Are you ready to tackle those long-overdue home repairs? Whether it's fixing leaky faucets or conducting seasonal maintenance, having a well-structured schedule can make all the difference. In this article, weÂ’ll walk you through a practical template for organizing your maintenance work, ensuring that every task is completed efficiently and on time. So grab a cup of coffee and letÂ’s dive into the details that will help keep your home in tip-top shape!
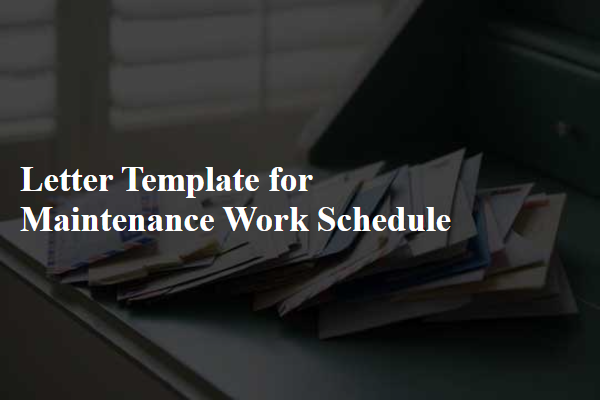
Clear and Formal Language
Maintenance work schedules are crucial for ensuring operational efficiency in facilities such as manufacturing plants. Scheduled maintenance, typically performed quarterly (every three months), minimizes equipment downtime and extends the lifespan of machinery. For instance, HVAC systems may require checks every season to ensure optimal performance and energy efficiency. Safety equipment inspections, mandated by regulations like OSHA (Occupational Safety and Health Administration), must also be conducted at least annually to comply with legal standards. Comprehensive reports detailing the condition of equipment and any required repairs should be documented after each maintenance session to track performance over time. Coordination with various departments such as operations and safety is essential to minimize disruptions during the maintenance period and ensure all personnel are informed of scheduled downtime.
Specific Dates and Times
Scheduled maintenance work includes tasks to ensure optimal performance and safety in various systems. Specific dates range from November 1 to November 15, 2023, targeting both weekdays and weekends for minimal disruption. Maintenance windows are set between 8:00 AM and 5:00 PM, accommodating different operational hours of facilities. Key tasks include inspections of HVAC systems, electrical systems, and plumbing fixtures, all vital for environmental control and safety compliance. Technicians will employ a preventive maintenance approach to address potential issues, enhancing system longevity and reliability. Users can expect notifications 48 hours in advance, allowing for adjustments to schedules and minimizing disruptions.
Detailed Task Description
The maintenance work schedule details essential tasks for optimal facility functionality, as in the case of HVAC systems or emergency generators. Each task, such as air filter replacement (recommended every 3 months for peak efficiency) or lubrication of moving parts (quarterly intervals to prevent failure), is critical. A comprehensive inspection of fire safety systems, including smoke detectors and sprinkler systems (required yearly by local fire codes), ensures compliance and occupant safety. Plumbing checks, particularly of pipes and drain systems (critical during seasonal changes to prevent freezing), aim to identify leaks or blockages proactively. Lastly, routine cleaning of electrical panels and equipment (suggested every six months), enhances safety and prevents potential hazards related to dust accumulation.
Contact Information for Queries
The maintenance work schedule serves as a crucial roadmap for ensuring the upkeep of facilities and equipment. Clear contact information is essential for addressing queries related to scheduling and the scope of work involved. For example, facilities management teams may provide phone numbers such as (555) 123-4567 or email addresses like maintenance@facilityservices.com to streamline communication. This allows staff, tenants, or stakeholders to seek clarification on specific tasks like plumbing repairs, electrical work, or landscaping. Additionally, including office hours (e.g., 9 AM to 5 PM, Monday through Friday) enables individuals to reach out during designated times for immediate assistance, fostering accountability and transparency in the maintenance process.
Notification and Response Deadlines
Maintenance work schedules require clear communication regarding notification and response deadlines for effective planning and execution. For instance, scheduled maintenance for commercial facilities, such as office buildings or manufacturing plants, typically demands advance notice of at least 14 days to allow for coordination with affected employees and clients. Specific deadlines can vary: emergency repairs might necessitate immediate notification, while routine inspections may have a grace period of 7 days for response. Properly documenting these timelines ensures that all stakeholders, from facility managers to maintenance personnel, are informed and prepared for any disruptions. This structured approach enhances operational efficiency and minimizes service interruptions during the maintenance process.
Comments