Hey there! In this update, we want to share the latest developments in our medication manufacturing process that are designed to enhance quality and efficiency. By incorporating state-of-the-art technology and rigorous quality controls, we're committed to ensuring that our products meet the highest standards of safety and effectiveness. Curious to learn more about how these changes could impact your experience with our medications? Keep reading for all the details!
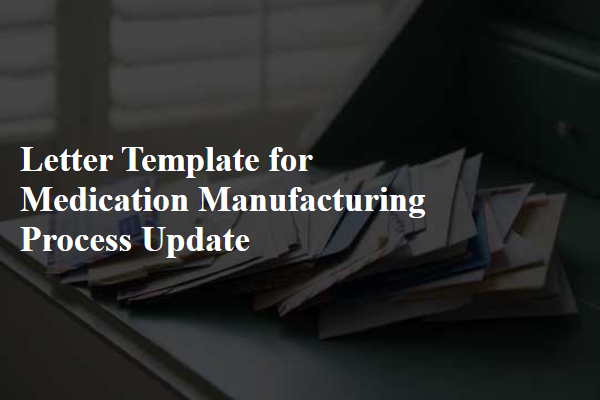
Regulatory Compliance
Updating the medication manufacturing process to ensure regulatory compliance involves multiple steps that align with the stringent guidelines set by health authorities such as the Food and Drug Administration (FDA) in the United States. Quality Assurance (QA) protocols must be reviewed and enhanced to adhere to current Good Manufacturing Practices (cGMP), including stringent documentation procedures and batch record keeping (which must detail raw material specifications and final product testing results). Equipment used in the manufacturing process must undergo rigorous validation processes, including Installation Qualification (IQ), Operational Qualification (OQ), and Performance Qualification (PQ) to ensure functionality and reliability. Training programs for personnel should be re-evaluated to include updates on compliance-related practices and safety protocols. All changes must be documented meticulously to facilitate inspections and audits, ensuring that the pharmaceutical plant or facility maintains the highest standards of safety and efficacy throughout the production cycle.
Supply Chain Management
In the dynamic landscape of pharmaceutical production, supply chain management plays a pivotal role in ensuring the timely availability of essential medications. The integration of advanced inventory systems allows for real-time tracking of raw materials like active pharmaceutical ingredients (APIs), ensuring compliance with quality standards set by regulatory agencies such as the FDA (Food and Drug Administration) in the United States. Recent updates to our supply chain protocols have included partnerships with trusted suppliers across critical regions, minimizing the risk of disruptions, particularly from global events such as pandemics or natural disasters. Furthermore, the implementation of lean manufacturing techniques has optimized production efficiency, significantly reducing lead times while maintaining stringent safety measures in factories located in highly regulated environments. Overall, continuous monitoring and improvement of our supply chain processes are critical to enhancing the accessibility of life-saving medications to patients worldwide.
Quality Assurance
Quality Assurance plays a crucial role in the medication manufacturing process, ensuring compliance with stringent industry standards set by organizations like the FDA (Food and Drug Administration) and EMA (European Medicines Agency). Every stage, from raw material sourcing to final product packaging, undergoes rigorous inspection and testing to maintain the integrity of pharmaceutical products. For example, batch sampling procedures must adhere to guidelines that specify minimum quantities based on the volume of production. Documented quality checks, including stability tests and sterility assessments, occur within controlled environments, such as Clean Room facilities that maintain specific ISO classifications. In addition, effective quality management systems, like GMP (Good Manufacturing Practices), are essential to track potential deviations and facilitate continuous improvement. Regular audits and compliance assessments are vital to uphold the high standards required for patient safety and product efficacy.
Production Efficiency
The production efficiency in the medication manufacturing process has seen significant advancements, especially in facilities like Pfizer's Kalamazoo, Michigan plant, where the implementation of automation technology has streamlined operations. Recent data indicates a 25% increase in output capacity due to the integration of robotic systems, which minimize human error and enhance consistency in drug formulation. Additionally, real-time monitoring systems have improved resource allocation, ensuring optimal use of raw materials, such as active pharmaceutical ingredients (APIs) sourced from global suppliers. Furthermore, adherence to Good Manufacturing Practices (GMP), enforced by the Food and Drug Administration (FDA), has resulted in a reduction of production downtime by approximately 15%, allowing faster time-to-market for critical medications. Continuous training programs for staff further support these efficiency gains, fostering a culture of excellence in production lines across multiple locations.
