In todayâs fast-paced market, ensuring product quality is more crucial than ever. Companies must prioritize rigorous quality assurance processes to maintain customer trust and satisfaction. A well-structured product quality assurance report can be a game-changer, providing clear insights and actionable recommendations. Letâs dive into how to create an effective letter template for your product quality assurance report!
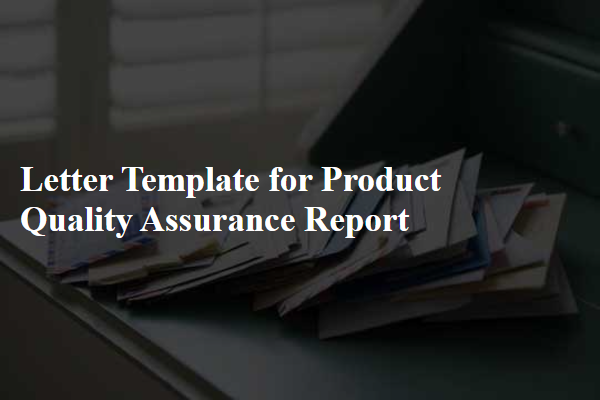
Company Information
Mediocre product quality can negatively affect brand reputation and consumer trust. Establishing a robust quality assurance protocol is crucial for companies, such as XYZ Corp, headquartered in New York City, which specializes in consumer electronics. Regular quality audits, adhering to industry standards like ISO 9001, can enhance production processes. By implementing continuous improvement practices and utilizing feedback mechanisms from customers, including surveys, brands can identify areas for enhancement. Additionally, integrating technological advancements, such as automated testing systems in manufacturing plants, ensures higher consistency and reliability in products.
Product Description and Specifications
The product quality assurance report for the Solar Panel Model SP-3000 outlines the key specifications and features of the device. This high-efficiency solar panel, rated at 300 watts (W), utilizes monocrystalline silicon technology, which allows for improved energy conversion rates of up to 22%. Measuring 1650 millimeters in length and 1000 millimeters in width, the SP-3000 is designed to withstand severe weather conditions, certified with an IP67 rating for water and dust resistance. The panel includes a robust aluminum frame, ensuring durability and stability, while its lightweight construction (approximately 18 kilograms) facilitates easy installation. Additionally, the device comes with a 25-year linear power output warranty, highlighting its reliability and long-term performance assurance for residential or commercial energy solutions.
Quality Standards and Compliance
Quality assurance in product manufacturing ensures adherence to established quality standards, such as the ISO 9001 certification. Compliance with these standards involves rigorous inspections and testing, including both visual and functional assessments. For instance, a factory may implement a quality control checkpoint during the assembly line process, where random samples are selected for detailed analysis. Statistics may indicate that a maximum deviation of 1.5% from the target specifications is allowable, ensuring products meet customer expectations. Additionally, maintaining documentation of compliance audits and corrective actions is essential for continuous improvement, reflecting the commitment to excellence in international markets. Key metrics, such as defect rates per million units (DPPM), contribute to the overall assessment of product reliability and safety standards.
Testing Procedures and Results
A comprehensive product quality assurance report details systematic testing procedures and specific results pertaining to a new consumer electronics gadget, such as the XYZ Smartphone model. Standardized tests were conducted in a controlled environment at the City Tech Testing Laboratory, adhering to ANSI and ISO testing protocols. Performance assessments measured battery longevity, screen durability under pressure (2 kilograms applied), and water resistance (up to 1 meter submerged for 30 minutes). Results indicated that battery life met the expected threshold of 12 hours of active use, while screen durability remained intact without visible damage after 20 drop tests from a height of 1.5 meters onto concrete. Water resistance tests confirmed the device's ability to function post-submersion, with only minor moisture intrusion detected. Overall, the evaluations provided clear benchmarks highlighting product reliability and consumer readiness before market launch.
Recommendations and Action Plan
Product quality assurance reports necessitate thorough assessment and actionable strategies for enhancement. The recommendations should focus on key areas such as production processes, which encompass the methodologies employed from raw material acquisition to final assembly. Implementation of rigorous testing standards (including ISO 9001 certifications) ensures compliance with industry benchmarks. Additionally, staff training programs should be established, emphasizing quality control techniques and error reduction protocols pertinent to the specific manufacturing context (for example, automotive or electronics). An action plan should outline a timeline for the execution of these recommendations, incorporating metrics for success evaluation, such as defect rates and customer feedback scores. Regular updates (such as quarterly reviews) are crucial for monitoring progress and making necessary adjustments.
Comments