Navigating the complexities of supply chain management can sometimes feel like walking a tightrope, especially when unexpected disruptions occur. Recently, weâve encountered challenges that may impact our usual efficient delivery timelines, and we want to keep you in the loop every step of the way. Open communication and transparency are vital during these times, which is why weâre reaching out to share important details about these developments. Join us as we explore what this means for you and how we plan to address the situation moving forward!
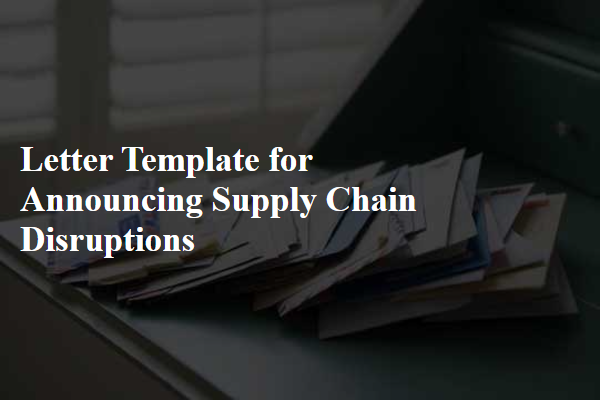
Clear subject line
Supply chain disruptions can significantly impact business operations and customer satisfaction. Recent events such as the ongoing global pandemic and geopolitical tensions have resulted in delays and shortages of essential materials. For instance, semiconductor shortages in the electronics industry have affected production timelines, while logistical challenges in shipping routes have extended delivery times for several key products. Companies are advised to communicate transparently with stakeholders, detailing specific affected products, estimated impact timelines, and alternative solutions. Timely updates can help manage expectations and maintain trust with customers during these challenging circumstances.
Explanation of disruption cause
Recent global supply chain disruptions have significantly impacted logistics and inventory management across various industries, particularly affected by the COVID-19 pandemic and geopolitical tensions. These disruptions, originating from widespread factory shutdowns in key manufacturing hubs like China and logistics bottlenecks at major ports like Los Angeles and Long Beach, have resulted in delayed shipments and increased shipping costs, with container freight rates skyrocketing by over 350% since 2020. Additionally, labor shortages in transportation sectors have compounded issues, leading to longer delivery times and scarcity of essential components in technology and automotive sectors. Companies are now facing challenges in meeting consumer demand while navigating increased lead times, often stretching to several months.
Expected impact duration
Recent events, such as global shipping delays due to the COVID-19 pandemic and continued geopolitical tensions, have significantly disrupted supply chains worldwide. Companies like Maersk and Evergreen are experiencing unprecedented delays, with shipping container transit times increasing by up to 50% compared to pre-2020 levels. Local suppliers, heavily reliant on imported raw materials, are facing shortages that could last for several months, particularly impacting sectors like electronics and automotive manufacturing. Estimates indicate that these disruptions may persist until early 2024, which could severely affect product availability and pricing. Companies are advised to reassess inventory strategies and communicate transparently with customers regarding potential delays.
Mitigation measures
Supply chain disruptions experienced recently can significantly impact delivery schedules for various products across industries, including electronics and automotive sectors. Global events such as the COVID-19 pandemic, geopolitical tensions in regions like Eastern Europe, and extreme weather conditions have created logistic delays and shortages. In response, companies implement mitigation measures, such as diversifying suppliers to secure alternative sources, increasing inventory levels to withstand shortages, and utilizing advanced analytics for better demand forecasting. Enhanced communication with stakeholders, including suppliers and customers, becomes crucial for managing expectations and ensuring transparency. Additionally, investing in technology improvements like automated tracking systems can streamline operations and reduce the impact of future disruptions.
Contact information for inquiries
Supply chain disruptions present significant challenges for businesses across various sectors. Factors such as global shipping delays, increased demand for raw materials, and geopolitical tensions (e.g., ongoing trade disputes) can severely impact inventory levels and lead to delays in product availability. Companies may face challenges like increased costs (up by 30% in recent months) and extended lead times (averaging several weeks longer than anticipated). Customers affected by these interruptions may experience frustration and uncertainty, leading to a potential decline in customer satisfaction and loyalty. For inquiries regarding these supply chain issues, businesses typically provide dedicated contact information, ensuring timely communication with relevant stakeholders.
Comments