Hello there! If youâve ever found yourself low on essential supplies or struggling to keep your shelves stocked, you know how crucial a well-structured inventory restocking request can be. Crafting the perfect letter not only streamlines the process but ensures that your needs are communicated clearly and effectively. In this article, weâll walk you through a simple yet impactful template that will help you address your restocking needs with confidence. Ready to dive in? Letâs explore together!
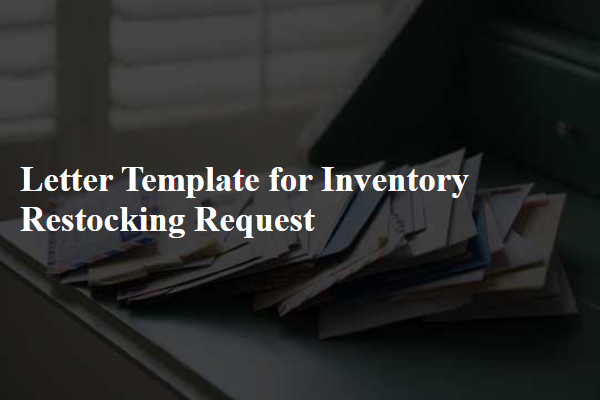
Clear product identification
Inventory restocking requests require clear product identification to ensure accurate fulfillment. Key elements include the product name, SKU (Stock Keeping Unit) number, and description. Products like Apple iPhone 14 (model A2649) necessitate detailed specifications such as color, storage capacity (128GB, 256GB), and condition (new, refurbished). Additionally, including the supplier's name (e.g., Apple Inc.), reorder quantity based on sales data trends, and preferred restock lead time (within 7 days) optimizes the replenishment process. Accurate identification prevents errors and aligns the inventory system with actual stock levels, enhancing operational efficiency.
Accurate quantities needed
Inventory restocking is a critical process for maintaining optimal operational efficiency in businesses, particularly in retail environments. For example, the warehouse located at 123 Commerce Street may have a current stock of 200 units of product XYZ (category: consumer electronics). Recent sales data from the last quarter indicates a monthly turnover rate of 150 units, necessitating a restock to prevent stockouts. Accurate quantities are essential, with a suggested replenishment of 300 units to ensure sufficient supply for upcoming promotional events planned for November 2023. Additionally, utilising an inventory management system (IMS) can streamline this process, providing real-time analytics on stock levels and turnover rates to avoid overstocking, which commonly leads to increased operational costs and potential wastage.
Supplier contact information
Maintaining appropriate inventory levels is crucial for smooth operations across businesses. Accurate inventory management systems are essential to monitor stock levels, such as inventory management software like Zoho Inventory or QuickBooks. Timely restocking requests to suppliers, such as ABC Wholesale with contact information at (555) 123-4567 or contact@abcwholesale.com, ensure that essential products remain available. Regular communication regarding demand forecasting (analyzing sales patterns) can strengthen supplier relationships. Utilizing precise ordering methods, like electronic purchase orders, can streamline the restocking process while minimizing delays and inaccuracies. Additionally, implementing a reorder point calculator helps in determining the optimal time for placing restocking orders based on lead times and sales velocities.
Desired delivery timeline
A well-organized inventory management system is essential for businesses, particularly retail stores and warehouses, to maintain optimal stock levels. Inventory restocking requests become crucial when supplies reach a low threshold, often set at 20% of total stock capacity. A timely restock ensures that customers do not face delays while processing orders, impacting satisfaction levels. The desired delivery timeline, typically ranging from 3 to 7 business days (depending on shipping methods), must be communicated clearly to suppliers to avoid interruptions in operations. Accuracy in forecasting demand--using historical sales data from the previous quarter--can greatly enhance the efficiency of the restocking process, leading to increased sales and reduced inventory holding costs.
Authorization and signatures
An efficient inventory restocking request can lead to smoother operations in a business environment. A well-structured request typically includes key details such as item descriptions, quantities needed, and current stock levels. For instance, a request for restocking 50 units of high-demand products like wireless headphones from leading brands such as Bose or Sony can optimize sales performance. Additionally, authorization signatures from relevant department heads such as the Supply Chain Manager or Warehouse Supervisor ensure that the request is validated and aligns with budget constraints. Providing timelines for receiving backordered items, often taking two to three weeks, can further enhance the planning process. Ensuring accuracy in this communication not only boosts inventory efficiency but also enhances operational workflows.
