As we approach the end of the year, it's that time againâour annual inventory count! This crucial process not only helps us keep track of our stock but also ensures we're ready for the upcoming year with a clear vision of our resources. It's a collective effort that involves teamwork, attention to detail, and a little bit of planning. So, grab your notepad and join us as we dive into everything you need to know about our year-end inventory count!
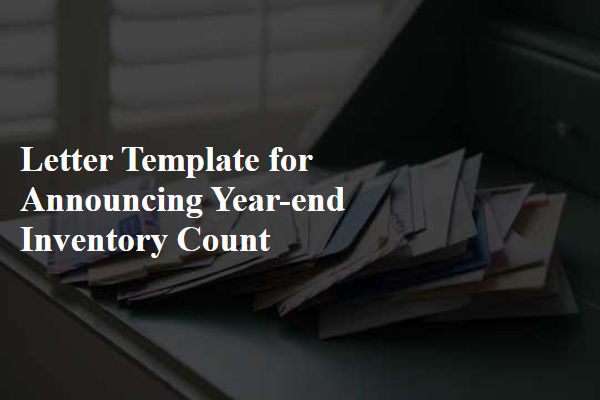
Clear Dates and Times
The year-end inventory count will take place on December 15, 2023, starting at 8:00 AM and concluding at 5:00 PM. This essential process, crucial for accurate stock assessment and financial reporting, will occur at our main warehouse located at 123 Business Park Road, Springfield. All employees involved in the count should report to the warehouse by 7:30 AM for briefing and assignment of duties. Accurate inventory records, including SKU numbers and quantities, will be examined meticulously throughout the day to ensure complete and precise accounting. Participation in this event is mandatory, as the count significantly impacts year-end financial statements and operational planning for the upcoming year.
Purpose of Inventory Count
The year-end inventory count serves a crucial purpose in maintaining accurate financial records for businesses, ensuring the integrity of asset management. This systematic process involves physically counting all inventory items, including raw materials, work-in-progress, and finished goods, at the end of the fiscal year, typically December 31st. The count aids in reconciling discrepancies between recorded inventory levels and actual stock on hand, which can occur due to theft, damages, or mismanagement. A comprehensive inventory count provides essential data that helps inform financial statements, assists in tax preparation, and supports strategic decision-making for future operations. Maintaining an accurate inventory count enables businesses to optimize supply chain efficiency, reduce costs, and enhance overall profitability.
Impact on Operations
As a crucial annual procedure, the year-end inventory count for 2023 is scheduled to take place from December 1st to December 10th across all distribution centers, including the main warehouse in Chicago, Illinois. This inventory assessment, essential for maintaining accurate financial records, will entail a comprehensive examination of stock levels, including over 25,000 SKUs (stock keeping units) and the evaluation of assets valued at approximately $5 million. Operations will be impacted significantly during this period, with daily shipping and receiving activities being temporarily suspended to allow for thorough counting and verification of all merchandise. Staff members from various departments, including logistics and finance, will collaborate closely to ensure minimal disruption and accurate reporting, while customers should expect delays in order fulfillment until inventory procedures are completed.
Employee Responsibilities
The year-end inventory count is a critical process for ensuring accurate financial reporting and efficient stock management at our facility. Each employee plays a vital role in this process, which occurs from December 15 to December 20 annually. All team members assigned to inventory tasks must familiarize themselves with the inventory management system and the specific items for which they are responsible. Accuracy is essential; employees should double-check quantities and item conditions, ensuring everything aligns with documented records. Additionally, maintaining organization in designated counting areas prevents confusion and errors. Communication with supervisors is crucial if discrepancies arise, facilitating timely resolutions. Participation in training sessions scheduled for December 10 will enhance understanding of procedures and expectations. Active engagement in the inventory count will contribute significantly to the company's overall success and operational efficiency.
Instructions for Reporting Discrepancies
The year-end inventory count is a crucial process for maintaining accurate financial records and evaluating stock levels at [Company Name], located in [City, State]. Employees must conduct a thorough physical count of all inventory items, including raw materials, work-in-progress, and finished goods, during the scheduled inventory period from [Start Date] to [End Date]. To ensure accuracy, discrepancies between the physical count and recorded inventory must be reported immediately. This includes overages (surplus items) and shortages (missing items). Staff should document discrepancies using the Inventory Discrepancy Report form, located in [Designated Location]. All reports must be submitted to the inventory management team by [Submission Deadline] for analysis and reconciliation. Accurate inventory records contribute to financial health, ensuring compliance with accounting standards and proper tax reporting.
Comments