Are you looking to streamline your logistics processes and improve overall efficiency? In todayâs fast-paced world, optimizing your supply chain is more crucial than ever, and even small changes can lead to significant benefits. From enhancing inventory management to improving delivery times, there are many strategies you can implement to revamp your logistics. Curious about the best practices and actionable tips? Let's dive into the details!
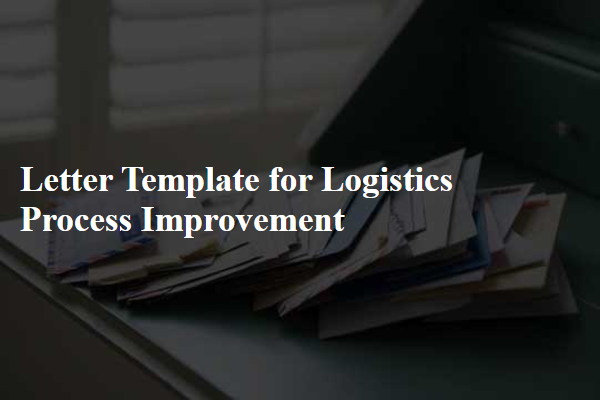
Clear Statement of Purpose
Logistics process improvement aims to enhance efficiency, reduce costs, and optimize supply chain operations. Inefficient logistics operations can lead to delayed deliveries, increased operational costs, and customer dissatisfaction. For instance, the average delivery time for packages in the United States is around 1.5 days, with companies like FedEx and UPS striving to improve this metric. By analyzing critical components such as inventory management, transportation systems, and warehouse operations, organizations can identify bottlenecks that hinder performance. Implementing advanced technology, such as real-time tracking software, can streamline communication and provide visibility throughout the logistics process. Additionally, adopting best practices for route optimization can significantly reduce fuel consumption and delivery times, which is crucial, given that the transportation sector accounts for approximately 29% of greenhouse gas emissions in the United States. Overall, focusing on logistics process improvement not only enhances operational efficiency but also contributes to a more sustainable and customer-centric supply chain.
Identification of Current Challenges
Logistics processes often encounter significant challenges that hinder efficiency and effectiveness. Common issues include inventory management discrepancies, such as stockouts or overstock situations that can lead to increased holding costs, and delays in transportation, with average shipping times exceeding industry benchmarks of 24 to 48 hours for domestic deliveries. Poor communication between stakeholders, like suppliers and carriers, can result in misalignment and lost information, impacting overall supply chain visibility. Additionally, reliance on outdated technology, including legacy warehouse management systems that lack real-time tracking capabilities, may contribute to inefficiencies. Furthermore, employee training deficiencies can lead to errors in order fulfillment, negatively affecting customer satisfaction ratings, which tend to average around 75 percent in logistics sectors lacking effective training programs. Addressing these challenges requires a comprehensive analysis and implementation of strategic improvements tailored to specific operational needs.
Proposed Solutions and Strategies
In the logistics sector, implementing innovative process improvements can significantly enhance efficiency. Automated tracking systems, such as RFID technology, offer real-time visibility of goods (reducing loss and streamlining inventory management). Adopting advanced software solutions for route optimization can decrease transportation costs, improving delivery times by up to 30% in some regions. Collaborative partnerships with local carriers, particularly in metropolitan areas like New York City and Los Angeles, enable businesses to leverage existing infrastructures and reduce last-mile delivery challenges. Regular training programs for staff on using modern tools and best practices not only increase productivity but also boost employee morale, ensuring a well-informed workforce that can swiftly adapt to evolving market demands. Emphasizing sustainability through eco-friendly packaging and green logistics can also enhance brand reputation while contributing to environmental conservation efforts.
Implementation Timeline
The logistics process improvement project involves several key stages designed to enhance efficiency and reduce costs within the supply chain framework. The initial phase, which includes a thorough assessment of current systems and identification of bottlenecks, spans approximately 4 weeks. This phase takes place across various locations, including warehouses in Seattle and distribution centers in Dallas, allowing for a comprehensive analysis of operational workflows. Following this, the development of optimization strategies will occur, taking around 6 weeks, during which stakeholders will collaborate to determine the most impactful changes. The implementation of selected strategies will commence in the 12th week and is expected to last for approximately 8 weeks, focusing on critical areas such as inventory management and transportation routing. Finally, a monitoring and evaluation phase of 6 weeks will ensure that the improvements yield desired outcomes, allowing for adjustments as necessary to maximize overall logistical performance.
Expected Benefits and Impact
Logistics process improvement initiatives can lead to significant enhancements in efficiency across supply chain operations, particularly in the distribution centers and transportation sectors. Streamlined workflows can reduce lead times, with studies showing potential reductions of up to 30%, leading to faster delivery times for customers and decreased operational costs. Implementing automated systems, such as Warehouse Management Systems (WMS), can increase inventory accuracy by over 95%, minimizing stock discrepancies and improving order fulfillment rates. Enhanced tracking and visibility of shipments through IoT and GPS technologies can lead to better decision-making, reducing lost shipments and improving delivery accountability. Furthermore, sustainability initiatives, such as optimizing route planning through Advanced Planning Systems (APS), can reduce carbon emissions and fuel costs, benefiting both the environment and the bottom line. Ultimately, these improvements can foster stronger customer relationships and increase overall satisfaction, encouraging repeat business and loyalty.
Comments