Dear valued partners, we understand that navigating supply chain disruptions can be challenging, and we want to keep you informed every step of the way. As our industry faces unexpected hurdles, transparency and communication are key in maintaining strong relationships. In this article, we'll explore effective strategies to manage these disruptions and ensure a smoother operation going forward. So, join us as we dive deeper into the solutions that can help your business thrive even in uncertain times!
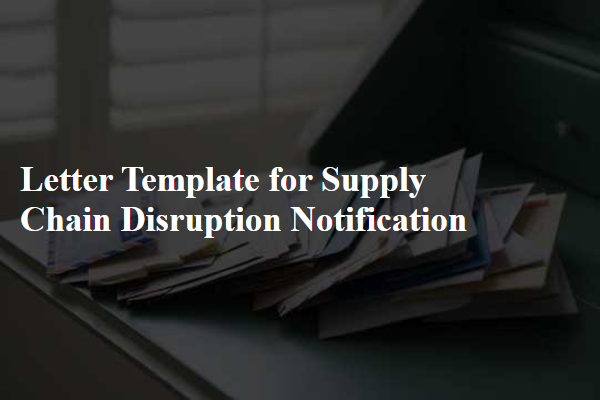
Clear and Concise Communication
Supply chain disruptions significantly impact operations and deliveries for businesses globally. Factors such as natural disasters, vehicle shortages, regulatory changes, or even geopolitical tensions can create delays. Supply chain networks often span multiple countries, with manufacturers in places like China, shipping hubs in Singapore, or logistics centers in the United States. An increase in lead times, sometimes extending to several weeks, exacerbates product shortages. These disruptions can lead to financial losses, affect customer satisfaction, and require adjustments to inventory management strategies. Timely communication is crucial to manage expectations and maintain stakeholder trust during such events.
Specific Details of Disruption
Supply chain disruptions can occur due to various factors, including natural disasters, transportation issues, or supplier failures. Recent events, such as Hurricane Fiona impacting the Caribbean region in September 2022, have caused significant delays. Areas like Puerto Rico and the Dominican Republic faced logistical challenges due to damaged infrastructure and port closures. This situation resulted in longer lead times for essential materials, including electronics and perishable goods. Consequently, affected companies may experience shortages, forcing them to reassess inventory management and establish alternative supplier relationships to mitigate future risks.
Impact Analysis and Mitigation Plans
Supply chain disruptions due to unforeseen events, such as natural disasters (e.g., hurricanes or earthquakes), trade restrictions, or global pandemics, can critically impact operations and delivery schedules. Such disruptions may lead to delays in production (often exceeding 30% in various sectors) and result in increased costs, with companies facing potential losses that can reach millions. Key players, including suppliers, manufacturers, and logistics providers, must rapidly adapt through risk assessment strategies and contingency plans. Implementing alternative sourcing methods, stockpiling essential materials, and utilizing advanced technology in tracking and inventory management can help mitigate these effects. Collaboration among stakeholders is crucial during these disruptions to ensure transparency and efficient communication. Regular assessments of the supply chain's resilience are essential to identify vulnerabilities and strengthen response strategies.
Expected Duration and Updates
Supply chain disruptions can significantly impact operations and delivery schedules across various industries. Recent events, such as natural disasters or geopolitical conflicts, have led to delays in materials and products. Currently, disruptions are anticipated to last for an estimated four to six weeks, affecting key suppliers based in regions like Southeast Asia and Eastern Europe. Updates will be communicated weekly, detailing the status of affected shipments, including changes in timelines for essential goods. Stakeholders are encouraged to implement alternative sourcing strategies and prepare for potential impacts on inventory levels to mitigate the effects of these disruptions.
Contact Information for Further Queries
Supply chain disruptions can significantly impact operations, particularly in industries relying on timely deliveries. During recent global events, such as the COVID-19 pandemic or natural disasters like hurricanes, companies often face delays in transportation and logistics. For example, shipping routes through the Suez Canal can become congested, causing delays of weeks or even months for goods. Effective communication is essential to address concerns regarding affected orders, logistics changes, or estimated delivery times. Therefore, maintaining clear contact information for further queries becomes crucial. Key department contacts such as logistics managers or customer service representatives should be provided, ideally through multiple channels, including email addresses and phone numbers, ensuring swift resolutions and ongoing support for clients dealing with uncertainty during these disruptions.
Comments