Letter Template For Inventory Restocking Request Samples
Letter template of inventory restocking confirmation for supplier agreements
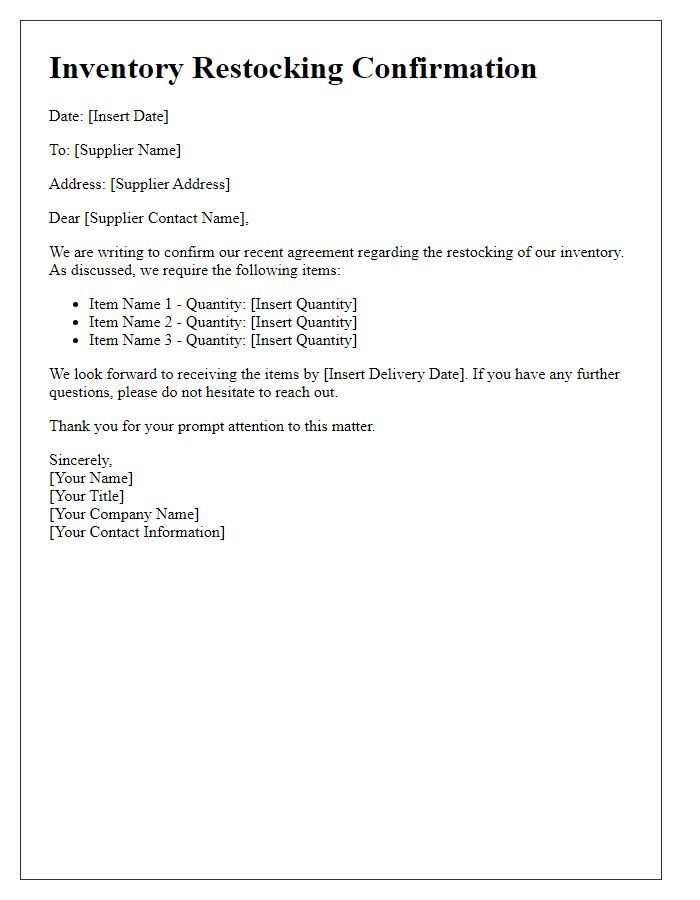
Letter template of inventory restocking recommendation for product lines
