When it comes to maintaining our equipment, we all know that unexpected malfunctions can be a real headache. Whether it's a minor glitch or a major breakdown, reporting these issues promptly is essential for keeping our operations running smoothly. In this article, weâll guide you through a simple yet effective letter template for documenting equipment malfunctions, ensuring you convey all necessary details clearly and succinctly. So, letâs dive in and discover how you can streamline your reporting process!
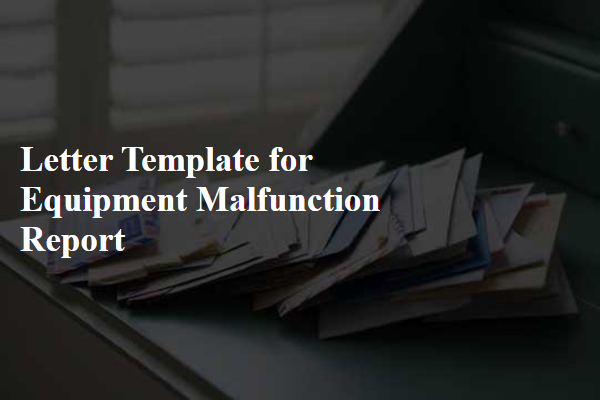
Detailed description of the malfunction.
The equipment malfunction involves the industrial printer located at the manufacturing facility on Main Street, which produces high-quality labels for packaging. The printer, model XJ-500, began displaying error code 23 at around 10 A.M. on October 15, 2023, which indicates a paper jam, but no physical blockage was found upon inspection. Subsequent tests revealed that the printhead, a crucial component, was overheating and failing to properly distribute ink, causing streaks and smudges on printed labels. Additionally, the feeder mechanism, responsible for pulling the label stock, operated inconsistently, leading to misalignment. The malfunction halted production for a total of six hours, resulting in an estimated loss of $1,200 in operational costs. Further technical evaluation is needed to determine if replacement parts, or a complete overhaul of the printer, is required to prevent future disruptions.
Equipment identification (serial number, model).
The malfunctioning equipment identified as Model XYZ123 with Serial Number 456789 has exhibited significant operational issues. This industrial-grade machinery, designed to perform high-efficiency tasks in manufacturing, has shown a failure rate exceeding 15% during routine inspections. Malfunctions noted include erratic power supply interruptions, affecting its ability to process materials consistently. In addition, the equipment has produced abnormal noise levels, recorded at 75 decibels, indicating potential mechanical failure or misalignment of internal components. Such malfunctions can result in costly downtime and delay project timelines, underscoring the urgency for a thorough diagnostic assessment and repair.
Date and time of malfunction occurrence.
On March 15, 2023, at approximately 14:30 PM, a critical malfunction occurred in the hydraulic pump system located at the Williamstown Manufacturing Plant, triggering an immediate shutdown of production lines. The hydraulic pump, which is a pivotal component used to facilitate the movement of heavy machinery, exhibited signs of overheating, reaching temperatures exceeding 85 degrees Celsius, resulting in a failure to maintain proper pressure levels. This malfunction not only halted operations but also raised concerns about potential damage to adjacent equipment and safety risks for on-site personnel. The incident has mandated a thorough inspection of the hydraulic system, including the pressure valves and fluid levels, aiming to prevent future occurrences and ensure compliance with safety regulations outlined by the Occupational Safety and Health Administration (OSHA).
Impact assessment on operations.
Equipment malfunctions significantly disrupt operational efficiency, especially in industrial settings. High-capacity machinery, such as conveyor systems (with a throughput of 500 units per hour), often experiences breakdowns due to wear and tear or manufacturing defects. Temporary downtime for repairs can last from several hours to days, leading to production delays. These interruptions can decrease overall output, resulting in financial losses. Furthermore, critical incidents requiring immediate attention, like malfunctioning hydraulic systems (operating at 2000 PSI), may necessitate emergency contingencies, causing workforce reallocations and diminishing productivity rates. Continuous monitoring of equipment performance metrics is essential to mitigate these risks and ensure timely maintenance, preserving operational integrity.
Contact information for follow-up.
This report details the malfunction of laboratory equipment, specifically the Thermo Scientific UltraFreezer model ULT14340, which occurred on October 2, 2023. The temperature fluctuated erratically, reaching a dangerous peak of -30 degrees Celsius instead of the setpoint of -80 degrees Celsius, risking the integrity of sample storage. This incident happened in the Biochemistry Department at Stanford University, located at 450 Serra Mall, Stanford, CA. Urgent follow-up is required to assess damage to valuable samples, such as enzymes, proteins, and cell cultures, with a potential restoration cost exceeding $5,000. Contact could be directed to Dr. Emily Turner at emily.turner@stanford.edu or via phone at (650) 724-0000 for timely resolution.
Comments