Have you ever found yourself surprised by unscheduled maintenance work that disrupted your day? It can be quite inconvenient when unexpected repairs arise, especially in a busy environment. Understanding the importance of clear communication during these times can help alleviate frustration and keep everyone informed. Join me as we delve into effective letter templates that will not only help you notify your team but also streamline the entire maintenance process!
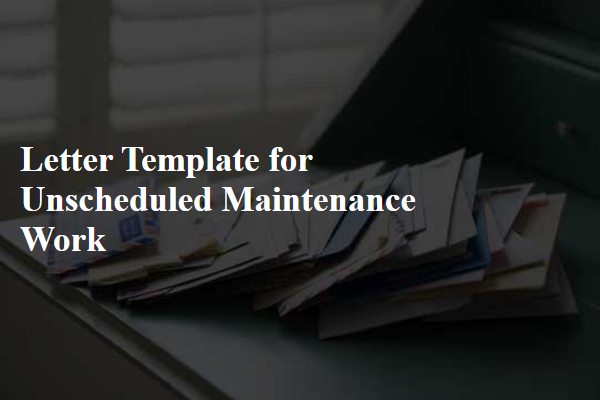
Clear subject line
Unscheduled Maintenance Notification: Immediate Action Required Equipment malfunctions can disrupt operations significantly. An unscheduled maintenance event has occurred, requiring immediate attention to the HVAC system at the corporate headquarters located at 123 Business Parkway. The malfunction was identified on October 15, 2023, leading to inconsistent temperature regulation, potentially affecting employee comfort and productivity. Maintenance teams have been dispatched to conduct urgent repairs, expected to last approximately four hours. Employees in affected areas (floors 1 to 3) should prepare for temporary relocation if work extends beyond the scheduled timeframe. Notification will follow on completion of repairs.
Brief introduction of the issue
Unscheduled maintenance work often arises unexpectedly due to equipment failure or safety concerns, necessitating immediate attention to mitigate potential hazards. For example, a malfunctioning HVAC system can lead to uncomfortable indoor temperatures, impacting employee productivity and health in corporate offices like those located in New York City. Additionally, critical machinery breakdowns in manufacturing facilities, particularly those utilizing conveyor belts for high-speed assembly lines, can halt operations, causing significant financial losses. Essential parts or components failing, such as motors or circuit boards, require urgent repairs to ensure operational continuity and uphold safety standards.
Detailed explanation of maintenance reasons
Mechanical failures in industrial machinery, such as conveyor belts or hydraulic systems, often necessitate unscheduled maintenance to prevent operational downtime. Unexpected breakdowns, caused by factors like wear and tear (detected after approximately 1,000 operational hours) or sudden overload (exceeding manufacturer weight limits by 20%), can lead to decreased production efficiency. Specialized inspections reveal alignment issues in rotating equipment or lubrication failures impacting bearing performance, sometimes identified through vibration analysis. Addressing these issues promptly is crucial to maintaining safety standards and operational reliability in facilities, such as manufacturing plants in Detroit, known for automotive production.
Expected timeline for completion
Unscheduled maintenance work can significantly impact operational efficiency across various sectors, such as manufacturing facilities or commercial offices. Typically, this work arises unexpectedly due to critical issues, such as equipment failures or safety violations that necessitate immediate attention. The anticipated timeline for completion often spans several days, depending on the complexity of the repairs and the availability of necessary parts or skilled technicians. For example, a malfunctioning HVAC system might require up to 72 hours for thorough inspection and parts replacement, while facility electrical repairs can demand up to a week to ensure safety and compliance with regulatory standards. Communicating this timeline both clearly and promptly is crucial to maintaining workflow continuity and minimizing disruption to employees or clients.
Contact information for inquiries
Unscheduled maintenance work can lead to operational disruptions, particularly in industrial settings like manufacturing plants or commercial buildings. For instance, emergency repairs may arise from equipment failure or safety inspections, prompting immediate attention from maintenance teams. In these scenarios, it is essential for stakeholders to have access to accurate contact information, such as a dedicated hotline number, email address, or a maintenance manager's direct line, to facilitate communication and inquiries. Efficient coordination ensures that all parties are informed about the status of the maintenance, potential downtime, and the expected resolution timeline, thus minimizing the impact on productivity and safety in the workplace.
Comments