Are you navigating the complex world of health and safety compliance? Writing a clear and concise letter can help ensure that all necessary protocols are effectively communicated and understood. Whether it's addressing concerns, providing updates, or outlining procedures, a well-crafted letter plays a crucial role in maintaining a safe environment for everyone. Dive into our comprehensive guide for tips and templates that will simplify your compliance communicationâread more to get started!
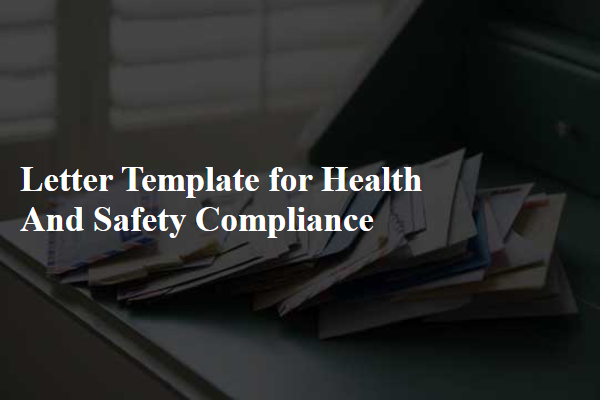
Specific health and safety regulations
Health and safety regulations are critical frameworks designed to protect employees in various work environments, such as construction sites, factories, and offices, in compliance with legislation like the Occupational Safety and Health Act (OSHA) established in 1970. These regulations encompass specific requirements, such as providing personal protective equipment (PPE) like helmets or gloves, conducting regular risk assessments, and ensuring proper training on emergency protocols. Failure to adhere to these regulations can result in significant consequences, including fines reaching thousands of dollars or even legal actions against organizations. Moreover, maintaining a safe workplace fosters employee morale and productivity, creating a culture of safety that benefits both workers and employers. Regular audits and inspections, often mandated bi-annually or annually, ensure compliance and identify potential hazards, ensuring a proactive approach to workplace safety.
Company policy and procedures
Health and safety compliance is essential for maintaining a safe working environment in organizations, such as manufacturing plants and office buildings. Company policy outlines regulations that ensure the well-being of employees, including guidelines for emergency procedures, personal protective equipment (PPE) usage, and risk assessment protocols. Procedures may vary based on industry specifics, with regular training sessions scheduled quarterly to educate staff on health hazards, safe practices, and incident reporting. For example, in construction sites, strict adherence to scaffolding regulations and the use of hard hats reduces the likelihood of accidents. Additionally, incorporating ergonomic assessments in office environments helps lower repetitive strain injuries among employees, promoting overall workplace health and productivity. Regular audits and inspections by certified safety officers, conducted annually, ensure compliance with Occupational Safety and Health Administration (OSHA) standards, fostering a culture of safety within the organization.
Risk assessment and management
Effective health and safety compliance requires meticulous risk assessment and management practices within workplace environments. Organizations must identify potential hazards, including physical (e.g., machinery, tools), chemical (e.g., solvents, dust), biological (e.g., viruses, bacteria), and ergonomic risks (e.g., repetitive strain), assessing their likelihood and potential impact on employee well-being. Risk matrices can be employed, categorizing risks into low, medium, or high levels, guiding mitigation strategies tailored to specific situations. Documentation, such as the Health and Safety Executive (HSE) guidelines in the UK or OSHA standards in the USA, must be referenced to ensure compliance with legal requirements. Regular training sessions, with an emphasis on emergency procedures and reporting protocols, reinforce a culture of safety across all operational levels. Monitoring and reviewing risk management practices ensure dynamic adaptability to evolving risks, ultimately protecting the workforce and maintaining organizational integrity.
Training and awareness programs
Health and safety compliance training programs, crucial for workplace safety, encompass guidelines set by organizations like OSHA (Occupational Safety and Health Administration) in the United States. These programs often include sessions that educate employees about potential hazards specific to their roles, such as chemical exposure in manufacturing plants or ergonomic risks in office environments. Training typically involves hands-on demonstrations, interactive workshops, and assessments to gauge understanding. Regular updates and refresher courses promote long-term awareness and adaptation to new regulations or safety equipment, ensuring a proactive approach to workplace safety. Additionally, fostering a culture of safety where employees feel empowered to report safety concerns significantly enhances overall compliance.
Emergency contact and reporting procedures
In compliance with health and safety regulations, emergency contact procedures must be clearly established. All employees should have access to the emergency contact list, which includes telephone numbers for local emergency services (such as 911 in the United States), internal safety officers, and facility management. Reporting procedures require immediate notification to a designated health and safety officer or supervisor upon witnessing an incident or hazard. It is essential to document the event using an incident report form, capturing critical details such as date, time, location (specific building or area within the facility), nature of the incident, and individuals involved. Regular training sessions should be conducted to ensure all staff understand these procedures, bolstering workplace safety and compliance with Occupational Safety and Health Administration (OSHA) standards.
Comments