Are you looking for a reliable way to keep track of your machinery maintenance? A well-structured maintenance schedule can not only extend the life of your equipment but also enhance overall efficiency. In this article, we'll explore a comprehensive letter template that makes it easy to communicate maintenance plans with your team or clients. Join us as we delve into the essential components of an effective machinery maintenance schedule!
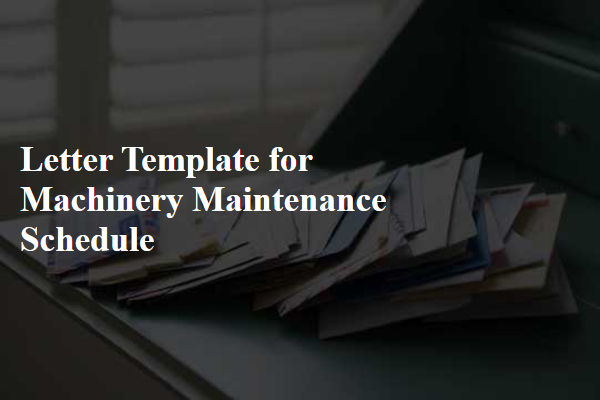
Machine Details
Routine maintenance for heavy machinery, such as bulldozers or excavators, is essential for optimal performance and longevity. Scheduled inspections, often every 250 operating hours, ensure that critical components like hydraulic systems and engines remain in top condition. Lubrication of moving parts, typically using high-quality greases, helps reduce friction and wear. Replacement of air filters, necessary every six months or 500 operating hours, improves engine efficiency and air quality in confined workspaces. Additionally, regular checks on safety features, like emergency shutdown mechanisms, are crucial for accident prevention, especially on construction sites in urban areas with high foot traffic. Documentation of maintenance activities plays an important role in compliance with industry standards and warranties. Implementing a comprehensive maintenance log can enhance operational safety and machine reliability, ultimately minimizing downtime and repair costs.
Maintenance Frequency
A well-structured machinery maintenance schedule is essential for ensuring the efficient operation of industrial equipment, such as CNC machines or conveyor systems. Maintenance frequency plays a crucial role in minimizing downtime and enhancing productivity. Daily maintenance tasks may include lubrication of moving parts and inspection for wear and tear. Weekly checks could involve cleaning filters and verifying safety mechanisms. Monthly assessments might encompass detailed inspections of electrical components, ensuring alignment, and replacing worn belts. Annual maintenance procedures should ideally include comprehensive overhauls, thorough examinations of hydraulic systems, and replacement of any aging components to maintain optimal machine performance and prolong equipment lifespan.
Tasks and Procedures
Creating a machinery maintenance schedule involves organizing a series of tasks and procedures essential for ensuring the longevity and efficient performance of industrial machines. Regular inspections (quarterly or bi-annually depending on usage) of critical components, such as belts, bearings, and hydraulic systems, are vital to identify wear and tear before major failures occur. Lubrication tasks (monthly) should include greasing joints and changing oils to reduce friction and extend component life. Safety checks (weekly) are important to evaluate emergency stops, guards, and sensors, ensuring all systems function safely. Documentation of maintenance activities within a tracking system enhances accountability and helps in analyzing performance metrics over time. Implementing a proactive maintenance approach can prevent unexpected downtimes and reduce repair costs significantly, fostering a more productive operational environment.
Safety Protocols
Machinery maintenance schedules must adhere to stringent safety protocols to ensure the well-being of operators and the longevity of equipment. Regular inspections should be conducted on critical components, such as hydraulic systems, electrical wiring, and safety guards. For example, hydraulic fluid levels must be checked weekly (every 7 days) to prevent leaks and system failures. Daily visual inspections (every 24 hours) of emergency shut-off switches and protective enclosures are essential to ensure quick response during emergencies. Furthermore, equipment such as forklifts and conveyor belts should undergo more comprehensive evaluations quarterly (every 3 months) according to Occupational Safety and Health Administration (OSHA) guidelines to maintain compliance with federal regulations. Utilizing personal protective equipment (PPE), such as gloves, helmets, and eye protection, is mandatory during all maintenance activities, reducing the risk of injury in potentially hazardous environments.
Contact Information
A comprehensive machinery maintenance schedule enhances operational efficiency and prolongs equipment lifespan. Essential elements include key machinery identifiers such as model numbers (e.g., Caterpillar 320D) and serial numbers (e.g., CAT03200X123456). The schedule details specific maintenance tasks, frequency intervals (monthly, quarterly, annually), and responsible personnel. Include contact information for maintenance personnel, highlighting emails, phone numbers, and operational hours (e.g., 8 AM to 5 PM, Monday to Friday). Additionally, record parts suppliers for essential replacements, including parts numbers and vendor contact details. Documenting maintenance history fosters compliance with industry standards and aids in troubleshooting future mechanical issues.
Comments