Hey there! If you've ever faced the challenge of managing inventory levels, you're not alone. An inventory shortfall can hinder operations and impact customer satisfaction, making clear communication crucial. In this article, we'll explore the best practices for notifying stakeholders about inventory shortages and how to effectively mitigate their impact. So, grab a cup of coffee and let's dive deeper into this essential topic!
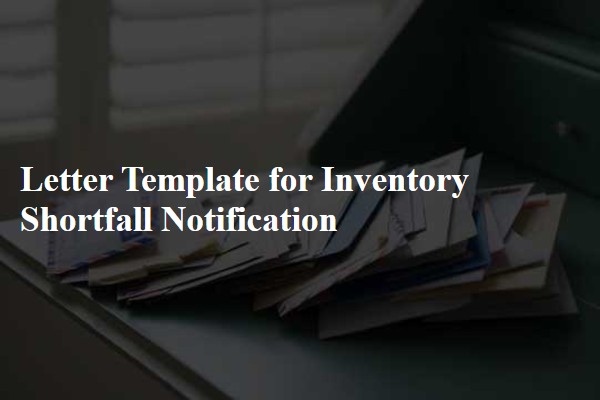
Clear identification of shortfall issue
Inventory shortfall issues can significantly impact operational efficiency and customer satisfaction. A notable example is a retail chain experiencing a 30% shortfall in stock levels of essential items, such as electronics during the peak shopping season (November to December). The primary cause often relates to supply chain disruptions, such as delays from suppliers based in regions like Southeast Asia due to shipping container shortages. Accurate identification of affected items, like the latest smartphone models or popular gaming consoles, is crucial for timely communication. Implementing inventory management systems that employ real-time tracking can help mitigate future occurrences, ensuring adequate stock availability and maintaining consumer trust.
Specific details of affected inventory items
Inventory shortfalls can disrupt supply chain operations significantly, affecting businesses' ability to meet customer demand efficiently. Recent analysis indicates discrepancies in critical inventory levels across various product categories, including electronics, clothing, and household items. For instance, a shortage of high-demand smartphones, particularly the iPhone 14 model, has been observed with only 15 units remaining, while expected demand forecasts indicate a requirement of 150 units for the upcoming quarter. Similarly, clothing items from the Fall 2023 collection, specifically the women's winter jackets, show a significant shortfall with only 100 pieces available versus a target of 500 pieces. Household items, particularly kitchen appliances like the Instant Pot, reflect an alarming shortage of 80 units out of a planned stock of 250. Immediate action is necessary to address these discrepancies, including reassessing supplier agreements and considering emergency restocking options.
Explanation of reasons for the shortfall
Inventory shortfalls can occur due to various factors, including supply chain disruptions, unexpected spikes in demand, stock mismanagement, and logistical challenges. Supply chain disruptions may arise from natural disasters, geopolitical tensions, or vendor issues, which can delay shipments of essential materials. Unexpected spikes in demand can result from seasonal trends, promotional events, or market shifts, leading to a depletion of available stock faster than anticipated. Stock mismanagement may involve inaccurate record-keeping or forecasting errors, creating an illusion of sufficient inventory when it is not present. Logistical challenges, such as transportation delays or warehouse inefficiencies, can also contribute to shortfalls, preventing timely replenishment of essential products. These combined factors underscore the complexities of inventory management and necessitate proactive strategies to mitigate future shortages.
Proposed corrective actions or solutions
Inventory shortfalls can significantly disrupt business operations, particularly in retail environments where stock levels fluctuate based on consumer demand and seasonal trends. A shortfall may occur due to various factors, including inaccuracies in supply chain management, unexpected spikes in product demand, or even logistical delays. Accurate inventory tracking systems play an essential role in preventing these situations. Implementing corrective actions, such as conducting thorough audits of current stock and enhancing order forecasting techniques based on historical sales data, can prevent future discrepancies. Vendors might need to be assessed and renegotiated to ensure a reliable supply chain. Additionally, training staff on improved inventory management practices could reduce human error and enhance accountability. These solutions aim to stabilize stock levels and mitigate the impact of shortages on customer satisfaction and revenue.
Impact assessment and future prevention measures
Warehouse inventory shortfalls can significantly disrupt supply chain operations, impacting businesses like retail or manufacturing. A notable shortfall, such as a 20% decrease in stock levels, can lead to halted production lines or empty store shelves, resulting in lost sales revenue exceeding thousands of dollars daily. Noteworthy events contributing to these shortfalls include vendor delays and unexpected spikes in consumer demand, often influenced by seasonal trends or promotional campaigns. To prevent future occurrences, implementing real-time inventory tracking systems, automated reorder alerts, and robust supplier relationships are vital. These measures can enhance visibility into stock levels, allowing businesses to adjust procurement strategies proactively, ultimately ensuring consistent product availability and customer satisfaction.
Comments