Hey there! If you've ever found yourself juggling deadlines and project timelines, you know that sometimes a production schedule just needs a little tweaking. Whether it's due to unexpected delays or shifting priorities, adjusting your schedule can make all the difference in keeping everything on track. In this article, we'll explore some effective strategies for communicating these changes through a well-crafted letter. So, grab a coffee and letâs dive into how you can seamlessly navigate production adjustmentsâread on to discover more!
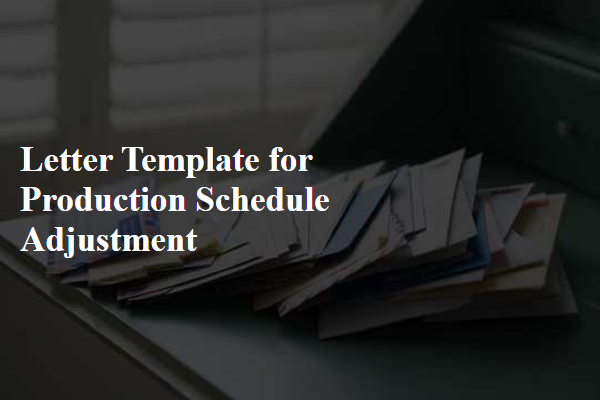
Clear communication of changes
Effective communication regarding production schedule adjustments is vital for minimizing disruption in manufacturing operations. For instance, a planned shift in the delivery timeline for raw materials, such as steel or plastic components, can lead to alterations in the production graphs of output, specifically for automotive or electronics assembly lines. Production personnel, including shift leaders and quality control teams, must be informed about any changes to ensure synchronization across departments. Clear notification via internal memos, updating shared digital calendars, or instant messaging platforms like Slack is recommended. Moreover, a revised schedule should highlight critical deadlines, such as the end of the current fiscal quarter, to ensure that all stakeholders remain aligned with operational objectives. Regular briefings or meeting announcements also facilitate transparency and foster a cooperative environment which is essential for maintaining production efficiency amidst changing schedules.
Impact assessment on timelines
Production schedule adjustments require a thorough impact assessment to understand the effect on timelines. Delays in material procurement, such as aluminum (used in automotive manufacturing), can shift project timelines by several weeks, affecting delivery dates. Additionally, labor shortages in regions like Southeast Asia, where many manufacturing plants are located, can further extend lead times for essential components. Equipment malfunctions, like those involving CNC machines (Computer Numerical Control) in production lines, can also cause significant interruptions, leading to cascading delays. It is crucial to evaluate these factors comprehensively to develop a revised timeline that accurately reflects operational realities and maintains project integrity. Implementing contingency plans, like alternative suppliers or shift adjustments, may help mitigate some of these impacts.
Explanation of reasons for adjustment
Production schedule adjustments often arise from unexpected delays in raw material shipments, requiring careful reevaluation of timelines. Supplier disruptions can stem from natural disasters, impacting logistics networks like trucking and shipping. Equipment failures, such as breakdowns in critical machinery like CNC machines or conveyors, necessitate immediate repairs to maintain production flow. Additionally, fluctuations in demand, noted during seasonal peaks (e.g., holiday seasons), may lead to increased output requirements. Workforce availability also plays a significant role, with potential shortages due to training programs or illness affecting labor capacity. All these factors combined necessitate a comprehensive recalibration of the production schedule to align with current operational capabilities and market needs.
Revised schedule with specific dates
The revised production schedule outlines key dates crucial for project completion in the manufacturing process. The new timeline includes the start of assembly on April 15, 2024, followed by quality checks scheduled for April 25, 2024. The shipping of finished products is planned for May 5, 2024, ensuring timely delivery to clients. Coordination meetings will take place bi-weekly to monitor progress and address any challenges. Resource allocation adjustments have also been made to maximize efficiency during peak production periods. Detailed reports on each stage will be compiled and assessed on April 30, 2024, to evaluate adherence to the revised deadlines.
Contact information for further inquiries
The production schedule adjustment requires immediate attention due to unforeseen delays in material supply, specifically the high-grade steel sourced from the Massachusetts factory. New timelines indicate a shift of 10 days in the completion date, affecting the overall delivery to clients in the New England region. For detailed inquiries regarding procurement status, quality assurance measures, or rescheduling, please contact the operations manager, Sarah Johnson, at (555) 123-4567 or via email at sarah.johnson@example.com. Further details can also be addressed through the customer service hotline, ensuring prompt responses to any production-related questions.
Letter Template For Production Schedule Adjustment Samples
Letter template of formal notice for schedule realignment in production.
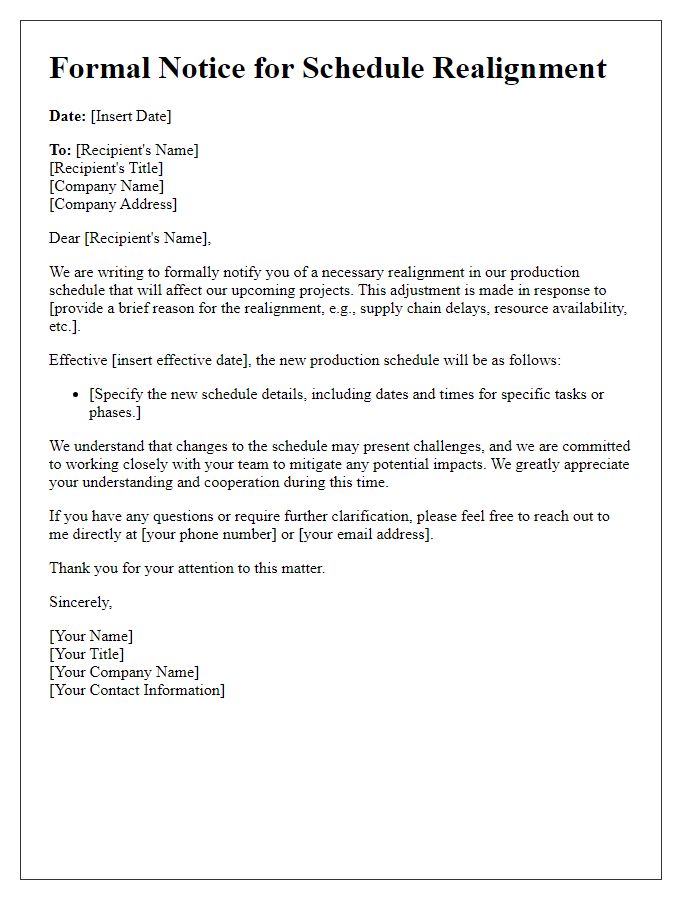
Comments