In todayâs fast-paced business environment, effective vendor capacity planning is essential for maintaining a competitive edge. Collaborating with our vendors can lead to streamlined operations and enhanced productivity, ultimately benefiting all parties involved. By sharing insights and aligning our goals, we can better anticipate demand fluctuations and ensure timely delivery of products. Interested in learning how we can optimize our vendor relationships together? Read on for more insights!
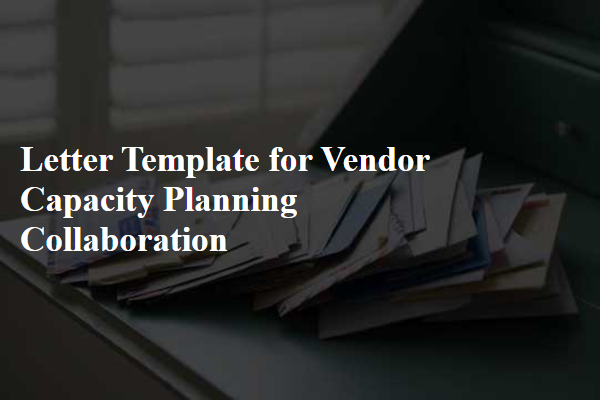
Clear objectives and goals
Effective vendor capacity planning is essential for optimizing supply chain efficiency and meeting demand forecasts. Establishing clear objectives aids in coordination between vendors and stakeholders. Key goals include analyzing historical data, identifying peak demand periods, and aligning inventory levels. Utilizing tools like demand forecasting algorithms enhances accuracy. Regular communication and strategic meetings between vendors, held quarterly, foster collaboration and adaptability. Implementing performance metrics, such as on-time delivery rates and order accuracy percentages, ensures continuous improvement. Additionally, technology integration, such as Enterprise Resource Planning (ERP) systems, allows real-time data sharing, facilitating proactive decision-making.
Key performance indicators (KPIs)
Effective vendor capacity planning collaboration requires a clear identification of key performance indicators (KPIs) to ensure optimal supply chain efficiency. KPIs such as order fulfillment rate (measured as a percentage of orders delivered on time and in full) play a critical role in assessing vendor reliability. Cycle time, including the average time taken from order placement to delivery, provides insight into operational efficiency. Additionally, inventory turnover ratio, which gauges how many times inventory is sold and replaced over a specific period, is crucial for analyzing stock management effectiveness. Quality defect rates, expressed as a percentage of products returned due to defects, highlight areas for improvement in product quality and vendor selection. Overall, regular monitoring and assessment of these KPIs enable informed decision-making and strategic improvements in collaboration.
Resource allocation and scheduling
Effective vendor capacity planning requires meticulous resource allocation and scheduling. Accurate forecasting models enable efficiency, ensuring that supplies meet demands without overstocking. Key metrics such as lead times (time taken between order placement and delivery) must be examined alongside historical sales data to anticipate peak periods, such as holiday seasons. Robust communication with vendors, using platforms like Vendor Management Systems (VMS), ensures that adjustments to capacity can be made promptly, optimizing fulfillment rates. Regular reviews and updates of capacity plans are essential to adapt to fluctuations in market conditions, while real-time analytics can enhance decision-making processes.
Communication and reporting structure
Effective vendor capacity planning requires a clear communication and reporting structure to ensure a seamless flow of information. Vendors, such as manufacturers and suppliers, need to provide regular updates regarding their production capabilities, lead times, and inventory levels. Annual forecasts, typically submitted in January, outline expected volumes and any seasonal fluctuations (e.g., holiday peaks). Weekly reports on production schedules help identify potential bottlenecks early, while monthly capacity reviews assess long-term alignment with demand projections. Establishing dedicated points of contact, including roles such as procurement managers and operations analysts, facilitates prompt issue resolution. Implementing a centralized dashboard can enhance visibility, allowing stakeholders to track capacity utilization in real time and make informed decisions based on accurate data.