Technological Advancements
The recent technological advancements in the medication manufacturing process, particularly in large-scale operations, have significantly improved efficiency and quality. Innovations such as the implementation of continuous manufacturing systems, exemplified by companies like Pfizer and Johnson & Johnson, allow for a seamless flow of materials and reduce production time by up to 50%. Advanced robotics and automated systems in facilities located in regions like the Pharmaceutical Corridor in North Carolina enhance precision and minimize human error, contributing to a more consistent product output. Additionally, integration of artificial intelligence (AI) for predictive analytics can streamline quality control processes, ensuring that each batch meets stringent regulatory standards set by the FDA, leading to a safer end product for consumers. This evolution not only optimizes resource allocation but also aligns with global initiatives to improve sustainability within the pharmaceutical sector.
Letter Template For Medication Manufacturing Process Update Samples
Letter template of medication production process improvement notification
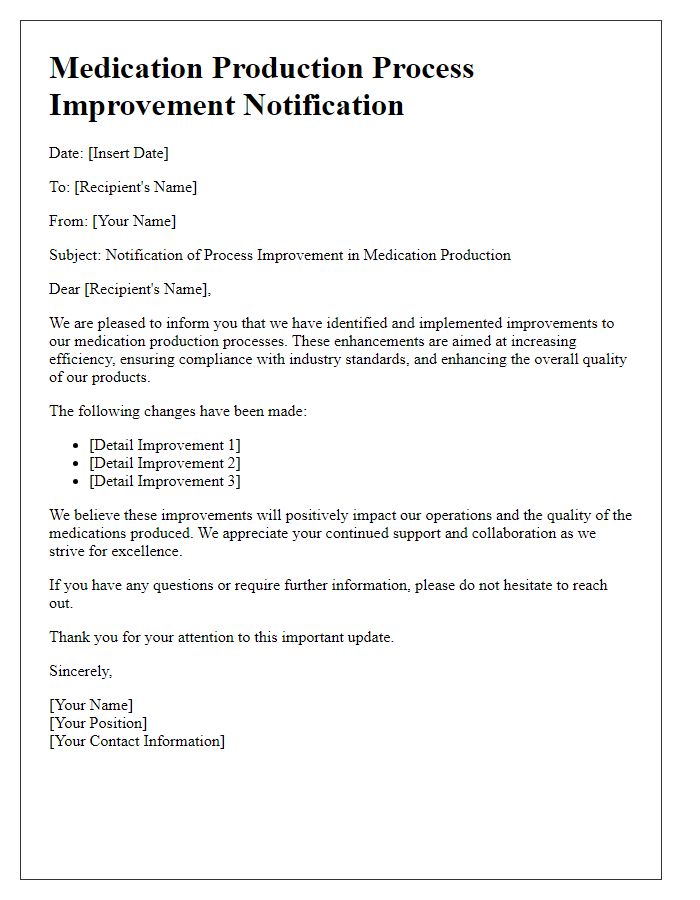
Letter template of enhancements in pharmaceutical manufacturing procedures
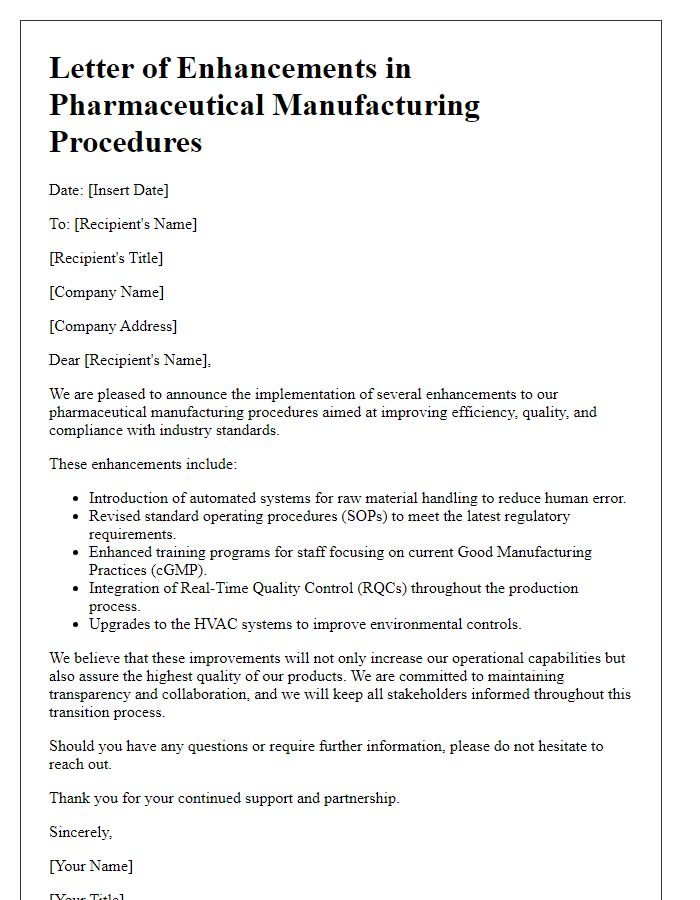
Comments