Are you considering expanding your production line but unsure where to start? Whether you're looking to boost efficiency, increase capacity, or enhance product quality, navigating the expansion process can feel daunting. In this article, weâll explore essential strategies and tips for a successful production line expansion that will set you up for growth. So, if you're ready to take your operations to the next level, join us as we dive deeper into this exciting topic!
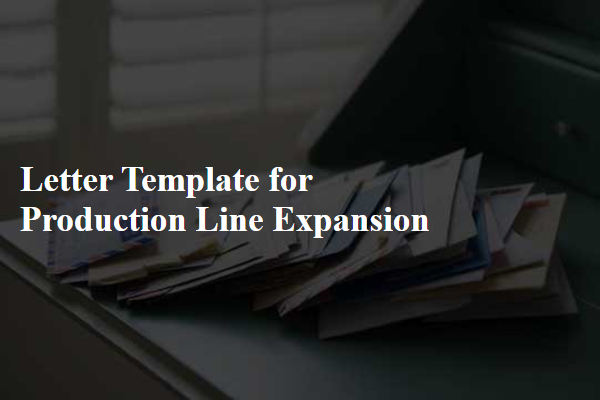
Purpose and Objectives
The purpose of the production line expansion at the central manufacturing facility in Springfield, Missouri, is to increase output capacity by 30% to meet rising consumer demand for the latest automotive models produced since 2022. Objectives include enhancing operational efficiency through the integration of state-of-the-art machinery and automation technology, as well as expanding workforce capabilities by recruiting 50 skilled technicians and engineers. The initiative aims to reduce production cycle time from 14 days to 10 days by optimizing workflow processes and minimizing bottlenecks. Furthermore, the installation of a new quality assurance system is crucial to maintaining product standards and improving customer satisfaction ratings, which currently stand at 85%. Overall, this expansion aligns with the strategic vision of achieving a 15% increase in market share by 2025 in the competitive automotive sector.
Project Scope and Timeline
The project scope for the production line expansion encompasses the installation of additional machinery, integration of automated systems, and expansion of the physical facility in the industrial zone of Springfield. A preliminary analysis has identified a need to increase output capacity by 30%, addressing growing demand for our flagship products, particularly the customized widgets. The project timeline spans six months, beginning in January 2024 with site preparation activities, followed by equipment procurement and installation in February. March will focus on testing and calibration of new systems, with full operational capacity anticipated by June 2024. Key milestones include securing permits from local authorities, completion of construction by mid-April, and training of 20 new staff members on the expanded line processes in May.
Budget and Financial Justification
The production line expansion project at the state-of-the-art facility located in Springfield aims to increase output capacity by 30% by the end of the fiscal year. This project requires an estimated budget of $2 million, which includes the procurement of new machinery, hiring additional personnel, and upgrading existing infrastructure. Financial projections indicate an anticipated return on investment (ROI) of 15% within the first two years due to reduced operational costs and increased product throughput. Additionally, market demand studies reveal a projected growth in sales volume of 20% in the automotive sector, underscoring the necessity for capacity enhancements. Furthermore, cost-benefit analysis suggests that the expansion will enable the company to capture larger market share while meeting customer demands more efficiently.
Potential Risks and Mitigation Strategies
Production line expansion presents various potential risks that require careful assessment and strategic mitigation. First, supply chain disruption can occur due to reliance on multiple suppliers for raw materials such as steel or plastics, which can delay production timelines. Financial risks include increased operational costs, which may arise from hiring additional workforce or investing in new machinery, potentially impacting the budget if not managed effectively. Compliance risks with industry regulations could lead to fines or project delays if safety standards are not adhered to in new production methods. Technological risks involve the integration of advanced automation systems, which may face compatibility issues, causing downtime. Finally, workforce training on new equipment can also pose risks; if not properly conducted, it can result in decreased efficiency and increased error rates. Effective strategies for mitigation include establishing strong supplier relationships, maintaining a contingency budget for unexpected costs, ensuring comprehensive compliance audits, investing in technology that supports scalability, and implementing thorough training programs for employees.
Communication and Stakeholder Engagement
Production line expansion involves careful communication and stakeholder engagement to ensure project success. Effective communication strategies include regular updates, informative meetings, and stakeholder feedback sessions that foster transparency. Key stakeholders like suppliers, employees, and local government officials must be engaged throughout the expansion process. Specific milestones, such as completion dates and budget reviews, must be clearly articulated. This approach not only improves collaboration but also mitigates potential risks associated with changes in production capacity or operational workflows. In addition, addressing stakeholder concerns regarding environmental impact and workforce adjustments is vital for maintaining positive relations and supporting community standards.
Comments