Hey there! We know that navigating supply chain disruptions can be tricky and stressful for everyone involved. With factors like global events and delivery delays affecting our operations, we want to keep you in the loop about what's happening and how we're addressing these challenges. We believe transparency is key, so letâs dive into the details of these disruptions and the steps we're taking to mitigate their impact. Keep reading for more insights and updates!
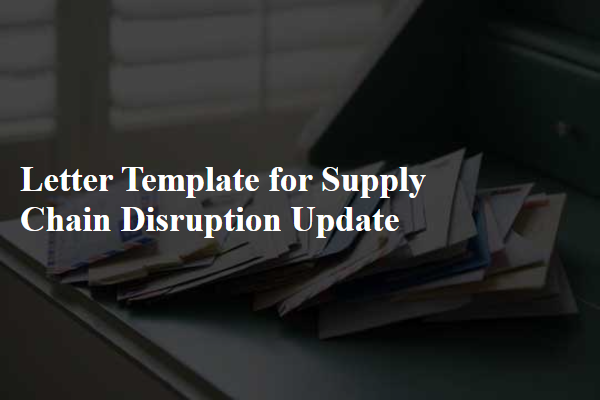
Clear identification of the disruption cause
Supply chain disruptions can significantly impact businesses, particularly in industries reliant on timely logistics. Factors contributing to these disruptions include natural disasters, like hurricanes or earthquakes, geopolitical tensions from trade wars, and global health crises such as the COVID-19 pandemic. For instance, the Suez Canal blockage in March 2021 created substantial delays affecting over $9 billion in goods daily, highlighting the vulnerability of maritime shipping routes. Additionally, labor shortages, particularly due to illness or strikes, can cascade through production timelines, causing ripple effects across the supply chain. Companies must adapt their inventory management strategies to accommodate these unforeseen challenges by diversifying suppliers or increasing stock levels of critical materials to mitigate risks.
Impact assessment on supply and demand
The ongoing supply chain disruption, driven by unprecedented global events such as natural disasters and geopolitical tensions, has significantly impacted the availability of essential goods. Manufacturing delays in countries like China, accounting for over 28% of global exports, have led to shortages in various sectors, including electronics and automotive components. Additionally, transportation bottlenecks due to port congestion in Los Angeles, with container ships sometimes waiting over two weeks to dock, have exacerbated delays. Consumer demand, particularly for home improvement and technology products, has surged by approximately 15% as more people opted for remote work and digital entertainment. This combination of increased demand and reduced supply has resulted in rising prices, with some items experiencing cost hikes of up to 30%. Companies must reassess inventory strategies and explore alternative sourcing to mitigate risks and adapt to this evolving landscape.
Detailed mitigation strategies and actions
Supply chain disruptions have significantly affected global operations, primarily caused by events such as the COVID-19 pandemic and geopolitical tensions. Key sectors, including automotive and electronics, face challenges like increased lead times and material shortages. For instance, semiconductor shortages have delayed production timelines across various industries, impacting companies like Ford and General Motors. Mitigation strategies involve diversifying supplier networks to reduce dependency on single sources and implementing advanced inventory management systems to anticipate disruptions. Companies are also investing in technology, such as artificial intelligence, to enhance forecasting accuracy. Additionally, establishing closer relationships with local suppliers can help increase responsiveness and reduce transportation costs. Collaborative planning with partners across the supply chain is essential to improve overall efficiency and resilience amid ongoing uncertainties.
Timelines for resolution and recovery
Supply chain disruptions can significantly impact operational timelines and recovery efforts. Current events, including the global semiconductor shortage affecting various industries, have led to delays in material availability and increased lead times. Companies like Tesla and Ford are grappling with these challenges, with production halts reported at manufacturing facilities in Michigan and California. Expected recovery timelines indicate a potential resolution by Q2 2024, depending on factors such as freight logistics and raw material sourcing from regions like Southeast Asia. Stakeholders are advised to remain flexible, monitor updates regularly, and adjust production schedules in response to evolving supply chain dynamics.
Contact information for further queries
Supply chain disruptions can significantly impact inventory management, delivery timelines, and operational efficiency. Such disruptions often stem from various factors, including natural disasters, global pandemics, or geopolitical tensions. Companies may experience delays, increased costs, or inventory shortages as they navigate these challenges. Clear communication regarding these disruptions is crucial for maintaining customer trust and managing expectations. Contact information for further queries typically includes designated email addresses, phone numbers, and designated customer service representatives to facilitate timely information dissemination and support.
Comments