump tests (to assess workability), ultrasonic testing (to evaluate weld integrity), and moisture content analysis for wood (to prevent decay). Established inspection schedules should be adhered to, covering key phases such as foundation pouring, framing, and finishing work. Documentation of all inspections, including detailed reports and test results, must be maintained for accountability and future reference, contributing to the overall safety and durability of the completed structure.
Contact Information for Queries
Quality assurance in construction work is critical for ensuring compliance with industry standards and safety regulations. Following the construction quality assurance plans (CQAP), project managers and stakeholders must maintain open channels for communication. Contact information for queries is essential for addressing any concerns regarding construction methods, materials, or compliance with local building codes. This information may include dedicated email addresses such as qa@constructioncompany.com, direct phone lines like (555) 123-4567, and contact hours from 9 AM to 5 PM, Monday through Friday. Effective communication fosters collaboration between on-site teams, quality inspectors, and contractors, ensuring a high standard of workmanship throughout the project lifecycle.
Comments