In today's fast-paced work environment, streamlining operational processes is essential for efficiency and productivity. We all encounter challenges that could benefit from thoughtful improvements, and sharing our insights can foster a collaborative atmosphere for positive change. Whether you're on the front lines or managing within the organization, your perspective is invaluable in shaping a more effective workflow. Join me as we explore some practical suggestions for enhancing our operational processesâread on for more details!
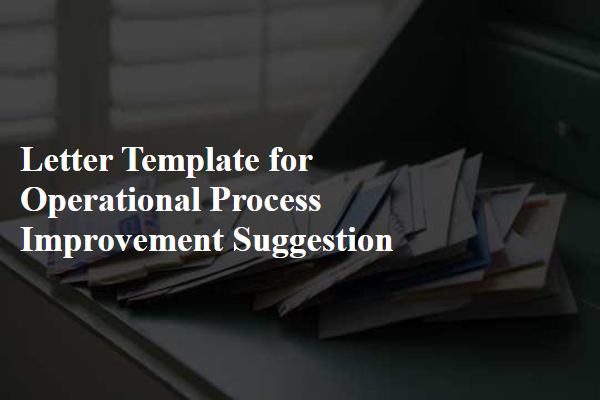
Clear identification of current process and issues.
Current operational processes often experience inefficiencies, particularly in inventory management systems used in retail environments, such as the implementation of outdated software that fails to provide real-time tracking (lagging up to 48 hours). Frequent stock discrepancies lead to losses estimated at $100,000 annually. Additionally, the manual handling of data entry in spreadsheets increases human errors by approximately 25%. Ineffective communication channels among departments, such as shipping and sales, create delays in order fulfillment, extending delivery times beyond the industry standard of 3-5 business days. Implementing a centralized digital platform could streamline these processes, improve accuracy, and enhance interdepartmental collaboration, resulting in reduced costs and improved customer satisfaction ratings above the current 70%.
Detailed suggestion for improvement.
Operational processes in manufacturing can greatly benefit from implementing Lean Six Sigma methodologies. This approach focuses on eliminating waste (non-value-added activities) while improving product quality (reducing defects). For instance, utilizing Value Stream Mapping (a tool to visualize the flow of materials and information) can identify bottlenecks in production lines, allowing for optimized workflow and resource allocation. Additionally, incorporating regular training sessions for employees on continuous improvement practices (like Kaizen events) can foster a culture of proactive problem-solving and innovation. This method encourages teams to suggest small, incremental changes regularly, leading to significant long-term enhancements. The result is a more efficient operation with improved cycle times and reduced operational costs, ultimately enhancing overall productivity.
Benefits and impact analysis.
Operational process improvement suggestions can significantly enhance efficiency and productivity within an organization. An analysis of potential benefits may include reduced cycle times (the time taken from the start to the completion of a task), leading to faster service delivery and increased customer satisfaction. Cost savings can also be anticipated, potentially reducing overhead expenses by up to 20% through streamlined workflows and elimination of redundancies. Furthermore, improved employee engagement is likely as streamlined processes often lead to clearer roles and responsibilities, thereby enhancing morale and reducing turnover rates. The overall impact may manifest as a more agile organization that can quickly adapt to market changes, thereby maintaining a competitive edge in the industry.
Stakeholder engagement and feedback.
Stakeholder engagement is crucial for successful operational process improvements in organizations, encompassing various departments and team members. Regular feedback from stakeholders, including employees, clients, and partners, enables the identification of inefficiencies and areas for enhancement within existing workflows. Utilizing surveys, workshops, and focus groups, organizations can gather comprehensive insights that inform strategic changes. Implementing suggestions from stakeholders, such as the adoption of new technology or revised communication standards, fosters a culture of collaboration and transparency. Additionally, tracking progress through performance metrics can provide valuable data, ensuring that enhancements lead to measurable outcomes in productivity and satisfaction levels across all involved parties.
Strategic alignment and goal relevance.
Operational process improvement suggestions often focus on strategic alignment and goal relevance to enhance organizational efficiency. Analyzing current operational workflows, it becomes essential to ensure that each process aligns with overarching strategic objectives, such as increasing market share, optimizing resource allocation, or enhancing customer satisfaction. Regular review meetings, ideally quarterly, can help assess if departmental goals match the company's mission, adjusting key performance indicators (KPIs) accordingly. Implementing tools like SWOT analysis (Strengths, Weaknesses, Opportunities, Threats) can shed light on areas needing improvement while guiding teams towards actionable objectives that are directly relevant to the organization's success. Investing in training programs, designed to cultivate skills that promote strategic thinking, might also bridge gaps in alignment, fostering a culture that prioritizes goal-oriented actions across all levels of the organization.
Comments