In todayâs fast-paced business landscape, ensuring the highest quality standards is crucial for success. A well-structured quality assurance procedure not only boosts customer satisfaction but also enhances overall operational efficiency. By implementing effective QA protocols, organizations can proactively identify and rectify issues before they escalate. So, if youâre looking to elevate your quality assurance practices, read on to discover essential templates and tips that can transform your approach!
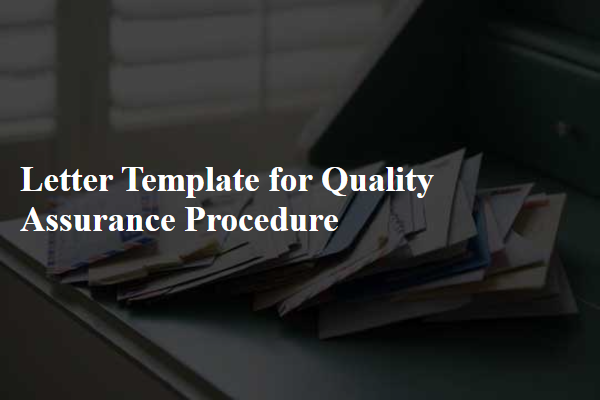
Introduction and Purpose
A quality assurance procedure outlines systematic processes and guidelines to ensure the delivery of high-standard products or services. The primary purpose is to enhance performance consistency and reliability across various departments or teams, such as manufacturing, customer support, and software development. This document aims to define roles, responsibilities, and methods to identify and mitigate risks associated with product quality, ensuring compliance with established industry standards like ISO 9001. Effective implementation of these procedures can lead to increased customer satisfaction, reduced defects, and improved operational efficiency while fostering a culture of continuous improvement within the organization.
Scope of Application
The scope of application for the quality assurance procedure encompasses all organizational departments involved in the production and delivery of services and products. This includes the design, development, manufacturing, and customer service sectors. Specific focus areas include compliance with established quality standards such as ISO 9001:2015 and adherence to relevant regulations in industries such as pharmaceuticals, automotive, or food safety. The procedure aims to ensure consistency in product quality, minimize defects, and enhance customer satisfaction at every stage of the process from raw material procurement to post-sale support. Stakeholders involved include quality assurance teams, production staff, management personnel, and external auditors, ensuring comprehensive oversight and continuous improvement in overall operational efficiency.
Quality Assurance Definitions
Quality assurance (QA) involves systematic processes aimed at ensuring that products and services meet specified requirements and standards. Key definitions under QA include: Quality Control (QC), which refers to the operational techniques and activities used to fulfill quality requirements throughout the production cycle; Total Quality Management (TQM), a management approach focused on long-term success through customer satisfaction and the continuous improvement of organizational processes; and Six Sigma, a set of techniques for process improvement, aiming to reduce defects and improve overall quality. Additionally, compliance auditing, an assessment process conducted to ensure adherence to regulatory and internal guidelines, plays a crucial role in maintaining standards across various industries, including pharmaceuticals and manufacturing. Quality assurance frameworks, such as ISO 9001, provide structured guidelines for establishing, implementing, maintaining, and improving an effective quality management system.
Roles and Responsibilities
Quality assurance (QA) processes establish crucial roles and responsibilities within organizations striving for excellence. The QA Manager oversees the entire quality assurance program, ensuring compliance with standards such as ISO 9001 and auditing procedures. Quality Analysts conduct routine evaluations of products, measuring defects per million opportunities (DPMO) to maintain quality benchmarks. Document Control Specialists manage vital documents, ensuring version control and availability to team members. Training Coordinators develop training sessions for staff, focusing on quality standards and methodologies like Six Sigma. Additionally, the cross-functional Quality Improvement Teams collaborate on continuous improvement initiatives, utilizing tools such as root cause analysis and process mapping to enhance operational efficiency. Each role significantly contributes to fostering a culture of quality.
Procedures and Guidelines
Quality assurance procedures are essential for maintaining high standards in organizations, particularly in the manufacturing sector. Detailed guidelines, such as ISO 9001:2015, establish a framework for consistently delivering products that meet customer expectations and regulatory requirements. The quality control process involves several critical steps, including quality planning, quality control, quality improvement, and documentation management. Each step requires specific metrics, like defect rates below 1% and on-time delivery rates above 95%, ensuring continuous monitoring and assessment of quality processes. Training sessions in places like production facilities or laboratories are crucial for employee awareness and compliance with standard operating procedures (SOPs). Regular audits, both internal and external, are conducted to verify adherence to procedures, assess effectiveness, and identify areas for enhancement. An effective quality assurance system ultimately contributes to customer satisfaction, brand loyalty, and overall business success.
Comments