Hey there! We all know how important it is to stay updated on project timelines, especially when changes arise. Recently, weâve noticed a shift in our lead time that could impact our collaboration. To make sure youâre in the loop and fully prepared, Iâve outlined all the details in the following article, so feel free to dive in and read more!
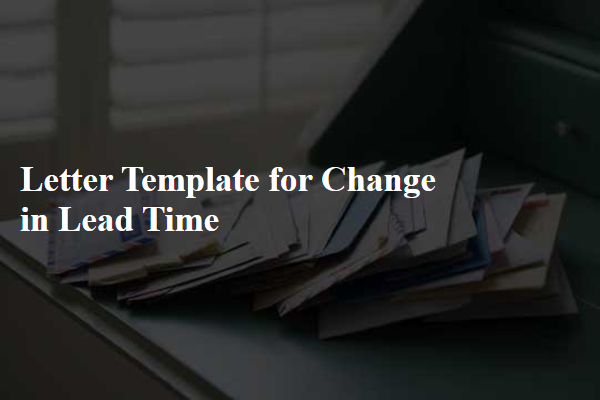
Clear Subject Line
Changes in lead times for product availability can significantly impact supply chain operations and customer satisfaction. For instance, a shift in lead time from 10 days to 15 days for electronic components can disrupt manufacturing schedules at facilities like those in Shenzhen, China, where many components are sourced. Industries reliant on Just-In-Time inventory methods may face production delays, affecting delivery schedules to retailers in North America. Notifying stakeholders about adjustments is crucial, ensuring transparent communication to mitigate any potential disruptions across supply chains.
Personalized Greeting
Due to recent changes in our supply chain dynamics, alterations in lead times for our product delivery schedules have become necessary. The updated lead time now stands at 14 to 21 business days, reflecting adjustments made to accommodate heightened demand and potential logistical disruptions. This change, while designed to enhance overall service quality, will affect shipments originating from our distribution center located in Dallas, Texas. Order tracking systems will remain operational, enabling customers to monitor their delivery status in real-time. We appreciate your understanding and continued loyalty as we navigate this transition.
Explanation of Change
Supply chain disruptions can significantly impact lead times for product delivery, particularly in manufacturing sectors. Unexpected events such as natural disasters, geopolitical tensions, or the COVID-19 pandemic have created bottlenecks in transportation networks, resulting in increased shipping times by an average of 20-30%. Furthermore, shortages in raw materials, such as semiconductors and steel, have extended production timelines, pushing manufacturers to revise delivery estimates. Enhanced communication with suppliers in Asia or Europe may improve forecasting accuracy, but fluctuations in demand remain unpredictable. Implementing strategies to mitigate these delays, such as local sourcing or adjusting inventory levels, is crucial for maintaining customer satisfaction. Adjusted lead time notifications should be communicated clearly to all stakeholders involved in the procurement process.
Impact on Stakeholder
Changes in lead time, affecting delivery schedules, can significantly impact stakeholders reliant on timely product availability. Suppliers may experience increased pressure to adjust their logistics strategies, while manufacturers may face production delays caused by the lack of necessary materials. Customers relying on scheduled deliveries for operational stability can encounter disruptions, leading to potential financial losses and dissatisfaction. Furthermore, planning departments must revise project timelines and resource allocations, which can strain team productivity and morale. Communication with all involved stakeholders, including logistics partners, sales teams, and end-users, becomes critical for mitigating negative effects and maintaining trust throughout the supply chain.
Contact Information
Delay in order fulfillment can significantly impact supply chain efficiency, especially for businesses requiring just-in-time delivery. Lead time, defined as the period from order placement to fulfillment, can vary based on several factors, including supplier availability and transportation logistics. For instance, a typical lead time for electronics components can range from 2 weeks to several months, depending on the sourcing location and demand fluctuations. A sudden increase in lead time may disrupt production schedules at facilities such as factories and assembly plants, leading to potential bottlenecks in operations. Moreover, communicating changes in lead time to stakeholders, including suppliers and customers, is essential for maintaining transparency and minimizing the effects on planned activities.
Comments