We understand that receiving an apology letter for a failed quality inspection may not be what you hoped for, but it's essential to address it head-on. Our commitment to delivering only the best products means we take any shortcomings seriously, and we genuinely regret any inconvenience this may have caused you. We value our relationship and are dedicated to rectifying this situation promptly and effectively. Curious about how weâre improving our processes moving forward? Read more to discover our action plan!
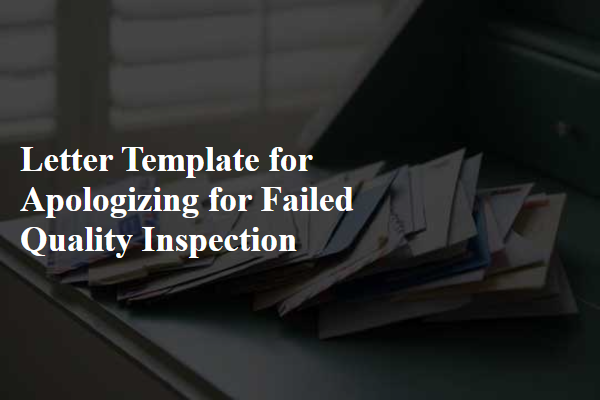
Clear Identification of the Issue
Failed quality inspections in manufacturing processes can disrupt production lines, potentially causing financial loss. Quality assurance (QA) teams often identify critical defects in finished products, which may include misalignment issues or incorrect material specifications. Such defects impact overall product reliability and customer satisfaction, leading to potential recalls or replacements. Specific incidents may involve discrepancies in dimensional tolerances exceeding acceptable limits by more than 0.5 millimeters. This failure necessitates immediate corrective action and a thorough review of the quality control protocols in place. Additionally, investigating the root cause of the failure is essential to prevent future occurrences and maintain product integrity.
Sincere Apology Statement
A sincere apology statement for a failed quality inspection should emphasize accountability, transparency, and commitment to improvement. In recent months, our products, particularly the Batch 2023-003, fell short of the rigorous standards set by the International Organization for Standardization (ISO) 9001, leading to a significant quality concern. This batch, produced in our California manufacturing facility, yielded a 15% defect rate, significantly above the acceptable threshold of 3%. We take full responsibility for not meeting our commitment to quality, particularly affecting our valued clients in the automotive sector. We have initiated a thorough investigation and corrective action plan, involving enhanced training for our quality assurance personnel and a review of our production processes. We sincerely apologize for any inconvenience this may have caused and appreciate your understanding as we work diligently to rectify these issues and restore your trust in our products.
Explanation of the Root Cause
Inadequate adherence to quality standards during the production process led to the failure of the recent quality inspection at the facility in San Francisco. Specifically, machinery used in the assembly line experienced unforeseen malfunctions, resulting in defects in the final products. A total of 150 items, representing approximately 5% of the batch, failed to meet the established criteria set forth by ISO 9001 for product durability and performance, primarily due to inconsistent calibration of equipment. Furthermore, a lack of proper training for the operators contributed to this oversight, highlighting the necessity for enhanced training programs to prevent recurrence. Immediate measures are underway to rectify these issues, ensuring compliance with quality benchmarks and restoring customer trust in our products.
Corrective Actions and Solutions
In manufacturing environments, a failed quality inspection can lead to significant repercussions for product integrity and consumer trust. Root causes often include inadequate quality control processes or lapses in employee training. Corrective actions must be implemented immediately to address the deficiencies. This may involve revisiting quality assurance protocols established by ISO 9001 standards, conducting comprehensive training sessions for personnel, and integrating more rigorous testing methodologies. Solutions such as real-time monitoring systems and data analytics tools can be utilized to identify potential defects early in the production process, ultimately safeguarding product quality. Moreover, stakeholder communication is essential throughout this process to rebuild trust and ensure transparency regarding steps taken to rectify the situation.
Assurance and Future Prevention Steps
Quality inspection failures can significantly affect product reliability and customer satisfaction, particularly in manufacturing sectors such as automotive or electronics. These inspections, conducted by certified professionals, are essential in ensuring compliance with established standards, such as ISO 9001. Upon discovering discrepancies in recent batches, immediate corrective actions were implemented, including thorough re-evaluations and additional training for quality assurance personnel. Implementation of a new quality control protocol will mitigate future risks, incorporating advanced statistical process controls and regular audits to enhance product consistency. Regular feedback loops with suppliers will also be established to ensure raw materials meet stringent guidelines, resulting in a significant reduction in defect rates and enhanced overall quality.
Letter Template For Apologizing For Failed Quality Inspection Samples
Letter template of acknowledgment for inadequate quality control results.
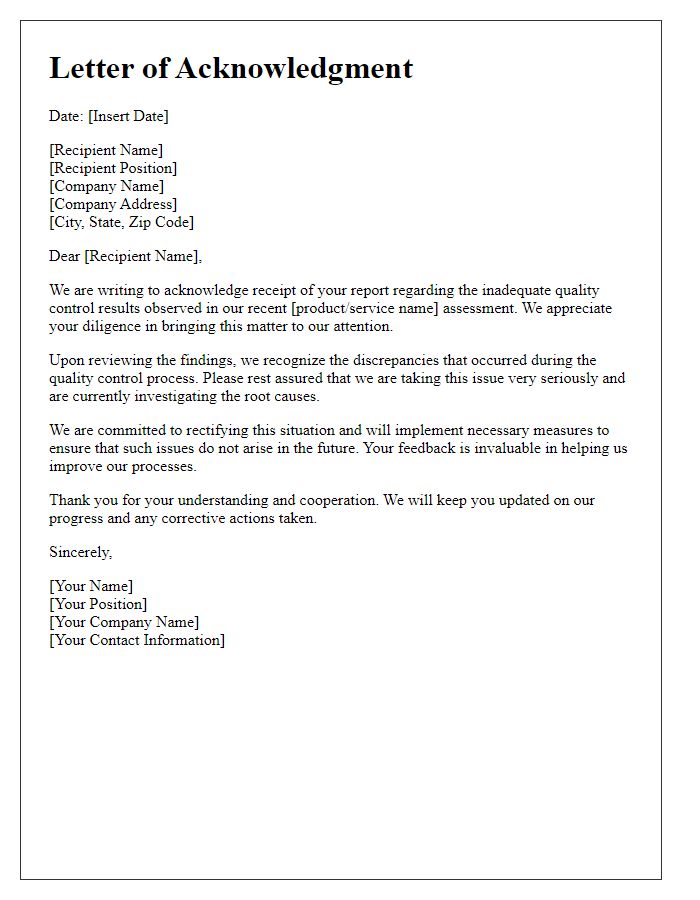
Letter template of commitment to improving quality after inspection failure.

Comments