Risk management and contingency plans
Vendor capacity planning is crucial for managing supply chain stability, especially in dynamic markets. Implementing risk management strategies ensures preparedness against unforeseen disruptions, such as natural disasters or global pandemics, affecting operations. Contingency plans, including alternative sourcing options, inventory management strategies, and communication protocols, allow businesses to respond effectively to potential risks. Regular assessments of vendor performance and capacity metrics, such as lead times and production capabilities, enhance visibility and inform decision-making. Collaboration with vendors fosters a proactive approach to capacity planning, enabling effective resource allocation. Additionally, maintaining a diverse supplier base minimizes dependency risks, ensuring resilience in various market conditions.
Letter Template For Vendor Capacity Planning Collaboration Samples
Letter template of vendor capacity planning for strategic partnership discussions
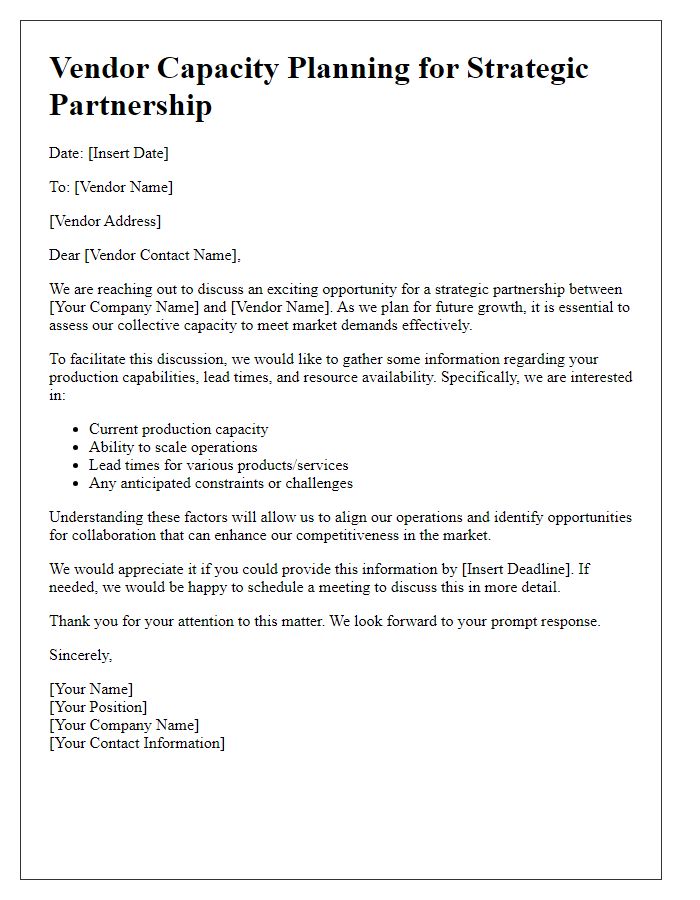
Letter template of vendor capacity planning for quarterly review meetings
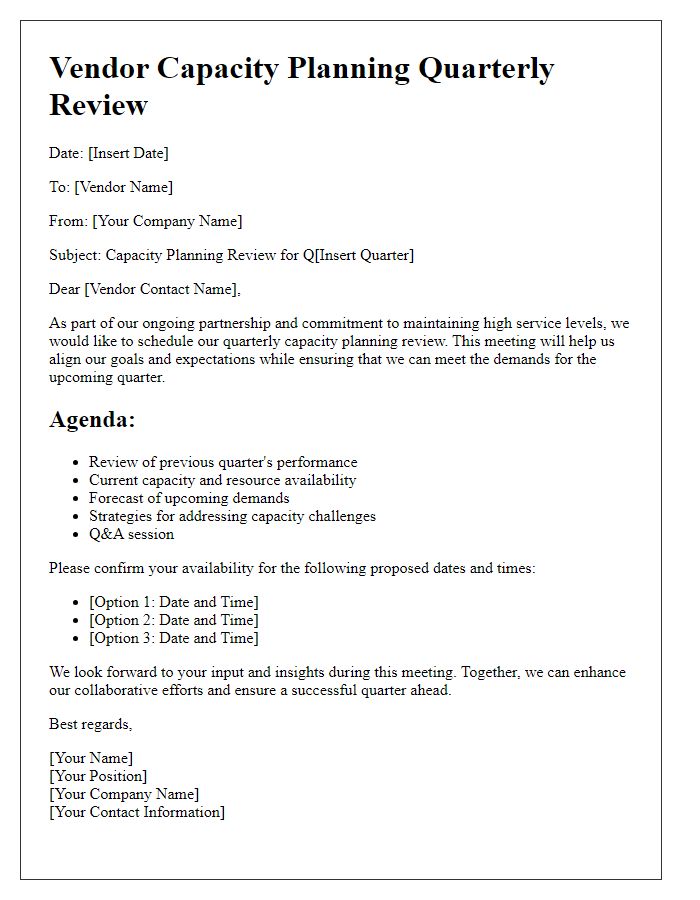
Letter template of vendor capacity planning for resource allocation assessments
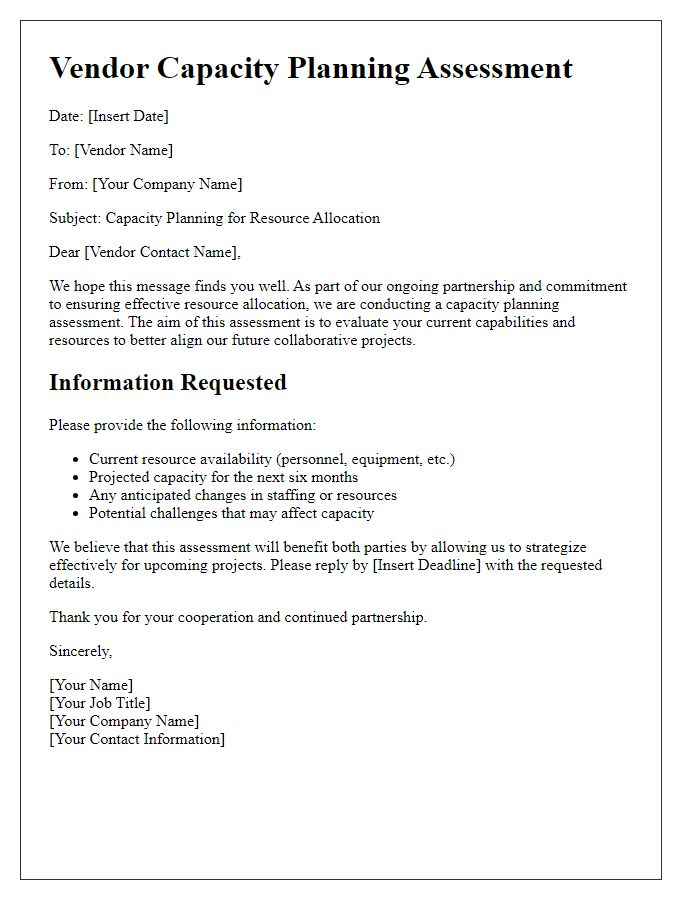
Letter template of vendor capacity planning for identifying supply chain efficiencies
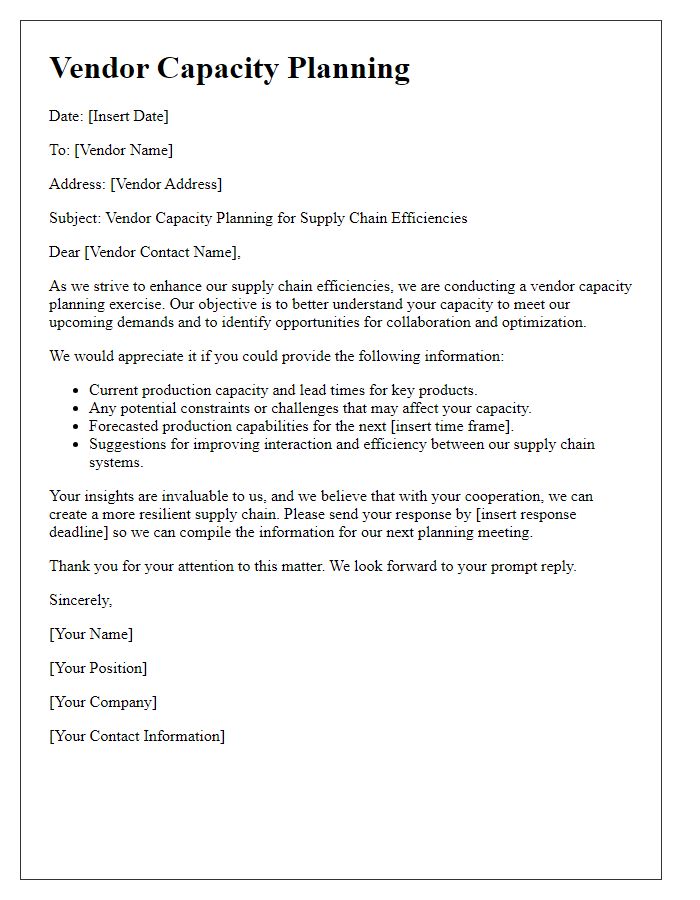
