Are you looking to enhance your inventory management and streamline your transportation operations? Our latest article dives into effective strategies for stock replenishment that can transform the way you handle logistics. From optimizing routes to implementing just-in-time delivery systems, we've got you covered with practical insights. So, buckle up and read on to discover how to elevate your transportation service!
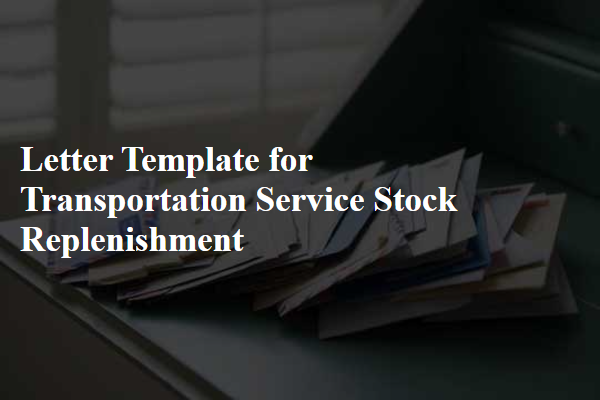
Specific Item Details
Transportation service stock replenishment requires precise item details to ensure timely availability. Inventory items include various types of vehicles, such as cargo trucks, which typically have a payload capacity ranging from 3,000 to 55,000 pounds depending on model specifications. Essential supplies also comprise fuel types, including diesel with an octane rating of 87 and gasoline with higher variations, needed weekly per vehicle type. Maintenance tools, including hydraulic jacks and wrenches organized in kits, should be replenished regularly to maintain operational efficiency. Safety equipment such as reflective vests, hard hats, and first-aid kits must meet OSHA regulations and be restocked quarterly to ensure compliance and worker safety. Adherence to local regulations for transportation logistics is vital for seamless operations.
Quantity Required
Transportation service stock replenishment requires precise inventory management. A detailed analysis of item quantities is essential to ensure efficient logistics operations. For instance, the replenishment of 150 units of high-demand items, such as fuel additives and tire replacement kits, is necessary to maintain service quality. Accurate tracking of stock levels can prevent shortages that disrupt essential transportation services, especially in regions with busy freight routes, like Los Angeles and Chicago. Efficient supply chain practices must be employed to facilitate timely replenishment, ensuring that all transportation services remain operational without delays or interruptions.
Delivery Timeline
Transportation service stock replenishment requires careful planning to ensure timely delivery of goods to warehouses or retail locations. The expected delivery timeline typically spans from 24 to 72 hours following order confirmation, depending on distance (measured in miles) and logistics infrastructure (including highways or rail systems). The process involves coordinating with trucking companies or freight carriers (such as FedEx or UPS) and tracking shipments using software solutions that provide real-time updates. Efficient handling at distribution centers (like Amazon's Fulfillment Centers) can further optimize delivery speed and accuracy. It is crucial to also account for potential delays caused by weather conditions (like snowstorms or heavy rain) or road traffic incidents, which can impact overall efficiency.
Contact Information
Transportation service stock replenishment relies heavily on accurate contact information to facilitate efficient operations. Maintaining up-to-date contact details (such as phone numbers and email addresses) for suppliers and logistics partners ensures timely communication. Accurate data entry into inventory management systems allows for quick identification of stock levels, ensuring that critical items such as fuel, maintenance supplies, and spare parts are reordered promptly. Regular audits (conducted quarterly) of contact lists prevent delays due to miscommunication. Efficient transportation operations (including freight logistics) depend on seamless coordination among all parties involved, enabling rapid response to stock shortages, thereby minimizing operational downtime and maximizing productivity.
Payment Terms
Transportation service stock replenishment involves critical logistics management, ensuring that inventory levels meet demand efficiently. Payment terms define the conditions under which transactions occur, often specifying a payment window of 30 to 60 days for services rendered. Companies, such as FedEx and UPS, may implement varying payment models based on client needs, whether net payment, advance payments, or phased payments depending on shipment size and urgency. Clear understanding of these payment terms (contractually binding agreements) enhances relationships between suppliers and clients, fostering timely service without inventory shortages. Maintaining accurate documentation (invoices, receipts) is vital for tracking financial obligations and ensuring compliance with agreed-upon terms.
Comments