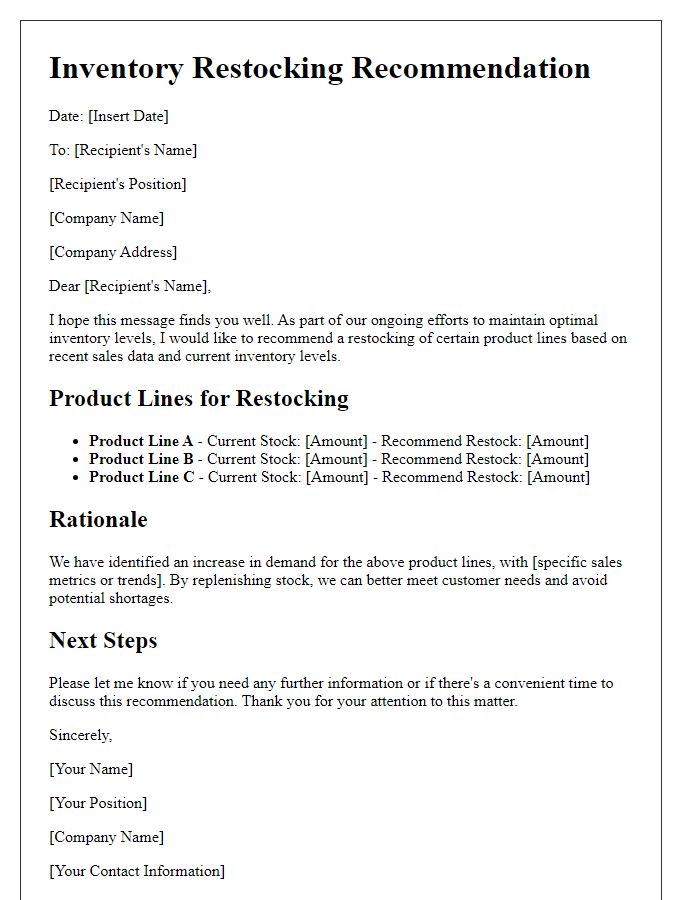
Letter template of inventory restocking schedule for upcoming promotions
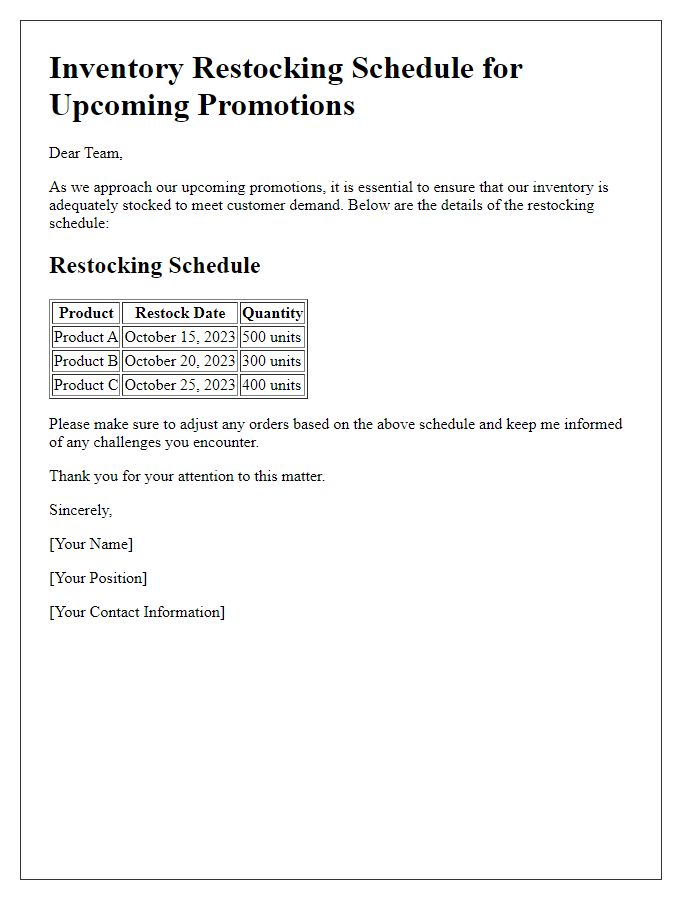
Letter template of inventory restocking status request for existing orders
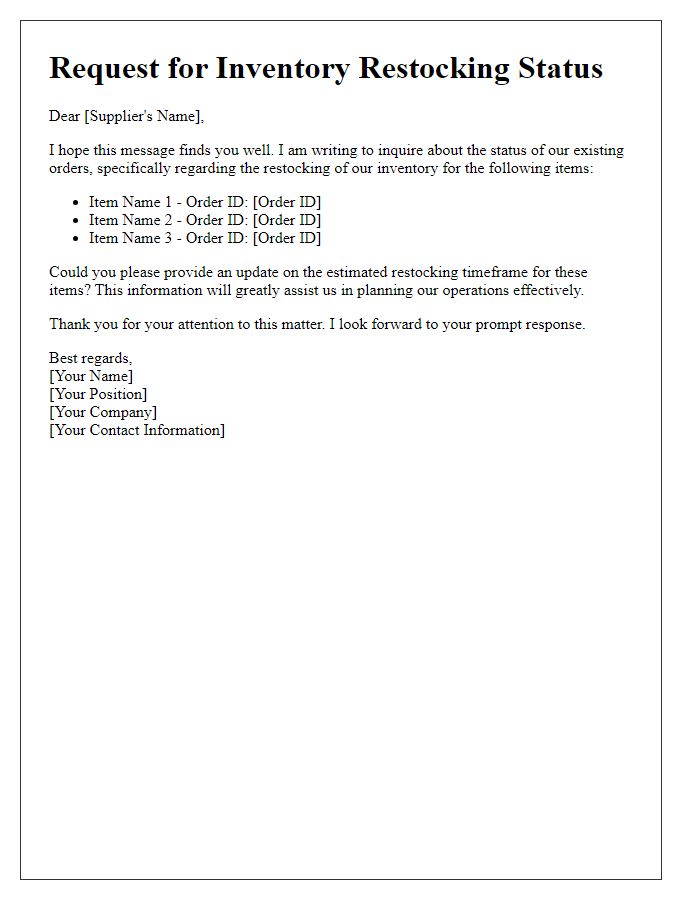
Comments