Letter template of vendor capacity planning for demand forecasting alignment
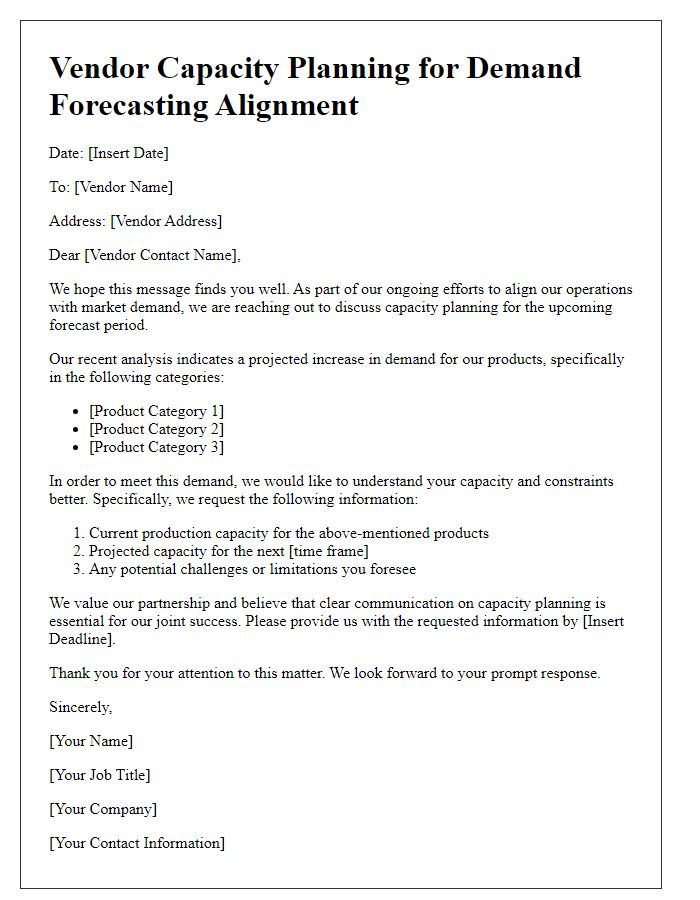
Letter template of vendor capacity planning for performance evaluation feedback
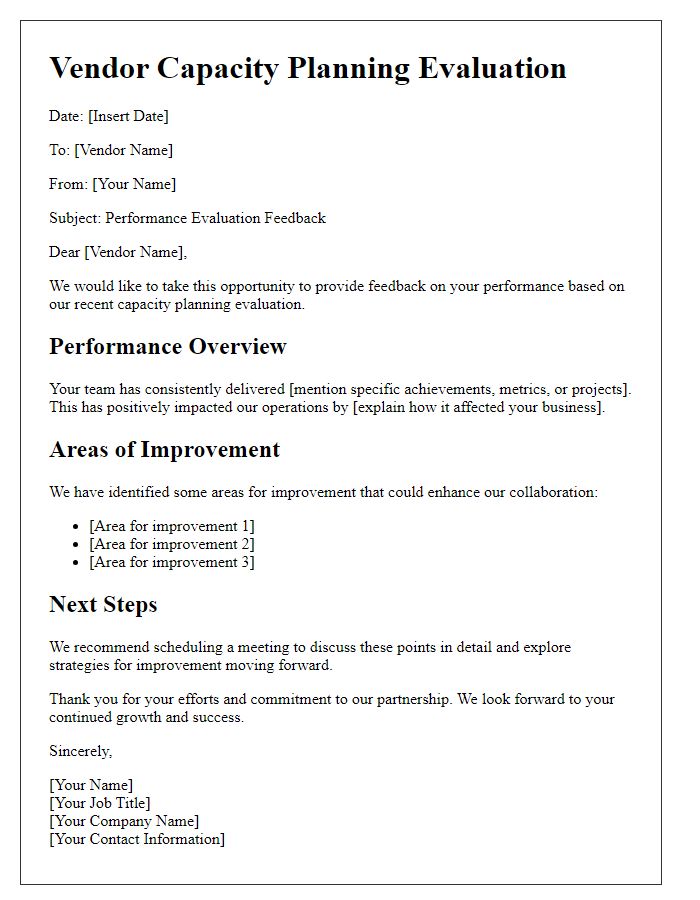
Letter template of vendor capacity planning for contract negotiation preparation
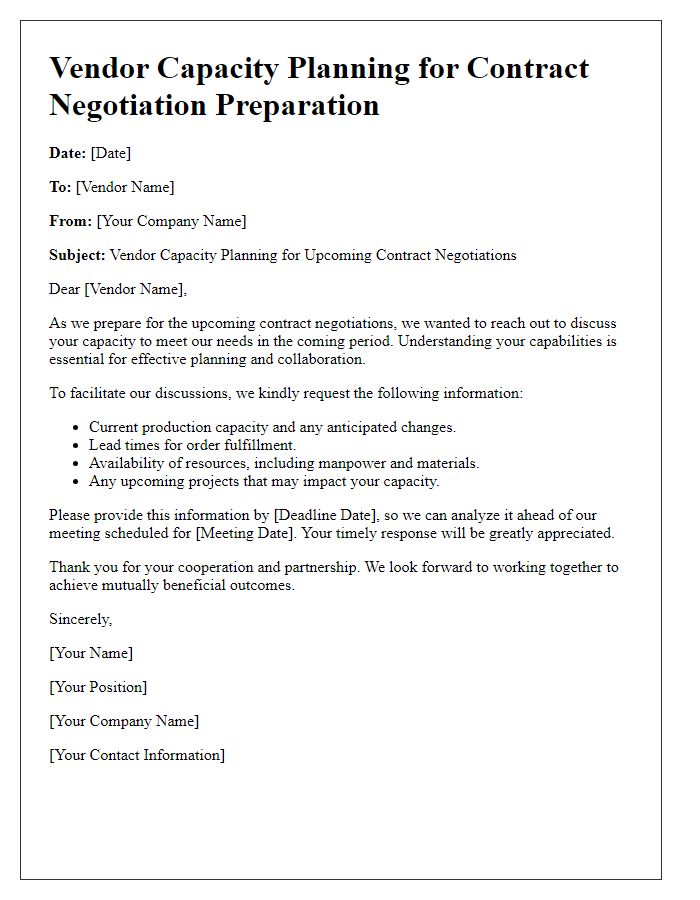
Letter template of vendor capacity planning for risk management strategies

Letter template of vendor capacity planning for integration of technology solutions

Comments